Excited about RCM?
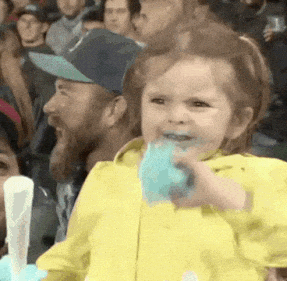
One of the Biggest RCM Misconceptions: You must have comprehensive “historical data” in order to carry out RCM
Historical data is important for an RCM analysis. But the kind of data that is generally collected isn’t sufficient to answer all the questions in the RCM process – and thereby formulate specific solutions.
Let me show you what I mean.
The kind of data collected for assets can be likened to baseball statistics. (I can’t help it. As a native Bostonian, I was brought up by fanatical Red Sox fans!)
The figure below presents a season’s batting statistics for player Smith.
Player Smith’s batting average is .204 which means the batter gets a hit approximately twice out of every ten at-bats. He has 21 runs batted in (RBI) and six homeruns. A batting coach can review this data and conclude that batter Smith needs improvement.
This is valuable information because now the batting coach knows where resources need to be designated (i.e. helping batter Smith to improve his performance).
However, what the batting coach cannot deduce from the data is what is “causing” batter Smith to perform poorly (think Failure Modes…). So, the coach cannot formulate specific solutions to help the batter improve based on the data alone.
For example, should the batter start to swing a little earlier? Or maybe a little later? Or maybe the batter needs to change his stance? Those questions can’t be answered solely by evaluating the data.
Historical data for assets is often of the same ilk. For example, a review of bearing data can reveal that 50 bearings were replaced last year (up from 20 last year). From this, the equipment custodian can conclude that there is a problem regarding the bearing.
However, what specifically caused the bearing failures cannot be identified simply from reviewing the data at hand.
For example, were the bearings greased improperly? Were they not greased at all? Was the wrong grease used? Was there a manufacturing defect? Were the bearings fitted improperly?
There are many issues that could specifically cause the bearing failures.
So, while the data is valuable because it allows an equipment custodian to zero in on problem areas and thereby allocate resources where they can be of most benefit, the data doesn’t reveal exactly what is causing the bearing problem.
Generally speaking, historical data often falls short because it typically:
- Reports only what failed
- Describes what was done to repair the failure rather than what caused it
- Doesn’t describe failures that are currently being prevented or plausible failures that haven’t occurred
- Describes failures which may be the effect of some other failure
- Offers inadequate information for determining On-Condition, Restoration, and Replacement task intervals
You may be wondering, well then, where do we go from here? If historical data is often inadequate to perform an RCM analysis, where can an organization turn to get the information?
(Don’t worry. RCM’s got you covered.)
Organizations can capture an enormous amount of information by asking the right people – those who are most intimate with and knowledgeable of the asset and the operating environment in which the asset is expected to operate. This is one of the most valuable tools in any RCM analysis.
These equipment experts make up the RCM Working Group and represent the various disciplines applicable to the analysis at hand.
The figure below depicts an RCM Working Group assembled to analyze a boiler.
When an RCM Working Group is gathered, there are typically over 100 years of cumulative experience at an organization’s disposal!
Because of the vast and varied experience and perspectives represented, it is a unique opportunity to “acquire” the kind of data needed to formulate solutions that can make a remarkable difference to the organization.
By turning to people who know where the improvement opportunities are, a skilled facilitator can use RCM principles to consolidate their knowledge and lead the experts in formulating solutions that can have a powerful impact on the organization.
(In my next post, I’ll talk about some of the amazing benefits of a Facilitated Working Group approach to RCM!)