Lean Digital Factory – A Blueprint
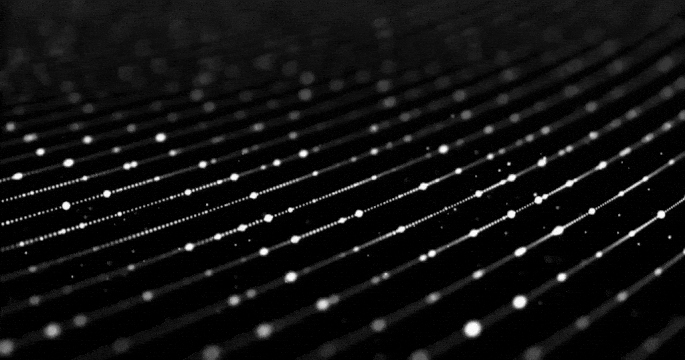
CHAPTER 1: The Setup
Abstract
Guided by factory needs, the LDF network provides direction & solutions for the digitalization journey of DI plants since 2016. By using own HW/SW products & solutions LDF has so far increased their productivity by low three digit MEUR and as recently shown even their resilience in times of a pandemic. While plants from different industries had to close, the output of DI plants was affected by only ~10% and back to normal quickly.
Supported by jointly created road maps, an alliance of >200 experts are working together to leverage new technologies. To guide employees in the digital transformation, even a dedicated learning channel was set up.
Winning several industrial awards, LDF supported to position Siemens as digital thought leader in the market and provided the blueprint for the Siemens-wide Factory Digitalization program with the mission to generate additional business with external customers.
Lean Digital Factory – A core program for the factories of Siemens Digital Industries
As complexity increases and business models change, traditional improvement methods must be augmented with digitalization, which is key for efficiency, flexibility, and speed. Successfully mastering digitalization is complex and requires high efforts. Sharing the burden by bundling expertise of the world-wide DI manufacturing network and our own solution providers while using our own solutions & products, LDF took thought leadership in 4th Industrial Revolution (4IR) technologies.
Our core program Lean Digital Factory is embedded in our framework of core programs „production and logistics excellence, in which we address all aspects of a role model factory from lean philosophy, employee engagement, plant network design, supply chain design and supplier collaboration.
The major benefits we have already achieved beside significant productivity increases are synergies, balanced workforce and capacity, speed learning and a reliable supplier base even before covid19 shocked the world.
This was possible because all plants are sharing one mission, to be the role model for excellence in production and logistics to provide proven value add for our customers, based on the methods of a digital enterprise and lean industrial engineering to master the challenges we face in manufacturing: to shorten our time to market, to increase our flexibility, to continuously improve our quality and to boost efficiency by increased security and sustainable operations.
We started this journey 2016 and since then, our factories are known internationally as digital lighthouse and received several recognitions. The factory in Chengdu, China and our factory in Amberg, Germany are rewarded as WEF Lighthouse factories and both facing challenges like serving 60.000 customers, producing 1 product per second with almost 6 sigma quality by having already reached full vertical and horizontal data integration.
In the year before the pandemic breakout, some DI factories pulled almost 10000 visitors per year, and therefore we were building a state-of-the-art digitalization center in Amberg which opened their doors for our customers in May 2021.
Figure 1: Motivation of Lean Digital Factory
Our core program “Lean Digital Factory” (LDF) was initiated to strengthen the focus further on automation and digitalization and shop floor productivity from data and analytics based on lean production philosophy.
The journey to become a lean digital factory always begins with becoming a lean factory first and can be characterized by several lean rules stated 1999 by Spear and Bowen.
One rule is known as that all work and process steps, shall be highly specified as to content, sequence, timing, and outcome. With other words, processes must be described without any waste, but in difference to the past, artificial intelligence and machine learning can be used to make them even more efficient.
Another lean rule states, that every customer-supplier connection must be direct, and there must be an unambiguous yes or no to send requests and receive responses. This can be realized very efficiently with defined digital supplier interfaces with standard communication protocols for tracking and tracing.
From the plant development point of view, the third and most important rule states, that any improvement must be made in accordance with the scientific method and at the lowest possible level in the organization.
From the very beginning, the empowerment of our people to drive and own data driven projects was key. So, our people started by using data to measure, track and optimize our quality for example down to a 5sigma level already with 9-11 dpm. This means, in our DI factories we are working with data to continuously optimize our processes. But one should be aware that one cannot introduce technologies on higher frequency than up- and re-skilling of the people who are going to use this technology.
Due to the reason that we are doing continuous improvement projects since a long time, the amount of shop floor productivity projects increased dramatically over the years to maintain the level of productivity we needed to stay competitive. To focus further on flexible automation with light weight robots and to address automation tasks was one focus. The next level of productivity, which we are reaching right now, is with further digitalization, which automates also administrative and engineering topics and due to shop floor IoT like augmented and connected workers and artificial intelligence (see also figure 1).
Our digitalization approach, which addresses more than 30 factories worldwide was started with an ideation phase, of course we had to define a certain program organization to assure best-practice and solution transfers as well as scalability. The main topic was to define which technologies we want to focus on and which not and how to prioritize. Therefor several technological workshops, expert interviews, visits and so on as well internally as externally have been conducted.
With so called technology radars, technologies have been evaluated economically. In parallel, we defined reference processes, as north star processes which have been released for orientation. Interesting could be, that we never expected that all plants will reach the reference processes at the same time. The focus was that all plants have an orientation for technology, software, and IT investments.
The overall elaborated “Digitalization Roadmap” finally consists out of five work streams flanked by an IT roadmap, solution link analysis and technology stack architecture for state-of-the-art connectivity and data mining.
The realization phase, in which we are now for almost three years can be described as an agile working mode with sprints and backlists. The implementation of solutions by itself are done via three major milestones “Proof of Concepts”, “Pilots” and “Scale Up Phases”. Nowadays, ~25% of our productivity measures are coming from LDF and the tendency is increasing, pushing our LDF plants to a level of up to 7% shop floor productivity per year and the recipe for our success can be seen in the generation of ready to scale up solutions by bundling the power of our manufacturing network to jointly develop and share solutions and to learn from each other by copying with pride.
The five workstreams, who are forming the overall roadmap also serve our digital factory vision, which contains out of the digital twin, which by itself can be divided in a digital twin of product, of production and performance.
What are now the five workstreams. The three workstreams “new ways of working”, “robotics” and “big data & analytics” can be seen as enablers while the workstream “digital twin” and “processes” serve the vertical and horizontal data integration with its respective reference processes.
Figure 2 shortly explains, what a roadmap on the highest level contain.
Figure 2: Generic digital roadmap
In figure above you see a roadmap on high level for a generic workstream with a timeline. Each workstream line addresses a defined target state and a trend, which is helpful for communication reasons. The boxes describing an evaluation state, which should be reached, the numbers are pointing to projects, with a defined timeline and project lead and group as well as a budget. Sometimes the project is a cluster of several single projects, who belong together.