Aaron Merkin with Fluke Reliability
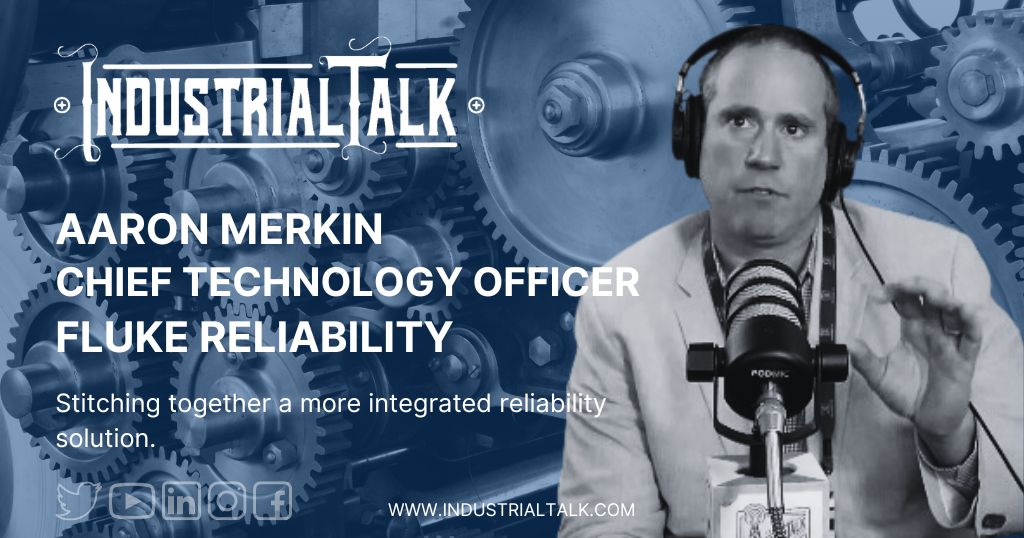
Industrial Talk is onsite at Xcelerate 24 and talking to Aaron Merkin, Chief Technology Officer with Fluke Reliability about “Stitching together a more integrated reliability solution”.
Aaron Merkin discussed the shift from on-premise to cloud software and the integration of AI in enterprise software. Scott MacKenzie and Aaron discussed the importance of data collection and closed-loop workflows for predictive maintenance, highlighting the benefits of modern applications like x5 and the potential of generative AI and augmented reality in asset management and maintenance. The conversation emphasized the challenges of navigating disruptive times in the industry and the need for comprehensive solutions to eliminate unplanned downtime and improve worker efficiency.
Action Items
- [ ] Reach out to Aaron on LinkedIn for more information on Fluke's solutions.
- [ ] Consider migrating to x5 platform to close the maintenance lifecycle loop.
- [ ] Continue investing in generative AI and augmented reality technologies to further automate workflows.
Outline
Industrial software and AI with a former CTO.
- Aaron Merkin, discusses his role as Chief Technology Officer (CTO) at Fluke.
- Aaron shares his experience taking his family to Washington, D.C. for spring break, including visiting museums and memorials, and watching the half marathon.
- Aaron discusses their experience in enterprise software and industrial software, mentioning their roles in various companies such as AWS, Clara, and Honeywell.
- Aaron shares their insights on the disruptive nature of the current time and how they helped Honeywell navigate through it.
Connected reliability and predictive maintenance workflow, with a focus on Fluke's Xeno and EMA acquisitions and their impact on
- Fluke reliability is expanding its approach to connected reliability, focusing on predictive maintenance workflows and integrating systems to provide value to customers.
- Fluke acquired Xeno and EMA to enhance its portfolio with AI and measurement technologies to improve data collection and workflow management.
- Aaron: X5 platform improves closed-loop maintenance with modern, easy-to-use mobile capabilities.
- Aaron: X5's mobile capabilities shorten time to productivity for new joiners in industrial facilities.
AI-powered predictive maintenance software for industrial assets.
- MacKenzie: Technology bridges skills gap, improves efficiency.
- Aaron: Closed-loop workflow automation for efficient asset management.
- Aaron discusses the benefits of using x5 quality PM management annex, including reduced backlog of maintenance activities and improved first-time correction.
- Case study highlights the effectiveness of x5 in addressing issues such as lack of prioritization, poor work instructions, and inadequate spare part information.
Asset management, maintenance, and reliability solutions.
- Scott MacKenzie: Electronic work packages can improve maintenance tasks (15 words)
- Aaron: Creating an ecosystem to help customers prioritize technology (14 words)
- Aaron Merkin: Leading industry direction with integrated solutions.
- Scott MacKenzie: Building platform for industrial professionals through education.
If interested in being on the Industrial Talk show, simply contact us and let's have a quick conversation.
Finally, get your exclusive free access to the Industrial Academy and a series on “Marketing Process Course” for Greater Success in 2024. All links designed for keeping you current in this rapidly changing Industrial Market. Learn! Grow! Enjoy!
AARON MERKIN'S CONTACT INFORMATION:
Personal LinkedIn: https://www.linkedin.com/in/austintechsaas/
Company LinkedIn: https://www.linkedin.com/company/fluke-reliability/
Company Website: https://reliability.fluke.com/
PODCAST VIDEO:
OTHER GREAT INDUSTRIAL RESOURCES:
NEOM: https://www.neom.com/en-us
Hexagon: https://hexagon.com/
Siemens: https://www.siemens.com/global/en.html
Palo Alto Networks: https://www.paloaltonetworks.com/ot-security-tco
Palo Alto Networks Report HERE.
Hitachi Digital Services: https://hitachids.com/
CAP Logistics: https://www.caplogistics.com/
Industrial Marketing Solutions: https://industrialtalk.com/industrial-marketing/
Industrial Academy: https://industrialtalk.com/industrial-academy/
Industrial Dojo: https://industrialtalk.com/industrial_dojo/
We the 15: https://www.wethe15.org/
YOUR INDUSTRIAL DIGITAL TOOLBOX:
LifterLMS: Get One Month Free for $1 – https://lifterlms.com/
Active Campaign: Active Campaign Link
Social Jukebox: https://www.socialjukebox.com/
Industrial Academy (One Month Free Access And One Free License For Future Industrial Leader):
Business Beatitude the Book
Do you desire a more joy-filled, deeply-enduring sense of accomplishment and success? Live your business the way you want to live with the BUSINESS BEATITUDES…The Bridge connecting sacrifice to success. YOU NEED THE BUSINESS BEATITUDES!
TAP INTO YOUR INDUSTRIAL SOUL, RESERVE YOUR COPY NOW! BE BOLD. BE BRAVE. DARE GREATLY AND CHANGE THE WORLD. GET THE BUSINESS BEATITUDES!
Reserve My Copy and My 25% Discount
Transcript
SUMMARY KEYWORDS
work, customers, asset, technology, industrial, reliability, workflow, ai, Fluke, aaron, plant, maintenance, facility, Xcelerate, workforce, software, changing, rbg, shift, pull
Welcome to the Industrial Talk Podcast with Scott MacKenzie. Scott is a passionate industry professional dedicated to transferring cutting edge industry focused innovations and trends while highlighting the men and women who keep the world moving. So put on your hard hat, grab your work boots, and let's get all right.
und. We are on site Xcelerate:Chief Technology Officer CTO?
Let's get cracking. It's a good meeting. Were you here last year? Unfortunately,
not. I had a spring break for my kids. So I had to watch Bill Washington DC. Or half a classic and my wife, wife and daughter in the Marine Corps half so
yeah. We did that with our kids. Yeah, you have to it's just one of those things. Yeah. We did do so you took in all of the museums and a
good number of museums and memorials. Watched America watch the half marathon. We packed a lot in in about a week or so. Yes, it was really good trip. Did
you go to Arlington? We
did and waited for the changing the guard. Yes. And it was actually I don't know if it was the first or there was gonna be the kind of last but was one of the one of the times was a female marine who was doing it? No way. Yeah, it was really, that that is just absolutely moving. Just it's it's I
just pulled it up on YouTube just to watch it. Yeah, no, that's it. Did you see the the Mount Suribachi, the raising of the flag that it's the classic taking the flag sticking in the ground? And the huge?
I don't think so I think we just saw the changing of the guard. And then went over to see this RBG RGB Berry, the Ruth Bader, Ruth RBG. Ruth Bader Ginsburg buried there. I think so I think we saw oh, I need to check. I think that's what we went to see her like, it's a very private, sort of small, talkback spot. And then there's a reflection, we went from, like our selection to whatever reason, okay, or something, I forgot what it was. But the changing of the guard was absolutely just,
it's, they don't mess around. They don't don't even think about making noise.
But I think that the thing that it's like one of the most selective duties in the Marines, because it's just because of the the honor associated with it. And for me, like I didn't grow up with it. I didn't grow up very much. Nobody my family is in the military with did not really grow up. She's super patriotic. But as you get older, of course, you get a bit more for that. And so something like that, when you see people like people who are so devoted to it, it just inspires you in yourself to kind of raise your level of patriotism.
No, it does. It's spectacular. All right. Before we get into our conversation about what all the happenings happening here at Xcelerate, for the listeners out there, Aaron, just give us a background just who you are.
I'm a so I've been working in enterprise software and industrial software are about 26 years the last 13 or so industrial software. I started my career very innocently as a software developer and worked my way up through a variety of management roles and architecture roles, was the CTO for AWS enterprise software group, and led a lot of their efforts to drive the shift from an on premise software into SAS. into cloud software. It's actually a combination of pure play cloud native applications lift and shift and some of the traditional EDM applications, as well as a bit of expansion. For some of the simulation software, we use cloud services for scaling purposes. Move to an AI company called the Clara and built out their very first cloud offering as well. And the meter data smart meter data management solution, incorporated some first pass and incorporating AI into an offering to help them shift from a private equity ownership to strategic ownership with Hubble and then move to Honeywell just at the end of the pandemic and spend some time with Honeywell, helping them navigate a very very disruptive time of time.
It's still disruptive. It still is still amazing. Amazing. So with that said, mad skills, great street cred absolutely wonderful stuff. So with that said, we look at connected reliability, right? We just So everybody is talking about connected reliability. And I think the conversation has changed even in a year. It's changed. We have the advent of AI, other tools. Take us through a little bit about what what is happening within, you know, Fluke reliability from the connected point of view,
I think we've Fluke reliability has was kind of, obviously the inventor of the concept of the approach to the industrial maintenance of Tech's reliability, we had initially taken maybe one more narrow view that I think is really appropriate for our customers more focused on sensors, and just as CMMS software, and really heavily tailored around what we have in our portfolio, quite honestly. And what we've tried to shift to do is to take a much broader view and understanding all of the customer problems that customer problems, customers have these systems of record that they have the right to hold information about the processes, and start looking at how can we stitch together much more, or help them stitch together a much more comprehensive philosophy about how they integrate those systems and how they solve their problem, right, as well as obviously bring ourselves in to try to provide additional technologies to advance them on that path. So we've sort of the, you know, the acquisition of the Xeno allowed us to bring in a leading edge artificial intelligence platform. And when we think about connected reliability, we think about connected reliability. Again, it's a very broad ecosystem. It's a way of structuring your L two and L three software system, a little devel, four to kind of software and systems up and down your technology stack. And bringing them together derive insights, we've chosen to focus on the predictive maintenance workflow as the primary workflow. We think that that that is the first place to eat and create value for customers to eliminate the effectively addressed unplanned downtime, as well as increased worker efficiency. And particularly as you're looking at some of the mega trends around skill shortages, you're not having people in the plant to do the work. We think that by having that closed loop workflow, we can provide the most value. And that's why we have the acquisition of EMA in our portfolio, which allows us to then help you more effectively plan and manage your work. Variety of measurement condition monitoring, measurement technologies will allow you backhaul data, the corporation is EMA allows us to help customers scale that data collection across the balance of plant very cost effectively. It also has because of the deep expert system functionality it has, it's able to be very prescriptive about diagnostics, versus just setting up a lot of people in the industry are taking red, green, yellow, and you're not really able to do much with with that except eight. Okay, great for scheduling and inspection. Work Order will be there for script prescriptive about the fault, which allows you then to send somebody else to do their own action, correct preventive maintenance with the right parts of corrective maintenance with the right parts, and shorten the time to repair. And then with our portfolio of alignment tools from protect, Nick, obviously, after you've adjusted any kind of electoral equipment, you need to rebalance that, realign it, and then sweep to get them to get the machine back to healthy RUNNING state and let's begin through email, we're able to have that closed loop, you've detected a problem, create a work order you perform the work you perform the maintenance activities to correct the problem. And now you're confident that it's been corrected. Having that closed, is I think something that is really valuable for customers to begin to really nail down that predictive maintenance workflow, and then start expanding into other opportunities for efficiency gains.
How does that mean? You have email, you have the the next version of it? 5x 5x x 5x 5x? Five? Yeah, I stumbled on that x five. That's right. That's an X version. Are you are you seeing more companies, a lot of the users here looking at migrating to the x five, and does the x five platform sort of serve or, or improve that closed loop with that objective?
So I think there's a couple things, but we definitely see the technology refreshed the Kleenex for next time. It's a much more modern, compelling application. You've invested heavily in a better mobile experience. And if you think about some of the mega trends that we're talking about here, Xcelerate, you know, one of those trends, again, is the absence of making any kind of you can kind of talk about whether it's skilled workforce or knowledgeable workforce, like you can be technically proficient but know nothing about a plant. But what we're trying to do is through the mobile capabilities of x five and the heavy investments we've made an ease of use, we have a actually a V a UX lab here where a customer is able to actually give us direct feedback on the product. Because that those investments we've made, we think that we are shortening the time to productivity of staff of new joiners into an industrial facility. So that's one of the I think one of the most compelling things about E maintenance is going to help cost bombers because of that improved ease of use because of it's just the general that the the mobile capabilities we have, it'll help them onboard a lower skilled workforce much more quickly. So it's a huge advantage in the market.
And correct me if I'm wrong, that's a big topic outside of the fact that I know just the workforce and the challenges with the workforce and the churn of the workforce and skilled workforce. So. So Fluke, reliability, is seeing that as a major problem, but through technology, being able to sort of bridge it and help individuals who have the skills be more productive, like like, like your new AI product allows allows, it allows the vibration individual to see what is really needed. But I'm not getting inundated with all the other stuff, I think just a little bit more efficient.
I think if you think about the we're taking really more of a two pronged approach. So the the event is x five and the evolution that we have there, it's really all about the direct technicians and operators in the plant, making them more efficient, making it easier for them to understand what they need to do to complete the tasks. And we have some future work that we're doing to incorporate much more copilot technology, the next generation generative AI to make that even easier for them where they're getting, they're able to get prompted in terms of the types of work that they need to do. So that's like a problem. In the short term, we've got a great strength there an area for us to build. On the other side with the Zeeman acquisition, there's really two approaches to it, you can as a as a customer who has vibration analysts, you can choose to use our tool suite to make your own vibration analyst more efficient. However, we really think that the better there's more value creation for customers, by obviating the need for them to have those vibration analysts, we have a incredibly powerful, powerful algorithm that is highly predictive. Behind that we have a workflow that has our cat one and cat two certified migration analysts who are validating the results. And in the know, in the case of very, either a very severe fault or afraid maybe customers may take action on it turns out it's not. Or in the case of maybe just a bit of an input ambiguous diagnosis, then we're using our own cat three and cat four certified personnel to provide that last mile sign off. So we believe that rather than customers trying to upskill in this area, or even tried to horizontally scale their their workforce, they're much better at working with us to get a comprehensive solution, which is this is the lead time portfolio for your asset, this is likely the thing that's broken. And here's how you can take action on it through incorporation with a CMMS of actually creating the workflow the work order with the pm that needs to be done.
Is it heavy lifting? If I'm going to try to create that closed loop does, did x four be able to do it? Or does x five do a better job because you have the mobility component? So
over time, we've put this cape, it's possible in those but obviously, we'll be investing over time, in our next generation product will continue to drive the usability enhancements and new integration hands was there.
Yeah, I just see that that's we're getting to a point and correct me if I'm wrong, Aaron, we're getting to a point where if I have the predictive capability, being delivered to from a device, to a machine learning or AI component, determining the health of that asset, creating that work order, I haven't, I don't have any human interface interface right now, creating that work order, then I have to go into the human, you know, depending on like here, go work on this particular valve or pump or whatever. And then being able to mobile and close it out. That's where the handoff and that's the efficiency of efficiency
of it is is that we are able to extract effectively the customers human beings from the full workflow of data collection, through prescriptive diagnostic of what may need to be done, help improve the efficiency of which those that that Pm is created through the quality of our RPM management and work order management and automate. And again, as I say, kind of closed loop all the way through so you're confident in the facility that you understand that the work was completed. And there's longer term benefits even that it's an episode that we've taken out some of your higher level maybe will I reliability engineer skill sets, reduced your need for them. The next thing is is that to talk about sort of the shift from the skills gap. You can have electric qualified electrician to know how to diagnose diagnose and repair prepare, generally a machine but what you often have is a knowledge gap. There's very specific assets are run in a specific way configure a specific way in your plant, and I can bring in somebody from outside who has those skills, they know how to sort of repair a compressor or blower, they don't have the knowledge, they don't know how mind behaves. So the next thing that went as I said, the next thing we're working on doing is incorporating much more of those copilot technologies, where we're able to look at historically how have work orders been been been processed in your plant for your asset type, what types of PMS have been effective, what type what steps and corrective maintenance are performed or not performed, so that you're able to take that skilled person in pre armed them with the knowledge of how to apply their skills to a specific asset asset instance in a customer's facility.
Does this also address in many companies right now there's the backlog the work order backlog that nobody ever gets to this sounds to be a greater efficient way of being able to really tackle have a good work order, tackle the task at hand, get it done. And it'd be able to plan around that versus a went out to that asset, I looked at it, it was vibrating or it was heating up. And then I created a work order. And that's where
we have a great case study I have here we are the quality of pm Management Annex five is yielding significant results for our customers in terms of their ability to burn down their backlog of, of maintenance activities. And some of this, they don't know what they need to appoint. They don't know what needs to be done. They don't know the priorities. They may or may not have associated spare part information so that they even you know, they go out when they go out. And they do that they do the work. They don't they don't bring the right parts. And by implementing x five, we're able to fix all those things. Right, prioritize them, ensure they have quality work instructions, have a tight schedule for them, try to help pre arm you with the assets and the information that you need. So when you go out there, you have a much higher first time correction.
Well, that's a whole nother conversation being able to have the right, kidded you know, equipment, the right tools, because how much time is wasted just because I don't have or my my, like, work order has been cannibalized or whatever it might be. Are you
familiar with electronic work packages? That? Yeah, I think we, I think that that's where the future is going in terms of being able to take the richness of electronic workpackage That may be something you'd only ever supercritical assets like a turbine or grind turbines and power generation facility. I worked with ABB we did a lot of work supporting nuclear reactor maintenance and repairs reliability. So those types of assets, you'll invest very heavily and all the prep work, that that electronic work package, I think with the incorporation of generative AI will be able to bring that same richness of information and preparedness to even standard maintenance tasks in some in you know, much less complex facilities, perhaps, you know, food and beverage facility.
I was at an event and we were talking specifically around augmented reality and applying augmented reality to the actual work being performed. And that's, that's interesting, too, as well.
It's that's a it's I'm curious to see where that goes. It's an idea whose time has been coming for a decade. Yeah.
I stood on a pair of glasses just sort of look like my glasses, but chock full attack, right. And what was really interesting was the simple fact that I was able to pull up up a 3d drawing of an asset, and then walk around it. Yep. Just look closer, pull back. And it was clear. And, and from a safety perspective, I knew that I could say, Okay, I need to work on that. There it is, anyway. Bad technology coming your way.
There's a it's, it's an embarrassment of riches. And, yes,
that's interesting. That's a good term. You're absolutely right. I think for me, personally, is like, where do you start? It's just so much. Who do I trust? Where do I start? You know, I want to do it. But do I? Where do I go? You know, what do I try?
And I think, you know, this is part of the thing. We talked about connected reliability. And I think the that the idea of creating an ecosystem is help is also helping to help customers understand the workflows and use cases and how to help them prioritize and what technology is available. And obviously, our ambition is to be your trusted provider for everything MRO related. Yeah. But really, what we take pride in is much more trying to help lead the industry, lead the industry, help the industry understand the right direction to go when framing for plenty of people. So even if our customers don't take tech from us, or that we don't have the tech that they need for their next generation, that they at least are out there understanding what's possible and they can take a look available avail themselves.
e broadcasting from Xcelerate:You're listening to the Industrial Talk Podcast Network.
Aaron Merkin, Xcelerate: