Brad Nanna with IRISS
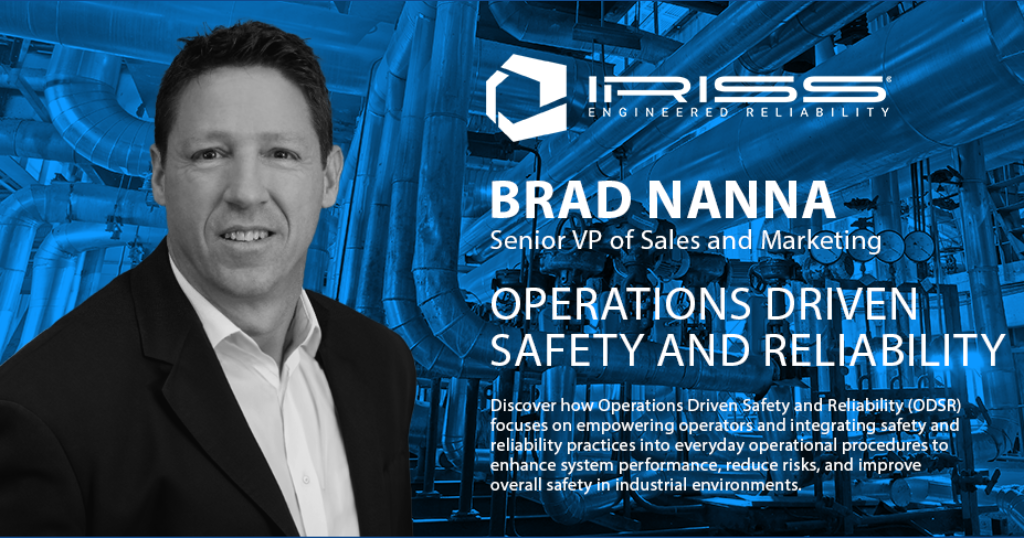
Lee Murray hosts a podcast episode discussing Operator Driven Safety and Reliability (ODSR) with Brad Nanna, Senior Vice President of Sales and Marketing for Iris. ODSR empowers operators, who are closest to the equipment, to identify and address potential issues before they become problems, reducing downtime, costs, and risks. The approach combines elements of condition-based and preventive maintenance, emphasizing operator involvement over traditional maintenance programs. Training for ODSR includes safety protocols, environmental awareness, communication skills, and continuous process improvements. Resistance to ODSR stems from a shift in mindset and management practices. Safety devices are crucial for maintaining safety and reliability in ODSR.
Action Items
- [ ] Address potential sources of resistance to ODSR like changing traditional mindsets.
- [ ] Discuss how electrical safety devices factor into ODSR.
- [ ] Continue future podcast discussions on ODSR in more detail.
Outline
Introduction to Operator Driven Safety and Reliability (ODSR)
- Lee Murray introduces the podcast episode, focusing on operator-driven safety and reliability (ODSR).
- Lee welcomes Brad Nanna, Senior Vice President of Sales and Marketing for IRISS, to discuss ODSR.
- Brad Nanna explains that ODSR is about empowering operators to take ownership of equipment and processes.
- The goal is to allow operators to identify potential issues and implement corrective action plans before problems occur.
Empowering Operators Over Traditional Maintenance Approaches
- Lee compares the operator's close relationship with equipment to a car owner's familiarity with their vehicle.
- Brad Nanna discusses the traditional maintenance programs: break-fix, time-based, and condition-based maintenance.
- He explains that ODSR combines elements of condition-based maintenance and empowers operators to act on issues.
- The focus is on operators, who are closest to the equipment and best suited to address issues efficiently.
Training and Skills for ODSR
- Lee inquires about the specialized training required for operators involved in ODSR.
- Brad Nanna outlines the training needed, including safety protocols, environmental awareness, and communication skills.
- He emphasizes the importance of continuous process improvements to enhance safety and reliability.
- The training program aims to save time, resources, and money while ensuring safety and reliability.
Challenges and Resistance in Implementing ODSR
- Lee asks about potential sources of resistance when implementing ODSR.
- Brad Nanna identifies a change in mindset as the primary challenge, requiring a shift from traditional maintenance approaches.
- He stresses the importance of involving operators, who are often overlooked in traditional programs.
- The goal is to help facilities and plant managers think differently about safety and preventive maintenance programs.
Integration of Safety Devices in ODSR
- Lee asks how electrical maintenance safety devices fit into the ODSR concept.
- Brad Nanna explains the importance of safety equipment and protocols in ensuring safety at work and home.
- He mentions various associations, such as NEC, NFPA, IEEE, and NESA, that provide safety standards.
- The focus is on keeping people safe while maintaining facility uptime and protecting mechanical and electrical assets.
Conclusion and Future Discussions
- Lee thanks Brad Nanna for the overview of ODSR and expresses interest in discussing it further in future podcasts.
- Brad Nanna encourages listeners to reach out to Iris for more information and support.
- Lee concludes the podcast, thanking the audience and signing off.
Transcript
SUMMARY KEYWORDS
maintenance, operator, reliability, processes, safety, condition based maintenance, facility, program, iris, electrical, equipment, lee, safety protocols, outages, engineer, podcast, change, maintenance procedures, cost, great
Lee, hello and welcome to this episode of the podcast. I'm Lee Murray, your host for the next few episodes, and I'm excited to be here to explore the world of reliability in electrical and mechanical systems. In today's episode, we're going to chat about a novel and exciting approach to safety reliability that's picking up speed in the world of Facilities Management. The concept is called operator driven safety and reliability, or odsr for short, and we have just a man to talk about it. Joining me is Brad Nana, Senior Vice President of Sales and Marketing for Iris. Brad, welcome back to the podcast. Yeah,
o looking forward to the next:is odsr in a nutshell? Then? Bren,
yeah, that's a great question. It's a change in our processes and thinking and how we do maintenance in odsr, obviously, Lee, you said it. It stands for operations driven safety, reliability in an essence, what we're trying to the message that we're trying to deliver here at Iris is we want to empower the operators. They're the per they're the people that are closest to the equipment, that know it the best in the industry and in the facilities that they that they're employed by and that they work at. But it's given them the ownership of the equipment, the processes that allows them to identify the potential issues and implement corrective action plans before a problem even occurs. Well,
that's great. It makes me think about the person being closest to the closest to the equipment. It makes sense, because I think about me and my car, and I know when there's something happening with it. You know, more than my mechanic does, because I'm close to it. I'm with it, 24/7, and I know it inside out. So that makes a lot of sense, why the focus on operators instead of their maintenance team? Yeah, it's
another good question. So you know my experiences, I started many years ago as a service engineer, and we provided maintenance work normally during scheduled outages. And what we know about the at least on the electrical side, and you can apply it to the mechanical side as well. When you have an unscheduled outage, it costs a lot of time, resources and money. There are four maintenance programs that we are aware of, and the four being a break fix mode, which is also run to failure, absolutely cost you an extreme amount of time, resources and money. And are, are are the least effective way to do a maintenance program. The second one, which we would call is a time based or planned preventative maintenance, so you're going out during outages, scheduled outages to do some type of plan, preventative maintenance, work to keep it running for a very long time. Again, not a bad practice. We would actually it's a good practice, but cost, time, resources and money. The third one is what we call condition based maintenance, and it's the way, the best way I can describe a condition based maintenance is that's your check engine light that comes on your vehicle. Okay, now I have condition. Now I know I need to go out and do some type of maintenance. So as you can see, we're progressing further along in establishing maintenance programs that are safe, that are more reliable and less downtime, less resources and less time and less money. And then best of all is what we call an operations driven safety and reliability. So it's taking those two previous one, which is the plan prevent the maintenance, and it's taking the condition based maintenance program, and now it's given direct access to the operator, in which we said earlier, they're the ones that know the equipment the best, and they can fix it in a very timely, efficient, productive way, and that's the main focus of having the operator involved in the program, not the engineer, the facility engineer, not the facility maintenance person. We know there's one or two to dozens of operators in a facility, and certain. Not the plant engineer, so taking all those tasks that those three individuals do and then empowering the the operator to do that, to do that work. Very
cool, very interesting. That's a that's beautifully put as well. What it makes me think, what kind of specialized training do you need to have for operators involved in no? DSR, yeah, we're
trying to demonstrate, and we do it here in our own facility. We're a manufacturing facility, irises, and in in in Florida. But you know, it's special instructions and processes. And the instructions and processes are on equipment tolling and handling safety protocols. So what are the safety protocols that you that you must comply to the environmental awareness, being aware, situationally aware, of your environment, and then most, one of the most important things is the communication and communication skills. So we're training people how to communicate and what the program looks like in the processes, and how to collect that data and use that data for future maintenance plan, maintenance outages. And then the last part of the whole program is in the training process is what we call continuous process improvements. So as you, as you venture and journey into this program, what can you continuously get better at doing? And as you continuously get better at doing, obviously, it saves time, resources and money, and most important, safety and reliability, two sides to the same coin, not individual paths, the same path, and it brings those two safety and reliability into the process and into the program.
That's excellent. Now, with any big change, there's always a few bumps in the road, of course. What sources of resistance can you meet when implementing odsr?
Yeah, you know, with odsr, it's really, in my opinion, again, I'll just say this is my opinion. It's a change of thinking. It's a change of guard. It's a change of management. And how they think about maintenance programs within their facilities. You know, is it? Is it the traditional maintenance procedures that they you know, that they do, the time based, the plan, preventive, the condition based maintenance. Again, those are all great programs, but it's done at a very high, sophisticated, intelligent level. The objective is, we want to keep those people involved. They're very important to the process, but the person that gets dismissed the most, and we said it already is, the operator, the person who knows the equipment the best. So that's that's the challenge, if you want to call it the challenge, or the resistance, is it's just a change of mindset, and it's a change of moving forward with something different, unique, as opposed to staying where you are. And let me tell you, if you're staying where you are, you're not progressing, so you're falling behind. So we want to help and train people, facilities and plant managers and engineers to think of a different way to do their safety their preventive maintenance programs.
How do electrical maintenance safety devices play into the odsr concept. How does, how does that work? Work in?
Yeah, great, great, great question. I think this is probably again, and this is just my opinion, one of the most important questions. You know, safety devices. There's a lot of safety equipment in our space today. We firmly believe safe at work, Safe at Home. It's important to to provide the tools, the processes, the training, to keep people safe at work. Again, we coin here at at Iris, safety and reliability, two sides of the same coin, one path, not individual paths. The safety protocols that you must comply with, with testing standards of various associations. An example the National Electrical Code, NIDA, IEEE nema. There are many, many associations, and they're there specifically to keep people safe at work, so they can go home and see their families at night. And that's the challenge that you know, that we have, is to keep those people safe performing a task and performing it safely, reliability in a rely. Manner, and, you know, keep keep facilities uptime running, because downtime costs cost money protecting the mechanical and electrical assets.
Thank you so much for giving us the skinny on odsr and giving us a broad overview of it. I'm sure we're going to talk about this topic in a lot more detail in future podcasts. So thank you very much for taking the time to speak to me today about it. Yeah,
great. Thank you. Always a pleasure. If you need anything, please feel free to reach out to Iris. It's a very important process program that we're working on. We'd love to share our ideas and thoughts with you all. Thanks, Lee. Thank you, and
thanks for tuning into the podcast. Until next time. I'm Lee Murray, take care. You.