Steven Hudson with Fluke Reliability
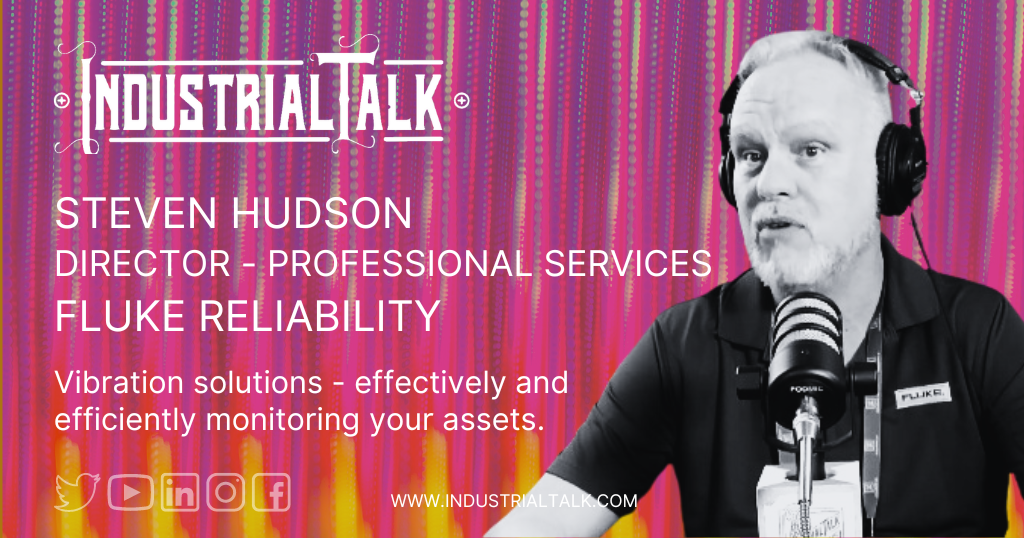
Industrial Talk is onsite at Xcelerate 24 and talking to Steven Hudson, Director of Professional Services with Fluke Reliability about “Vibration solutions to effectively and efficiently monitor your assets“.
Scott MacKenzie and Steven Hudson discussed the use of advanced vibration monitoring and analytics in industrial settings, while Stephen Hudson emphasized the importance of vibration analysis in asset management. They highlighted the benefits of wireless sensors, automated diagnostics, and real-time monitoring, with Hudson emphasizing the value of high-quality data and accurate analysis.
Action Items
- [ ] Contact Steven Hudson via LinkedIn or email at steven.hudson@fluke.com for more information about Fluke Reliability's vibration monitoring solutions.
- [ ] Attend Fluke Reliability's Accelerate conference in 2024 to learn more about their offerings.
- [ ] Consider partnering with Fluke Reliability to implement their wireless monitoring and automated diagnostic services. (Potential customers) [Throughout]
Outline
Vibration analysis and automation in industrial settings.
- Stephen Hudson, 35-year vibration analysis veteran, discusses asset management.
- Steven focuses on automated diagnostics with azimuth DLI wireless sensor.
Vibration monitoring technology for industrial machines, including device attachment, communication, and data analysis.
- Steven explains that the device is attached to the asset using adhesives and wire pass mesh network.
- Steven praises the ease of use and robustness of the devices, with one instance of a device reporting to the wrong gateway.
- Steven explains how Azima Connect works, including device-to-gateway-to-cloud connection and data analysis by a group of 30 analysts.
- Azima Connect sends faulty data to human analysts for final review and sends results back to customers in a timely manner.
Vibration analysis and predictive maintenance with Fluke Reliability.
- Wireless sensors simplify vibration analysis for new customers, while experienced analysts struggle with data overload.
- Steven advocates for preserving historical data to inform predictive maintenance decisions (12 words)
- Steven believes that relevant data is data that indicates machine condition at time of diagnostic (13 words)
- Steven Hudson of Fluke Reliability discusses vibration solutions for maintenance and asset management.
If interested in being on the Industrial Talk show, simply contact us and let's have a quick conversation.
Finally, get your exclusive free access to the Industrial Academy and a series on “Marketing Process Course” for Greater Success in 2024. All links designed for keeping you current in this rapidly changing Industrial Market. Learn! Grow! Enjoy!
STEVEN HUDSON'S CONTACT INFORMATION:
Personal LinkedIn: https://www.linkedin.com/in/steven-hudson/
Company LinkedIn: https://www.linkedin.com/company/fluke-reliability/
Company Website: https://reliability.fluke.com/
PODCAST VIDEO:
OTHER GREAT INDUSTRIAL RESOURCES:
NEOM: https://www.neom.com/en-us
Hexagon: https://hexagon.com/
Siemens: https://www.siemens.com/global/en.html
Palo Alto Networks: https://www.paloaltonetworks.com/ot-security-tco
Palo Alto Networks Report HERE.
Hitachi Digital Services: https://hitachids.com/
CAP Logistics: https://www.caplogistics.com/
Industrial Marketing Solutions: https://industrialtalk.com/industrial-marketing/
Industrial Academy: https://industrialtalk.com/industrial-academy/
Industrial Dojo: https://industrialtalk.com/industrial_dojo/
We the 15: https://www.wethe15.org/
YOUR INDUSTRIAL DIGITAL TOOLBOX:
LifterLMS: Get One Month Free for $1 – https://lifterlms.com/
Active Campaign: Active Campaign Link
Social Jukebox: https://www.socialjukebox.com/
Industrial Academy (One Month Free Access And One Free License For Future Industrial Leader):
Business Beatitude the Book
Do you desire a more joy-filled, deeply-enduring sense of accomplishment and success? Live your business the way you want to live with the BUSINESS BEATITUDES…The Bridge connecting sacrifice to success. YOU NEED THE BUSINESS BEATITUDES!
TAP INTO YOUR INDUSTRIAL SOUL, RESERVE YOUR COPY NOW! BE BOLD. BE BRAVE. DARE GREATLY AND CHANGE THE WORLD. GET THE BUSINESS BEATITUDES!
Reserve My Copy and My 25% Discount
Transcript
SUMMARY KEYWORDS
data, vibration, device, reliability, gateway, steven, customer, machines, cellular, great, industrial, sensors, analyst, attach, fluke, world, cloud, connect, diagnostic, actionable results
Scott, welcome to the Industrial Talk podcast with Scott. MacKenzie. Scott is a passionate industry professional dedicated to transferring cutting-edge industry focused innovations and trends while highlighting the men and women who keep the world moving. So put on your hard hat, grab your work boots and
ll a buzz out there. Xcelerate:hi everybody.
Yeah, welcome.
Thank you.
Did you have a good meeting? Yeah, it's
been quite a conference. Oh, that's
right, it's not a meeting. Meetings a little smaller than coffee. He's a little small. Yeah,
a ton of meetings.
That's exactly correct. So yeah, you're right. There's, there's meetings, and then, yeah, this is a conference. I'll go with that user conference. Excellent. Well, tell us a little bit about who Steven is first, and then let's get into that whole vibration conversation. Well,
that's great. I'm Steven Hudson. Had a background. Started off my career in submarines, US Navy, and then Submariner, yeah, then I transitioned into the reliability many, many years ago. I've been doing it about 35 years, so been doing a long time, primarily vibration analysis. Been involved in many of the other aspects of reliability maintenance as well. But today I really my primary focus is on vibration and automated, automated diagnostics. Yeah, probably the
big thing. There's a lot to be said there. All right, there's a lot to unwrap. All right, talk to us a little bit about that device, and then let's roll on into a Zima and all that good stuff, and see how all this works together.
Yeah, this is the azimuth DLI wireless sensor, Excel, 310, it's a triaxial accelerometer. It's it's got a very high sample rate, really great sensor my team uses it, relies on it. I'm going to say right up front, my entire vibration analysis team is, we're all data snobs. So the sensors really been killing the data snob we love it. So we like good data. And really the name of the game here is, is these little devices pump out a huge amount of data. So we really, our industry is evolving. We're learning that the customers are finding out that, you know, hey, just because they get a wireless sensor and they get lots of data doesn't mean they're going to get better results. So that's really where we come in. Is helping to automate that diagnostic piece. Because, again, this, this little guy is sending out data every hour, data every day. Typically, we've had a historical vibration analyst, you know, skilled analyst that's looking at the data, but that's 30 times more data than we got historically when we were doing it once a month, right? Oh, no, kidding. So, so we're really coming in and trying to and successfully adding the automation up front so that we focus our high value talent on where they need to be looking on those machines that are actually in fault, and then using their experience and their background to help the customer understand that problem, understand the risk, and hopefully get them to a work order, an action item, right? So that's really our goal, is to deliver actionable results for machines that are in fault and and send them non actionable results for
the rest the device itself. How do you place it on the asset? Is there a specific I would imagine each asset has a specific location for that device, and that comes with wisdom and knowledge and insights and all of that stuff. How do you and this is just me, just asking an off the cuff question. Here, attach that bad boy. Okay, how do you attach it?
s and hundreds. Of:So now it's attached to the asset. And we've been hearing a lot about the buzz around Zima, but let's, let's take it through the linear process. So now it's attached. It's cellular, or is it What? What? How do you communicate? How do you communicate the data, where talk to us about that. That's a,
again, another great question we use. This device uses wire pass. It's a it's a tree on kind of is who we partner with on that. But wire pass is a mesh network, and it's self healing. So essentially, there'd be this device, there would be a gateway, and either it has a line of sight or a direct connection to the Gateway, yeah, generally 100 feet, little more than 100 feet. Or if there's other sensors involved, and it can't get its signal back to the Gateway, it will connect to one of the other sensors that can so these things, this is what certainly, again, you know, I run a services organization, so we have to install them and use them. So we find them to be extremely robust. We find them to be very easy to set up. I'll even tell you we had one situation that we were on a plant and somebody had one in a car that was accidentally turned on, and it was reporting to the gateway at the plant that they were installing that day, and they couldn't figure out where it was coming from. So, yeah, we find them to be, to be very good. There are devices out there that are Bluetooth, those are the ones. But again, it's a, it's device to gateway or device to device to Gateway, and and Gateway then goes is connected to the cloud. That's
somebody was telling me about that technology, where you can go device, device to Gateway, or device, device device to Gateway. That's right. And so depending on where you can't just have a gateway everywhere, that is the way it's networked together, that's pretty doggone. Cool.
So then and then our gateway is connected. It can be either via internet connection, you know, a wired internet connection, a wireless internet connection, or via cellular. So in fact, a lot of our applications are cellular, because sometimes when we have this service and we're providing the diagnostics on this, we need it to go to a cloud. And so some plants don't want that then touching their internal network. So it's great to go through cellular, and we find that to be the easiest, basically, to get in line with an IT department and their requirements. So if we're just going device to device to Gateway to cellular, then it leaves the plant without ever touching anything.
So now we're in cellular. Now you're, you're, you're sending that data. Where are you sending the data? We're
sending the data to our our cloud, which, again, is our servers. It is a we use AWS servers. Once it hits those servers, it runs through again. This is high resolution vibration data, and it's high frequency, high resolution. It's not just simple overall values. It's it's time data, it's spectral data, right things that traditional vibration tools that they've always used to do their vibration analysis. So once it hits that cloud, it runs through our diagnostic system first, and that diagnostic system screens those and then the ones that are in fault get pushed to an actual human analyst for final review and sent back to the customer.
So here we have it. We have it up in where we need to be okay. So it's there, it's being analyzed. It's being taken care of. Where does Azima Connect? Where will that happen?
Azema connects to that cloud. I've got a group of 30 analysts around the world, and they connect into that same cloud. They see the incoming data. We have workflow tools that tell them exactly which machines each individual analyst has to look at. He goes, finds his test for his number of tests for that day, and he gets to review him, and as soon as he gets done reviewing that result in that same cloud, then gets sent a couple of ways to the customer.
How quickly does that happen? Compressing that time you don't want, you don't want it to be, you know, four weeks out, five weeks out, that's great. Is something that's going how quick? Yeah,
with our wireless SLA, we're doing the serious and extreme reviews to the customer within 24 hours. Yeah, non problem. Reviews go almost instantly. If it doesn't need a review, that's going to go straight to the customer. If it does need a review, it goes into a queue, and you turn that around within 24 hours,
and your technicians are what? Cat four, cat
three. So cat four is the highest I am a cat four, but I, most of my analysts are Cat Cat two and cat three. Most of them are cat three. Frankly, that's really what. It's
not easy to be a cat four.
It's not easy. But, you know, I really enjoy what I do.
Yeah, did you get. To look at all that squiggly line. So where do you see it going? Where do you see it heading right now, I think it's, it's more in line with trying to get the user community comfortable and and bringing it online and expanding the use of that solution and that service. Where do you see it going?
bration analysis for the last:you're able to take, take that steel mill analogy, and they've been collecting vibration data for whatever, many years. Yeah. Do you advocate taking historical data of the equipment that did exist to get an accurate or more clear picture of existing businesses.
If it's possible, it depends on the system. If it's possible, certainly we try and preserve at least a couple years, but we find that the older the data, the less valuable it is. We've had a large customer that did exactly that. We preserved two years of previous data on 15,000 machines, rather large customer we refer to that that historical data no more than a dozen times in the next year, right? So really, one thing I'll tell you about predictive maintenance and vibration analysis in particular, is it really is looking forward. And one of the things with these little devices like this is they're taking so much data, we can actually build a database in a week or two. With these sensors, they give us so much data so fast. So, you know, re baselining isn't as bad, isn't as big of a problem as it
was. Oh, I see that. That's that's important. But not. We have this, this device, and it's pulling data, and it's just hammering on the data. Is all the data that it's collecting? Will it be is it all relevant in the world of vibration, or some of it's just being collected? And maybe it'll be relevant in the future, near future,
I'll tell you what I think. I don't think it's all relevant. I do think that the data itself begins to age out and not become as relevant. What is relevant was that machine condition at the time. So once we do that diagnostic, and we know that the machine was not a problem, not a problem, and now it's a problem, and if we get that feedback as to what the customer was able to do to repair right? We made a recommendation. Was it the right recommendation? That is the relevant history that we really need for those machines, because that, that's what tells you where your bad actors are. That's what helps you feed back into your maintenance system and know where you need you know permanent improvements and things like that.
It's an exciting time. I think that that's a heck of a solution. Quite frankly, I really, I kudos to you and your team and this service that is being provided. I have always been wrestling with the fact that, how do you sustain a reliability, you know, passion within the organization, and this is just helping with being able to do it and being able to do it in an automated way. How do people get a hold of you there?
They get a hold of me on LinkedIn, Steven Hudson, or at, email me at steven.hudson@fluke.com
Very good. You were great.
Thank you guys.
So honored to have you a part of the show. This was a lot of fun. All right. Listeners, we're gonna have all the contact information for Steven out on Industrial Talk. So fear not. Reach out to him. You will not be disappointed. Exciting things taking place at Fluke Reliability. Check them out. Get on you just got to be a part of the the event next year, or just reach out sooner than later. It's all about education, collaboration and innovation. It's happening now. So thank you very much. Stay tuned. We will be right back.
You're listening to the Industrial Talk Podcast Network.
y is the company and Xcelerate: