Justin Sirotin with OCTO Product Development
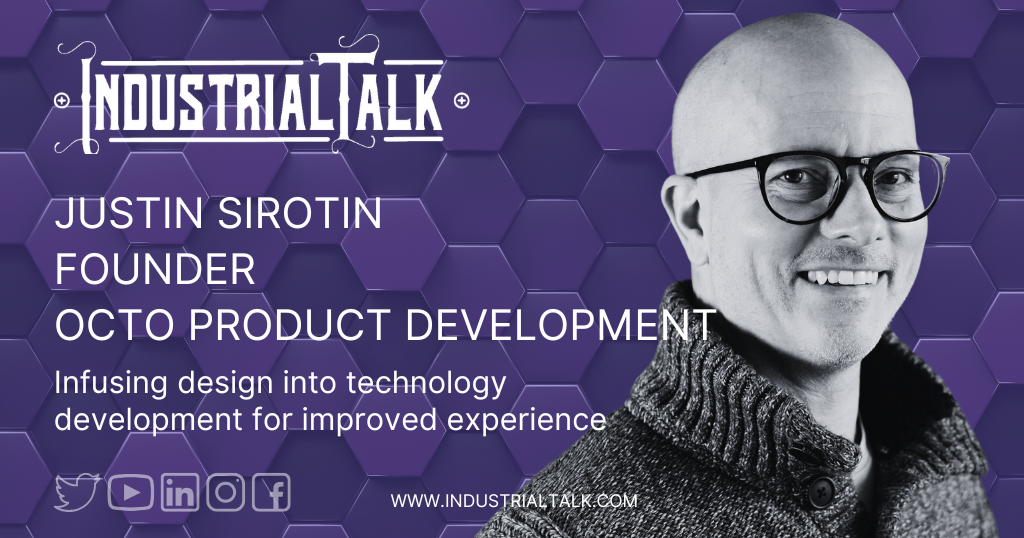
Scott MacKenzie interviews Justin Sirotin from OCTO, a company that designs complete customer experiences across various industries. OCTO, named after the octopus's adaptability, has been in operation for 15 years. Justin, with nearly 30 years in industrial design, emphasizes the importance of usability in technology. They discuss the challenges of integrating edge technology with utility grids to improve efficiency and user experience. Justin highlights the need for seamless, user-friendly designs to avoid user frustration. They also touch on the rapid prototyping and testing approach of companies like SpaceX and Formula One, which emphasize real-world testing and continuous improvement.
Action Items
- [ ] Reach out to Justin on LinkedIn or through the Octo website to discuss further.
Outline
Introduction and Purpose of Industrial Talk
- Scott MacKenzie introduces the Industrial Talk podcast, emphasizing its focus on industry professionals and their innovations.
- Scott highlights the platform's mission to amplify messages and support industry professionals worldwide.
- He expresses his admiration for industry professionals who solve problems and make the world a better place.
- Scott mentions the ease of getting involved with Industrial Talk for those interested in amplifying their message or technology.
Introduction of Justin and OCTO
- Scott introduces Justin and his company, OCTO, and explains the company's name and its origin.
- Justin shares the story behind the name OCTO, which was inspired by the adaptability of an octopus.
- Justin explains that the name OCTO is a shortened version of octopus, as the full name was unavailable.
- Scott and Justin engage in a light-hearted discussion about the name and its superhero-like connotations.
Justin's Background and OCTO's Services
- Justin provides a brief overview of his background in industrial design and his nearly 30 years of experience in the field.
- He explains that OCTO designs complete customer experiences, including pre-product, product, and post-product services.
- Justin mentions that he has started several companies and also teaches manufacturing techniques at the Rhode Island School of Design.
- He emphasizes the importance of embracing constraints and building market-validated creative solutions.
Challenges and Insights from Teaching Industrial Design
- Justin discusses the challenges of staying current in the industry and the impact of his students on his learning.
- He shares his experiences visiting factories in Vietnam and China to stay informed about production processes.
- Justin highlights the generational differences in attitudes towards consumption and the environment.
- He emphasizes the importance of efficiency and zero waste in the manufacturing sector.
The Role of Design in Technology and User Experience
- Scott and Justin discuss the importance of designing technology that is user-friendly and meets the needs of end-users.
- Justin explains that OCTO's role is to connect technology with user needs, ensuring seamless integration and usability.
- They discuss the evolution of the design field from being seen as just making things pretty to being integral to functionality.
- Justin shares an anecdote about a client who believed that complex software should be hard to use, illustrating the shift in thinking.
Designing for the Utility Grid and User Experience
- Scott and Justin delve into the complexities of designing for the utility grid and the challenges of integrating new technologies.
- Justin explains the role of OCTO in translating edge technology into software that utilities can consume.
- They discuss the importance of understanding the needs of both the utility operators and the edge technology providers.
- Justin shares the challenges of articulating the opportunity and building trust with clients.
The Future of Design and Automation in Manufacturing
- Justin predicts that the gap between the sophistication of consumer technology and industrial technology will continue to close.
- He emphasizes the importance of automation and business practice automation in improving efficiency and margins.
- Justin shares his observations from visiting factories in Vietnam, highlighting the focus on driving up margins through technology.
- They discuss the competitive pressures on domestic manufacturers to adopt efficient practices quickly.
SpaceX and the Impact of Rapid Prototyping and Testing
- Scott and Justin discuss the rapid prototyping and testing approach of SpaceX, drawing parallels with consumer technology.
- Justin highlights the importance of testing and learning in real-world conditions, as seen in Formula One racing.
- They discuss the benefits of this approach in driving down costs and improving efficiency.
- Justin shares his admiration for SpaceX's innovative approach and its impact on the space industry.
Conclusion and Contact Information
- Scott wraps up the conversation, emphasizing the importance of design in creating user-friendly and efficient solutions.
- Justin provides his contact information, including his LinkedIn profile and the OCTO website.
- Scott encourages listeners to reach out to Justin and OCTO for further discussions and collaboration.
- They express their enjoyment of the conversation and look forward to future interactions.
If interested in being on the Industrial Talk show, simply contact us and let's have a quick conversation.
Finally, get your exclusive free access to the Industrial Academy and a series on “Why You Need To Podcast” for Greater Success in 2023. All links designed for keeping you current in this rapidly changing Industrial Market. Learn! Grow! Enjoy!
JUSTIN SIROTIN'S CONTACT INFORMATION:
Personal LinkedIn: https://www.linkedin.com/in/justin-sirotin-983b233/
Company LinkedIn: https://www.linkedin.com/company/octo-product-development/
Company Website: https://www.octopd.com/
PODCAST VIDEO:
THE STRATEGIC REASON “WHY YOU NEED TO PODCAST”:
OTHER GREAT INDUSTRIAL RESOURCES:
NEOM: https://www.neom.com/en-us
Hexagon: https://hexagon.com/
Arduino: https://www.arduino.cc/
Fictiv: https://www.fictiv.com/
Hitachi Vantara: https://www.hitachivantara.com/en-us/home.html
Industrial Marketing Solutions: https://industrialtalk.com/industrial-marketing/
Industrial Academy: https://industrialtalk.com/industrial-academy/
Industrial Dojo: https://industrialtalk.com/industrial_dojo/
We the 15: https://www.wethe15.org/
YOUR INDUSTRIAL DIGITAL TOOLBOX:
LifterLMS: Get One Month Free for $1 – https://lifterlms.com/
Active Campaign: Active Campaign Link
Social Jukebox: https://www.socialjukebox.com/
Industrial Academy (One Month Free Access And One Free License For Future Industrial Leader):
Business Beatitude the Book
Do you desire a more joy-filled, deeply-enduring sense of accomplishment and success? Live your business the way you want to live with the BUSINESS BEATITUDES…The Bridge connecting sacrifice to success. YOU NEED THE BUSINESS BEATITUDES!
TAP INTO YOUR INDUSTRIAL SOUL, RESERVE YOUR COPY NOW! BE BOLD. BE BRAVE. DARE GREATLY AND CHANGE THE WORLD. GET THE BUSINESS BEATITUDES!
Reserve My Copy and My 25% Discount
Transcript
SUMMARY KEYWORDS
Industrial Talk, OCTO company, user experience, design insights, manufacturing efficiency, utility grid, technology integration, customer satisfaction, product usability, industrial design, market validation, automation impact, competitive advantage, consumer technology, rapid prototyping
Welcome to the Industrial Talk podcast with Scott. MacKenzie. Scott is a passionate industry professional dedicated to transferring cutting edge industry focused innovations and trends while highlighting the men and women who keep the world moving. So put on your hard hat, grab your work boots and let's
All right, welcome. Thank you very much for joining Industrial Talk. Thank you for your continued support of this platform, this number one industry related platform in the universe. We celebrate you industry professionals all around the world. You're bold, brave, you dare greatly, you innovate, you collaborate. You're solving problems each and every day. You're making the world a better place. That's why we celebrate you here on Industrial Talk. Take that to the bank for what it's worth. Coming from me, I'm such a fan, as you can tell. All right, this is a lengthy conversation, a very cool, handworthy conversation. Justin is his name, and the company is Oct or OCTO, which is cool. It's great name, all right, and I'm gonna hopefully say his last name correctly, Sirotin, Sirotin. All right, let's get cracking with the conversation. Yeah, okay, we're gonna go right into the interview, but before we do that, keep in mind, Industrial Talk is here for you. Here, right here. Industrial Talk. Go out to Industrial Talk.com. It's here for you, and it wants to amplify your message in whatever capacity you have a podcast, you say, Scott, I I want more amplification. And I'd say, well, just stick it out on Industrial Talk, I can help you through that process. And it's easy peasy. Or if you want to, you have a technology that you want to make sure people know about, and it really is a game changer, which they're all game changers. Innovation is fantastic out there right now, but you say it is a game changer, well, come talk to me, go out to Industrial Talk, and say, Yeah, I'm interested. I want game changing amplification. And then if you want to be on the podcast, just because you're cool and you're an industry, and you have something to say that will help people in their journey, along on their journey, all of that stuff. Well, you know, talk to me. Look at all roads industrial. Talk.com just have that conversation with me. If it doesn't work out, no big deal. But I guarantee you it's gonna work out because you have something to say, something to amplify, something to help individuals within the industrial market to be better, to solve challenges. That's what I believe. We talked to a number of companies, and all of them, they're just have such a tremendous passion for helping people succeed. That's my plug. Now, off the soap box. All right, he is in the hot seat. Justin is and OCTO is the company, and it's very cool. I'm just telling you, it's really a great conversation. Tremendous insight. Justin just brings, just backs up the truck and just lays out all of this great insights. Fun conversation. All right, here's Justin. Justin, welcome to Industrial Talk. How are you doing today?
I'm doing great. Thanks, Scott, thanks for having me. Oh,
come on, bring the energy, baby. One that's annoying. Thanks
for having me. I'm doing well. I'm doing very I'm doing actually, very, very well.
Yeah, I'm looking forward to this conversation, just because I'm a big fan of design listeners. We're going to be talking about that, and we're going to be talking about how you can make the experience much more better, if I could use that. That's what we're talking about. This is what the company OCTO. Does that stand for anything?
No, it's just OCTO. That's it. It's got a funny backstory, which, so OCTO, we've been around for about 15 years, and when we were crafting the name, naming companies is a nightmare,
Yes, amen,
nightmare. And we were naming the company and trying to decide, did we want the name to mean anything, or did we want the name to just be generic? And we kind of came to the conclusion that having the name mean something would be fun. And I found this video on YouTube of an OCTOpus that got caught by a fisherman, pulled onto the boat, changed from. Brown to white immediately, because the boat was white, and then started to walk on its legs, across the boat, climbed up the other side of the boat, jumped in the water. As soon as it hits the water, changes color and becomes something else. And we thought like, Okay, well, that's us. We transform ourselves into whatever form we need to be in order to satisfy the needs of our of our client base, of our customers. And we behave like an OCTOpus. We're curious. We change shape, we change color. And we couldn't get the name OCTOpus, so we just said we took what we could get. We got OCTO. So that's
that's cool. A lot it because it's in capital letters. I thought it was OCTO. Now,
an acronym stands for nothing. It's just the first part of the word OCTOpus, and that's all we could get. You know, it
sounds like a superhero.
We are superheroes. Obviously, you
go, that's right. Own it superhero. So let's, let's just dive into who you are there, Justin real quick. And we've already got the OCTO background, yeah, give us a little background on who you are,
en't paid for a haircut since: saving:I'm on my third set of industrial clippers now. Yeah, but, uh, so the the, you know, I started as an industrial designer, and then very quickly, kind of moved into this space where we where we, instead of doing traditional industrial design, which is really more about more about form, more about ergonomics and usability, back when I first got off the ground, we have, we have sort of graduated into a space where we design much more than point solutions, where we're responsible for designing an entire customer experience from where they find a particular solution that they're looking for, how that solution is experienced before they've purchased it, then the product that they buy, then the service that gets delivered thereafter. So we kind of live across the entire spectrum of of our customers, businesses delivering, delivering both the pre product experience, the product experience, and then the and then the post product service experience that lives, that lives behind it. And so I started this company 15 years ago, worked in another, mostly med tech space before that, industrial goods, med tech, and then, and then started this about 15 years ago. I've actually started a number of companies. The agency that I, that I run, kind of lives at the core, and we've spun off a couple of other companies alongside it. And then I'm also, I teach the manufacturing techniques class at Rhode Island School of Design. So I get all of the third year industrial design students, and I, I tell my students on the first day of class that my class is the red pill. So if you've seen The Matrix, yeah, my class is the reality check, because design school is all about removing barriers, opening up your your your your creative mind. And I tell them, when you get out of school, the constraints are your friend, and they are required, and you don't get to avoid constraints, and so we've built a practice here that really embraces constraints and embraces the reality of guardrails as a benefit, not a hindrance, to building, you know, Market validated creative solutions
as a teacher, do you? Do you just constantly stay current? Do the do the students challenge you?
They do. And I have to, I have to work really hard to stay as many steps ahead of them as I can, from a, you know, from an industry standpoint, so I'm always out. I was in Vietnam last week, at factories. I was in China and in in January, I go to factories locally. Here, here, domestic factories, local factories. I'm kind of always in and out of the of the production world, both for my own learnings and for. For our clients, so it's they, they, where they really challenge me is on the social side interesting, where it's really like their whole mindset of what work is, what manufacturing should be, what what consumption looks like, is so different than you know what I would have come up through 30 years ago, when I was in college. You
think that that, are they hitting the mark? Is it? Is it going to I mean, I'm always interested in that school of thought, of trying to really challenge the norm, especially today, where we I think industry and manufacturing as a whole has changed so drastically, so and so rapidly, is it going to be just something completely different going forward? And I mean,
I so my opinion on this is migrated over the years. I think young people are both optimistic and conflicted about what this means like I sort of challenge them on the idea of, go look in your closet, pick out the number of clothes that you haven't worn in six months and tell me why you own them. Then think about what's going to happen to those clothes in six months time when you give them away, or you throw them away. And now think about the multiplication problem of all of the versions of you that live in the world. And now think about how many clothes are being produced globally that are going to just go from the store to the closet, from the closet to the landfill and never get worn. Wow. And that's a that's a that's an eye opening conversation to have with a 21 year old who hasn't really thought about the fact that, yeah, I'm buying too much crap and and at the same time, I really tried to expose them to the fact that the manufacturing sector is inherently built around efficiency and a lack of waste. It's the whole premise of manufacturing is zero waste, remove all. And not just waste from a material standpoint, but waste from an energy standpoint, waste from a human resources standpoint, like drive it as close to zero as possible. So when you're thinking about, you know where to where to find efficiencies the manufacturing sector is built on that. It's all they're trying to do is drive it to zero. And you have to find those efficiencies in other places, because you're not going to find them as easily in the production world as you will in lots of other parts of society.
It's also performance, right? You have efficiency. You're driving it down, but you're also improving the performance. And, and I'm, I am able to produce this one gar one more garment a day. Yep, and, and, yep,
so increasing productivity and driving down, yeah, you know, waste is what the manufacturing sector is built around, and the rest of the world isn't really built that way, in part because we're not incentivized to be like that, whereas the manufacturing sector is uniquely incentivized to be hyper efficient, hyper productive, whereas the rest of the world, I mean, even in my agency like we don't, we don't measure productivity in that way. We don't, we don't think about our job that way. But you walk into a production facility and they're trying to say, How can I drive 10% more in the same square footage with the same headcount? And how can I drive down my, you know, my scrap rate, and drive down my, my, whatever, all of my various metrics that I'm taking, taking on. Here's
a side note specific to your analogy there driving efficiency. So I was managing an ethanol facility up in Idaho, and it was a waste to energy type of technology, and we would be taking potato waste and then producing ethanol from it. And the it sounded fine. It was great. Everything was fine until the supplier became more efficient at cutting potatoes. Yeah, less less waste. And it it. And don't ask me how they did it, but they did it. And lo and behold, they're getting more out of that potato, and we are getting less, you know, waste, which is good, but then again, it business model, it just is, what it is. I got rid of waste.
It is, it is, and it's a so. So when I'm dealing with my students, you know that's a big part of what we talk about is the inherent lack of waste in the manufacturing sector as compared to other industries, because of the incentives that. Are built to be efficient. They make more money if they drive up throughput and drive down waste period the end so. And then we kind of use that across the entire spectrum of of how we talk about, you know, goods and services, which is, which is, aligning those with with incentives. And if the incentives are there, people behave differently. If the incentives aren't there, they don't like there's no incentive for you to not fill your closet with more clothes than you can wear. Interesting and so as a result, you will fill your closet with more clothes than you can wear, because you can go on the internet and you can buy them for cheap and you can feel good about that purchase at the time, but we don't have a system in place to build good incentives for people to behave differently. You
know what that system is? Age? I don't want to deal with it. Deal
with all this crap.
I'm cleaning out it.
I have a:yeah, it just happens. Sorry about digressing. That was that was fascinating. Well, we're going to be talking about is specifically about the utility grid and and how we can and what was, what jumped out in your conversation is that, and people can relate to this. There's a technology. The technology is designed by technology people and and it might be great in the way it's designed, but from a user perspective, the individuals that have to use that platform, it might be sub sub optimal, sub liked, and which then you get that, that issue of where I'm not using the product the way it needs to be used, because it's so unfriendly, it's so illogical in some cases. And not to say that it's not meeting the needs, but you're, you're the you're the guy that takes that and tries to bring it together. So where me end user, or whatever, I use that product, right? Yep,
yep, yeah, that's our that's our fundamental role to connect the user to a technology and say that we have a technology base that lives here. We have a user group that's here. They have a set of needs that they have in order to achieve their goals and their job, and we need to make sure those two things are seamlessly connected together, that they don't end up with extraneous steps that they have to take in order, in order to achieve their goals, which means you have to know their goals, yeah, and understand and Not not know their goals in a way that's superfluous. But really know, know why they need what you're providing to them, and know why your solution is uniquely qualified to deliver on their need. And once you know those things, you can start to build a product that then satisfies both sides of that equation.
It would, it would seem to me that I would like to have you involved at the beginning of these, these events, these, these design efforts, as opposed to after the fact, and then try to figure out how to sort of decouple and make it a user, a better user experience, it would probably, but that's that's
true, it does happen. Uh, it happens. I will say it actually has been happening more and more. I think, you know, 15 years ago, the the design field was almost thought of as lipstick.
Oh, interesting,
right? Like we made the thing. We're the engineers. We know how this works. You guys just come in and just make it pretty please. That was sort of the relationship. Over time, that relationship has matured to now being able to have the understanding for usability as a part of functionality and design delivering usability. So if you're delivering a solution that doesn't have good usability by default, less people will use it, yeah. And so as a result, you can tie directly, uh, revenue, customer attention, customer satisfaction, to a well designed product, yeah, yeah. And I think that the. The really interesting thing for my firm is that we're in a little bit of a weird space for designers. 95% of the companies we work with are purely technical organizations, yeah. And so we come in and we're like, we're the weirdos in the room, and it takes a little there's a there's a trust that has to get built over time for our customers to really understand that our our job here is to make the thing that the technology that you've created, better, not prettier, better, and we're making it better, because now your customer can flow through that technology in a way that delivers on the promise that they need it to deliver on not what you want it to do, but what they need it to do. And that time that that the way that we build, that bridge takes takes time. It takes some trust, because people are very protective of the thing that they make. And it takes a little time to sort of say, hey, look like it's not about whether what you've built is good or it's bad. It's about whether it delivers on the on the needs for the person who you're trying to deliver it for and as
a as a user, I don't like to click right? I want my business to be it's we're just that spoiled. And I would imagine the the pressures of what is taking place in the marketplace, just from apps and people are are designing and delivering apps that are smart and and high level of usability to it and and it just has trained me. I I've used absent and I, why do I have to do that? Yeah, that takes a lot
of I had, I had a client, this was years ago. Say to us in a meeting with a straight face, it's complicated software for smart people. It's supposed to be hard to use. Yeah. I was like, What?
No, no, I think
at the time, I picked up my phone, and this was, again, it was a long time ago, and I said, you know how you know how much complexity is in this device, and it's all shielded from you, you know. And they're not putting that complexity in front of you. They're taking that complexity away, and they're letting the technology do its job, and they're letting you use it in a really seamless way, but they're not forcing you to know how to make that technology do what it's supposed to do. And that's, that's the delivery of a good product. That's,
that's, I agree with you 100% Absolutely, 100% speaking of complexity, take us through one of the areas that has me just sort of dazzled. And I, I it's way above my pay grade. No, no doubt about it, I have a utility background. I love the utility industry. Being a former lineman, climbing and doing all that stuff, I really have a passion for it. But given the pressures that of today on the utility, just the just utilities in general, to be able to to adapt to all of the changes taking place and all the demands, how do we, how do we take something as complex as the grid and make it in such a way that delivers on what you you as a designer? I mean, it's got to be it's, I don't know. I don't even know how to even frame the question, how do you do that?
So, so let me just frame the problem that we were asked to try to solve, and that might help, yeah, answer that bigger question. So our clients, a company, called you till it outta they have been around for quite a long time. They are fundamentally a pattern recognition company. Fundamentally what they've done is they built a really clever technology that allows them to recognize patterns on the grid at certain levels and in certain locations for them to be able to understand what's happening at the edge of the entire system. So the grid itself is actually relatively dumb all the way at the edge. It's pretty smart in the middle. It's most smart at the beginning. So you have a power plant at one end delivering power into a community. We kind of know what's happening there. We know what's happening as it travels out through the substations, and then as it leaves the substations, and it travels all the way through those transmission lines to your home, we lose touch with what's actually happening at the edge of the grid. So this company works the opposite direction. They put technology at the edge. The grid that helps deliver information to effectively home base by listening, for lack of a better term, to what the power is telling them is happening all the way at the edge. So a specific example would be, if you have a neighborhood and you see a certain curve in the way that power is being drawn or not drawn. You can know if somebody's got an electric car on their house, a photovoltaic on their house, a large consuming appliance in their house that comes on on a regular basis, and you can help inform what kind of electricity needs to be delivered, and when, not what kinds, but what, when you need to deliver electricity and when you don't need to deliver deliver electricity at much higher fidelity, because you have this edge understanding of this of the space or of the community. So our responsibility was to effectively translate that technology into a software that then the the utility can consume the information into their end, because it's two completely different Think of it like two different languages. One's an one's a language of pushing power out. The other is a language of taking data in and they they didn't have a way to connect those two ideas. So our responsibility was to understand what the what the utility operators needed, connect that to, what the edge technology can deliver, and then embody it in a software that that gave the utility visibility in a place where they were otherwise blind. That's fundamentally what we had to do, see,
I couldn't put that into a question. Yeah, I got it now I know. Thank you. I will tell you I was in another country. It
took, it took my team six months just to be able to articulate the opportunity to ourselves like it. It's a if you when you get into the nuts and bolts of how all of this stuff works, it's so complicated, and the utility team is so sophisticated with what they've built, that it takes you're you're peeling this onion over and over and over until you get down to the point where it's Like, okay, but I understand what you're doing, but I don't understand why you're doing it. And we keep we had to just sort of open this thing up over a long period of time, lots of conversations with utilities, lots of conversations with with the internal teams, with the external stakeholders, with advisors, and then you kind of, and then all of a sudden, you kind of have this picture that emerges, and once that picture starts to emerge, you're able to embody that picture into an actual product or or tool that people can use. But if you don't, if you don't have that, you just keep making technology that it's looking for a problem to solve, yeah, instead of identifying a problem and applying a technology to solve it, and that was the that was the big shift in thinking that, that the whole group, us, them, everybody, had to find was, well, what are We really solving? And then what's the, what's the linchpin for getting our technology to deliver that, that level of resolution, so that you can solve the problem? And it's still evolving, like the thing we built four years ago is is no longer the product that's being produced today, like it's all changing all the time. Yeah. So it's this sort of constant process of testing, listening, learning, adjusting and looping that overnight, I like
the point that you bring out where you're having some intelligence at the edge. That's one thing. One of the stumbling blocks that I always had to deal with is my old school thinking of utilities, where I would have power generation, transmission, transmission substations gone into, you know, distribution, distribution substations, and on into the consumer itself, whatever that might be, very linear, very one directional, right nowadays, because you have distributive energy, and you're on the The, you know, the distributive side of that meter I could never reconcile of how me as a system operator, would be able to say, hey, check that out. Down to the minute detail challenges, they have a car that is Tesla, and it's pushing back. Power the other way, or it's consuming power, or whatever it might be, but it's dynamic, and me, as a system operator, how do I even see that? But it can be a it could be difficult and and impact the grid in a negative way, if I don't get that right?
Yeah. I mean, you're, you're in a, you're in an unusual and unique position to have this conversation, because you, because of the because of your experience. Most people, most people think of the grid like they think of the wires in their house. And that's not what the grid is. The grid's like an animal. It's like a living, breathing thing, and it gets bigger and it gets smaller, it gets hotter, it gets colder. It has all of this dynamic movement to the grid. And if you don't know what's happening at the end, at the edge, you can't then drive it to any sort of level of efficiency. I mean, our grid is our grid's really old. It's really, really old. It is not built for two way power. It's not made for us to bring in power from a house. It's made for us to just pump energy out. It is also not made for power to go in waves, daytime, nighttime, windy day, cloud, you know, calm day. It's not made for it's not made for ders distributed energy. It's not made for any of this. It's made to have a hub and spoke model. A big chunk of energy getting made over here, driving power out, and we overcharge the grid like crazy, because we have all these losses from beginning to end. And so there's a whole mind shift happening inside the energy sector that is okay, well, well, how do we manage this new version of electric distribution?
And there's such inefficiencies that exist. There's just tremendous gains that can happen as a result of doing it right. But the Achilles heel, from my perspective, is that consumer, and if my power, if I come home and I flip the switch and that thing sort of flickers a little bit, or that clock starts blinking at me, I'm upset. You have to be very precise in how they deploy a smart grid solution 100%
and, you know, I tell my students the same thing, and I say it to clients. People buy things. Whether you're a B to B technology service provider or you're direct to consumer. Doesn't matter. People buy things under the assumption of the big picture working well, that's why they buy things, right? Like this car is going to drive me from point A to point B, and it's going to do that at some level of power or some level of efficiency or some level of luxury, whatever that is, the reason people walk away from solutions is because of stupid little things. That's why we walk away, right? You make a thing, it's works amazingly well when you get it and then you start to use it a little like I have a Volkswagen ID for that. There have been days I want to just drive it back to the dealership and park it, and it's not over anything big. It's over like, why did you hide the icon for the heated steering wheel that I don't want to have on, and now I can't find how to turn it off.
And I'm, I'm, I don't like it. It's
driving me crazy. Now, the reality is, the car drives great. It's super efficient. It looks good enough. It's very like all the things they said it was going to be, it is, but those little details are what get people really, really annoyed if you get them wrong. And, yeah, that that's, that's, that's the, that's the power that a good design has over a bad design. You mask all those little weird idiosyncrasies, and people just use the stuff. And if you, if you expose those idiosyncrasies, people walk away. But
here's the funny thing, it like I take for granted my power. It just goes on. I don't even think about it, right, right? The only time I think about it is when it's a pain, or when I lose it, or whatever happening out there, and I'm thinking to myself, What the heck's going on? And the reality is, is that, if you're doing your job right, nobody notices.
Nobody notices. It's the hardest thing about the field that we're in. We do our job perfectly. Nobody even knows we're there. They don't think about it. They just, Oh, get the thing. They use the thing, they put the thing down, and they're happy. And if we do our job poorly, they know exactly. Exactly who to blame. It's like, who designed this?
Yeah, and as we talk about the utility challenge, I guarantee you all of this high tech equipment, all of this very sensitive stuff, we don't deliver on it. We don't deliver, you know, reliable power delivered at 60 cycles per second. You know, no variation in the voltage. It's all clean, yep. Then then a lot of this other stuff that we just take for granted, all of the technology that sits in front of us, it doesn't like that doesn't
like it at all. Yeah, not at all, yeah. And I think, you know, if you extrapolate that same idea outside of the grid, and you put that into any other, yes, any other industrial I think, I think the industrial sector, really, the industrial sector is really waking up to this idea, yeah, very quickly. Because, you know, the line operator in a manufacturing set or a facility who has to run a big piece of hardware. They also have a phone in their pocket, and they also drive a car that's well designed, and they also have a house whose grid works the way they expect it to. And so there is an expectation for functionality that exists outside of sort of the traditional consumer brands or or consumer electronics world that's now showing up. You know, if you're going to go build a connected worker system, well, your expectation is that that's going to work as well as Spotify, like I shouldn't have a connected worker solution in the manufacturing sector that causes me challenges for how I set up a user, or how I set up a particular workflow, or how I set up an alert, like I should be able to do that, Like I do it on my phone and and that reality is, is very much coming to light inside the industrial sectors, and that's the place that we we bring our expertise.
You're right, and I agree. I see it happening within manufacturing, where what used to take for a CNC machine very challenging, you know, programming of a particular part to now they're getting it, and they're driving to even simpler ways to deliver more complex parts exactly, and being able to do it efficiently. And for me, as a operator, I don't have to. I I'm enjoying the experience, which is good and then, but yeah, yeah. I
mean, people who are frustrated with the technology that they use, they're less efficient. They're not going to make good decisions. They're going to you're distracting them from the thing you really need them to do, which is their, their, their actual job. And so, you know, as I said, I think the, I think the market is waking up to the idea that well designed products in that space make you more efficient, which means you make more money. Yeah, period.
The end. No brainer. I Where do you see it going? I mean, if you're, if you're just sort of put your future hat on, I Where do you see it going? What do you
I think there's, I mean, we are with the bar is pretty low still in most of these sectors. I think you know, if you, if you just, if you just compare the level of usability and sophistication in your in your in your pocket, to your workplace. If you work in an industrial sector, you know that that that gap still very, very large. I think we're going to continue to see that gap close. I think we're going to see automation. And I don't mean automate. I mean I mean business practice automation, work, workplace, automation, start to really impact in a more meaningful way. I think up until now, it's been a bit, I don't want to call it frivolous, but it's not. It hasn't had the the bottom-line impact that I think a lot of people were looking for when you started to convert from an analog to a digital practice within especially in the manufacturing sector. And I think that we're finally at the point where we, we, we from a technology standpoint, understand where you can apply these to improve business practices, rather than just always thinking about them from a from a process standpoint, and merging those two things together is going to give people, you know, those who can figure it out are going to have, are going to have pretty big competitive advantages over those who don't. And I was just in three facilities in Vietnam last, last week. I. The level of sophistication of these three facilities was extremely impressive, and everything they were doing was was in an effort to drive up their margin. You could see it throughout everything you walk through is about them driving up their margin, which means, in theory, they can deliver a higher quality product with less waste, with less rejects, with with probably at lower prices. But if you think about their incentives, this is, you know, coming back to where we started, their incentive is, I need to drive up my margin. So if I'm going to drive up my margin, I'm going to figure out ways to apply this technology with that as my focus. How do I drive up my margin? And then the results are, I get benefits for everybody else, yeah, benefits for my workforce. I get benefits for my customers. I get benefits for for my for my future resilience of my organization. And so I think that's, that's, you know, we're going to continue to see things move, you know, move in that direction, where, where these technologies really get applied to help raise margins of manufacturers, raise margins of of organizations. And that then, that then drives all sorts of other benefits. Yeah, I
think it's undeniable. I think that it's a great time. I think it's a renaissance. I think people are beginning to embrace that, and I can appreciate that, and everybody benefits as a result of that, yeah, just it's an exciting time, yeah, yeah.
And for domestic manufacturers, you know, the pressure that domestic manufacturers are under requires that to be done at at probably larger scales and at faster speeds. That has to happen more quickly because you don't have the benefit of low cost labor and and and low cost power, low cost, real estate, low cost, all the rest of it. And so domestic manufacturers are really being pushed to to crack that code as quickly as possible to stay competitive.
Just look at SpaceX. They just drive to be able to turn around a rocket as fast as they possibly can. And everything is associated with that. And they recognize the necessity to drive down costs as much as possible, so that that interplanetary, you know, yeah, travel exists, and they have to do that or it will never, it will never,
shuttle launch in Florida in:It It was wild. It was wild. And they're shooting it off today.
Are they really? I
don't know. That happens a starship. It's going off in the afternoon, later in the afternoon, so that they can see it land. The the starship land in daylight. That's amazing. And then they have, you know, what they're trying to test. They're trying to test some of their their tiles. So they're coming in at a steeper, steeper decline, coming in to push the the levels of those tiles and see how they they're just trying to break it in such a way that they can come up with the data, and they're pulling data, data, data, data, data, data, the whole time and then come in faster to catch it with the chopsticks that that the heavy,
yeah, it's wild. I mean, and I mean, they're, they're in this, in this real way. You. They have taken what was once a sort of black box of development, and they're really applying a lot of consumer technology ideas to it, like this idea that you're gonna rapidly prototype and test ideas and allow things to break and allow things to not work correctly in a obviously, in a safe way, yeah, that that comes out of the, that's the consumer products world, that's the consumer electronics world, that's the consumer software world, right? Like, that's, that's this idea of, like, release a piece of software and then update, update, update, update. They're taking that mindset and in a, in a, in a pretty clever way, applying it to an area where nobody did that before. NASA didn't do that. NASA made they spent 20 years thinking, and then they put something into space, and they hoped it didn't blow up. And you know now you're, you're testing and trying and testing and trying, and there's and they think of the amount of computer simulation opportunities that they have, and they're still gonna just fly it, just gonna fly it, make sure it works. Yeah, and it's pretty it's pretty amazing. I mean, I follow Formula One really, really closely. I really like Formula One. And I think Formula One is this incredible laboratory. It's like a living laboratory of this con, this conflict between theory and practicality. Yes, because you go through all of this simulation work, you do all this work in a wind tunnel, but you don't know until the driver sits in the car and it goes around a track and the bumps are there and the wind is there. Another car is there, and a trailing car is there. And then you really learn, what do we got? Did we do it well, or did we not do it well? And, you know, I believe, I think that idea, that mindset, from a product standpoint, is really valuable, because if you spend all your time thinking, and you aren't out trying and testing and learning, you can you can convince yourself that anything is great. And then you get out there and you put it in front of a user, or in their case, put a driver in the driver's seat, and let them tell you what's working and what's not working, and all of a sudden you hear the radio chatter. This car is bouncing to the point where I can't see, yeah, what is happening, right? And the engineers are all scratching their heads saying, like, well, in the wind tunnel and the simulations, we didn't see any bouncing. And yet, if all they had done is look back 40 years, you'd have seen that the old ground effects cars from 40 years ago, they all bounced. And, yeah, that's like, it's a real problem to solve. And it doesn't, it doesn't, it doesn't Embody itself, until you get it out in front of out from inside, the thinking, out of your brain and into the world. And then once it's in the world, you learn all the things you didn't know. And
nd they're dialing it in to a:Oh god. Guy
comes in two seconds later. I said, What the heck? What was that? Yeah,
God. I think the records like 1.85 seconds to change four tires on a car. Yeah, I mean, you got like 30 guys, but still, it's really fast. It's real fast. Yeah, and you think about like, how much work went into just designing the wheel nut, that is. That's so true, how much work went in design that wheel nut. And you know, if they make two stops, and you pick up a second for each stop, then you gain two seconds over the course of a race like, that's meaningful. And, yeah, that wheel nut and the and the gun, I mean, there was, I forget, which team was struggling with their with their pit stops, and they sort of dialed it down to, like, the wheel nut, and the gun needed a redesign in order to be able to do this faster. And it's amazing, yeah, it's totally, you know, and, and those, this is, this is gets back to those, like, it's the little details, those little things that you do that, yeah, 401, is a really interesting, like, I said, it's like a, it's like a giant laboratory. And all it is for figuring out how to develop things faster, how to how to you. Execute ideas that are extremely complicated in the real world faster and more accurately. It's it's quite a it's quite a spectacle. It really
is. You as a designer can definitely appreciate it. And I'm he has just a casual I still geek out on it. By the way, Vegas is this week. It
is this week. Yeah, we'll see. It's gonna be 47 degrees on race night.
Is it really 47 I can't wait. See there it is. Car that responds in that type of weather, 47
the driver's hands are gonna be really cold. That's cold. I think it's, I think it's a little colder than last year, and they were worried last year,
yeah, at 200 miles per hour. Yeah, that's that's cool.
Nuts. Totally lost. Hopefully they welded up all the sewers down correctly this time.
You believe that that okay? Yeah, I must have
been million dollar Yeah, and he got Yeah, million bucks because he sucked a sewer cap off the road and destroy the bottom of the car. Think of the force. Both things are heavy. Car rode over and just suck. Yeah,
so we got to wrap this up
all day. This is good. What should we talk about next?
Yeah, big time. How do people get a hold of you there? Justin, let's
say Easiest way is LinkedIn. My company website is OCTO pd.com, so O, C, T, O, P like Paul, D, like david.com or Justin saroton on LinkedIn. Those are probably the two easiest ways to to get in touch. There you go. Well,
we're going to have all the contact information for you out on Industrial Talk. You are fantastic. Great. Thank
you, Scott, thanks for having me. This was fun. I really enjoyed.
Might not have covered what I covered everything I wanted to hear about. Good, yeah,
following your lead. So yeah, there you go. You need
to reach out to Justin. That's a must. That's that's a to do. We're gonna wrap it up on the other side. Stay tuned. We will be right back.
You're listening to the Industrial Talk Podcast Network.
How about that? That was fun. Those are great gumbo. Yeah, you need to, you need to reach out to just to put that on your to do list. Easy LinkedIn, right there. He's got some great insights. His team at OCTO delivering some really great solutions. They look at things through a designer's eye like that, like the whole thing, paper, pencil. If you haven't gotten through the whole thing, you need to come back. Listen to it again. Fast forward, slow down. You know, whatever it takes to get that content into your noggin. Good stuff. All right. Again, I'm going to reiterate Industrial Talk is here for you. You got a podcast, you've got technology. You want to be on the podcast. You go out to Industrial Talk. Easy, reach out to me. You'll have a conversation with me. I'm not a bad person. I'm easy to talk to. All right. Be bold, be brave, dare greatly, we're going to have some more great conversations coming to you at Industrial Talk. So stay tuned.