Preston Johnson with Cutsforth
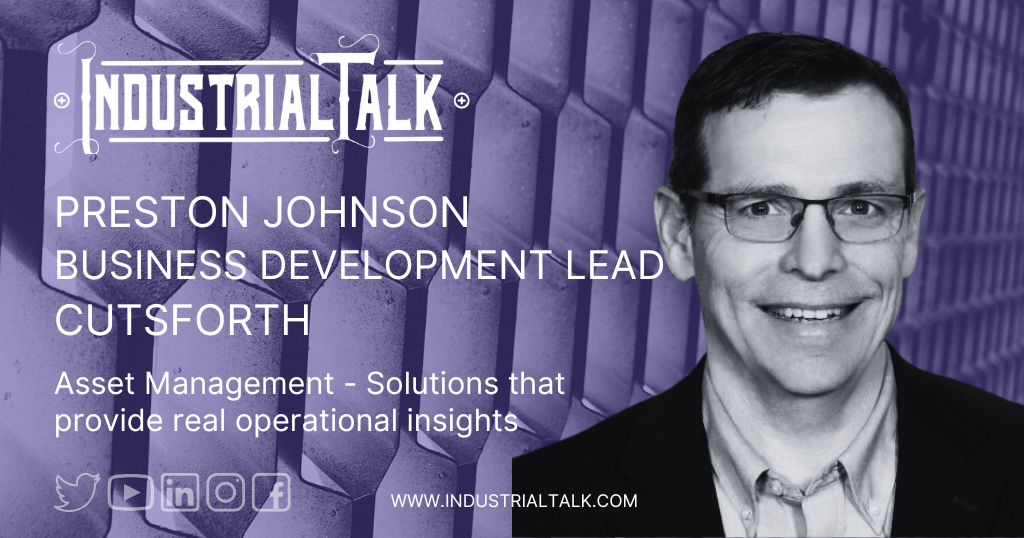
Scott MacKenzie hosts the Industrial Talk podcast, celebrating its success and encouraging listeners to share their stories and technology. He introduces Preston Johnson from Cutsforth, who discusses their asset management platform, Insight CM. Insight CM integrates various condition monitoring technologies, such as vibration, lubrication, and thermography, to provide a comprehensive view of equipment health. Preston emphasizes the importance of understanding asset failure modes and leveraging data to predict and plan maintenance. He highlights the benefits of workforce optimization, increased uptime, and reduced maintenance costs. Roadblocks include resource constraints, IT integration, and leadership buy-in. Preston provides contact information for further inquiries.
Action Items
- [ ] Understand the client's critical assets and failure modes.
- [ ] Identify the appropriate sensors to detect developing defects.
- [ ] Integrate the Insight CM platform with the client's existing data sources and systems.
- [ ] Develop prognostic capabilities to predict remaining useful life of equipment.
- [ ] Provide a business case and justification for implementing the Insight CM solution.
Outline
Introduction and Overview of Industrial Talk Podcast
- Scott MacKenzie introduces the Industrial Talk podcast, emphasizing its focus on industry innovations and trends.
- Scott thanks listeners for their support, highlighting the podcast's success and its mission to celebrate leaders in the industrial sector.
- Scott discusses the exciting developments expected in 2025, including innovation, technology, and solutions in various industries.
- The podcast aims to promote companies passionate about success and to provide a platform for sharing insights and solutions.
Introduction of Preston Johnson and Cutsforth
- Scott introduces Preston Johnson from Cutsforth, focusing on asset management and the importance of managing assets effectively.
- Scott reflects on the success of the previous year, mentioning the numerous interviews with industry leaders and the global broadcasts.
- Scott encourages listeners to create and share their stories, emphasizing the importance of amplifying messages through the Industrial Talk platform.
- The podcast aims to support listeners in their success by providing a platform for sharing technology and solutions.
Preston Johnson's Background and Cutsforth's History
- Preston Johnson shares his extensive experience in the industrial instrumentation business, including his time at National Instruments.
- Preston discusses his journey in condition monitoring and predictive maintenance, starting in the early 2000s.
- Cutsforth's acquisition of the Insight CM software in 2022 is highlighted, expanding their business from generator support to a predictive maintenance platform.
- Preston provides a brief history of Cutsforth and their involvement in various industries, including power generation and generator support.
Insight CM Software and Its Unique Features
- Preston explains the vision behind Insight CM, focusing on leveraging multiple condition monitoring technologies.
- The software was developed in response to a large power generation company's need for fleet-wide condition monitoring across various technologies.
- Insight CM's ability to digitize and compare trends from different technologies, such as vibration, lubrication, and temperature, is emphasized.
- The software aims to identify defects in equipment by collaborating and comparing data from different monitoring technologies.
Implementation of Insight CM and Typical Steps
- Preston outlines the typical implementation steps for Insight CM, starting with understanding the assets in the plant.
- The importance of identifying failure modes and selecting appropriate sensors to detect defects is discussed.
- Preston explains the process of understanding the performance and defects in equipment through various sensors and data acquisition systems.
- The software's ability to normalize and trend data from multiple sensors to provide actionable insights is highlighted.
Challenges and Benefits of Implementing Insight CM
- Preston discusses the challenges clients face in justifying the investment in continuous monitoring systems.
- The potential benefits of workforce optimization and increased equipment uptime are highlighted.
- The importance of leadership buy-in and the integration of IT and OT systems to support the implementation is emphasized.
- Preston mentions the potential for reduced maintenance costs and improved safety through early detection and mitigation of defects.
Prognostics and Predictive Maintenance
- Preston introduces the concept of prognostics, which involves predicting the remaining useful life of equipment.
- The challenge of predicting the trajectory of equipment degradation and the role of physics-based models in this process is discussed.
- The potential for advanced statistics and artificial intelligence to enhance prognostics is mentioned.
- The importance of understanding the specific failure modes and degradation patterns of equipment is emphasized.
Roadblocks and Future Directions
- Preston identifies the main roadblocks to implementing online monitoring systems, including resource constraints and the need for subject matter experts and IT support.
- The importance of leadership buy-in and the integration of IT and OT systems is reiterated.
- The potential for supply chain optimization and improved financial performance through better asset management is highlighted.
- Preston discusses the exciting developments in the field, including the integration of artificial intelligence and advanced analytics.
Conclusion and Contact Information
- Scott summarizes the key points of the conversation, emphasizing the importance of asset management and the potential benefits of Insight CM.
- Preston provides his contact information for listeners interested in learning more about Cutsforth and Insight CM.
- Scott thanks Preston for the insightful conversation and encourages listeners to reach out for further discussions.
- The podcast concludes with a call to action for listeners to stay engaged and continue the conversation in the coming year.
If interested in being on the Industrial Talk show, simply contact us and let's have a quick conversation.
Finally, get your exclusive free access to the Industrial Academy and a series on “Why You Need To Podcast” for Greater Success in 2025. All links designed for keeping you current in this rapidly changing Industrial Market. Learn! Grow! Enjoy!
PRESTON JOHNSON'S CONTACT INFORMATION:
Personal LinkedIn: https://www.linkedin.com/in/prestontoddjohnson/
Company LinkedIn: https://www.linkedin.com/company/cutsforth/
Company Website: https://www.cutsforth.com/
PODCAST VIDEO:
THE STRATEGIC REASON “WHY YOU NEED TO PODCAST”:
OTHER GREAT INDUSTRIAL RESOURCES:
NEOM: https://www.neom.com/en-us
Hexagon: https://hexagon.com/
Arduino: https://www.arduino.cc/
Fictiv: https://www.fictiv.com/
Hitachi Vantara: https://www.hitachivantara.com/en-us/home.html
Industrial Marketing Solutions: https://industrialtalk.com/industrial-marketing/
Industrial Academy: https://industrialtalk.com/industrial-academy/
Industrial Dojo: https://industrialtalk.com/industrial_dojo/
We the 15: https://www.wethe15.org/
YOUR INDUSTRIAL DIGITAL TOOLBOX:
LifterLMS: Get One Month Free for $1 – https://lifterlms.com/
Active Campaign: Active Campaign Link
Social Jukebox: https://www.socialjukebox.com/
Industrial Academy (One Month Free Access And One Free License For Future Industrial Leader):
Business Beatitude the Book
Do you desire a more joy-filled, deeply-enduring sense of accomplishment and success? Live your business the way you want to live with the BUSINESS BEATITUDES…The Bridge connecting sacrifice to success. YOU NEED THE BUSINESS BEATITUDES!
TAP INTO YOUR INDUSTRIAL SOUL, RESERVE YOUR COPY NOW! BE BOLD. BE BRAVE. DARE GREATLY AND CHANGE THE WORLD. GET THE BUSINESS BEATITUDES!
Reserve My Copy and My 25% Discount
Transcript
SUMMARY KEYWORDS
industrial innovations, asset management, predictive maintenance, condition monitoring, holistic equipment, performance predictive, Insight CM, sensor integration, workforce optimization, equipment uptime, maintenance costs, safety issues, IT-OT convergence, leadership buy-in, supply chain optimization
Scott. Welcome to the industrial talk podcast with Scott. MacKenzie Scott is a passionate industry professional dedicated to transferring cutting edge industry focused innovations and trends while highlighting the men and women who keep the world moving. So put on your hard hat, grab your work boots and let's go Well,
industrial talk is here, and:I'm doing terrific. It's a pleasure to be here, Scott. Uh, absolutely
wonderful that you are here. You're talking to some of the best listeners on the face of the earth all around the world right now. So, yeah, I hear the weather is nice in Central Texas right now.
It is starting to cool off, but we're still running our air conditioners.
Yeah, we're too here in Louisiana, south southeast Louisiana. Yeah. Do you get snow where you live,
only during odd years, yeah, and when that happens, we sometimes lose a lot of power.
Well, yeah, because you're, you're part of ERCOT.
Well, you know, there it has its pros and its cons. It
has its pros and cons. Well handled. Preston on that. All right, listeners, we're going to be talking a little bit about holistic equipment condition monitoring and perform, performance predictive maintenance solutions. That's what we're going to be talking about. But before we get into that conversation, Preston, give us a little background on who you are and a little background on cuts worth
f the millennium, in the year:Please do because I have some questions about the Insight cm and the market out there continue.
Yeah. So, yeah. So I've been with cuts forth about three months now. Prior to that, I worked with a small, yeah, a small artificial intelligence company that was trying to still working very successfully, adding artificial intelligence to predict their maintenance. Spent a little time with an information technology systems integrator that was involved with something called refinery of the future, where I learned a little bit about the it ot convergence. And then prior to that, I was with a reliability services company by the name of allied reliability, where I kept the and all the metrics and the KPIs and got my cmrp from smrp. And so I've, I've had a fun journey in this condition monitoring and predictive maintenance, starting with technology, learning the business, trying to understand the challenges of implementing fleet wide monitoring applications, and ultimately, I'm back with my team that I started with as we try to roll all the pieces of the puzzle together. Well, you've
seen a lot of changes happening within the marketplace. I mean, it's it has changed, and it's changing even more rapidly, I would have said, say, because of the advent of AI, and the ability to be able to have greater insights into those assets, and be able to sort of have tactical action items to say, go here. Do this. This is what's happening. So, very interesting. All right, it's noisy out there just FYI. It's noisy in the world of asset management systems, condition monitoring systems, how does the insight, cm, how does that differ from some of the other products out there?
Well, the first vision that we had for insight, cm, when we started putting the software together. Was partly an internal vision, being able to leverage and utilize all the different condition monitoring technologies. Many of the asset management softwares that came about in the 80s and 90s were really focused on vibration. More or less, we looked at the market, the vibration condition monitoring market was much larger than oil sampling, electrical signature analysis, thermography, and it really was the major focus of many of those applications. We also took the voice of the customer, one of the largest southeastern power generation companies in North America really wanted to be able to leverage all of the technologies. And as they looked for a way to do a fleet wide condition monitoring, not only of their critical assets, their turbine generators and so forth, they really wanted to be able to do more balance of plant and and they needed to leverage multiple technologies. So that's one of the unique features of insight cm, is being able to digitize all of the condition monitoring technologies that are in play today, bring them together into a single platform, which makes it easier to compare trends from the vibration, from the lubrication, from the temperature, thermography and so forth, to collaborate amongst the technologies and identify defects in the equipment. So
take us through that. Let's say I'm interested. I hear what you're saying. I'm having a common platform that really will be able to provide the insights that I needed for need, for my management of assets, take us through sort of a typical implementation of that solution, if I'm if I say, hey, Preston, help me. What would be what? What are those steps? Yeah.
So the first thing is, I want to understand the assets that you have in your plant that are important that you want to address. Sometimes those are bad actors. Sometimes we start at the top of the criticality list. Sometimes we might start with balance of plant, just to make sure that this technology is really going to work before we put it on critical assets. So we need to understand the assets. What are the name plates? What's the function of the asset? So functional failure is really failure, and that's what we're trying to prevent. So we need to understand what the assets doing, what are the components and the likely, improbable failure modes that we might experience. Subject Matter Experts understand that bearings wear, that lubrication loses viscosity, that there's electrical faults, and motors that pumps have cavitation and vein issues, same thing with fans. They get debris on them. There's a laundry list of failure modes that are that subject matter experts understand, and so we want to address those likely and probable failure modes be able to detect the defects that lead to those failure modes, so that we have plenty of time to plan and schedule mitigating action. So
hate to interrupt real quick, but you're talking to the individuals that are on the ground and talking about those assets in a pretty extensive way. I would imagine that each client is different in how they approach their assets. Typical, how long does a that understanding phase take?
Usually, it's a matter for for cuts forth, for our team to understand the assets and how they're being used in a plan, probably within a week or two. Yeah, just a few man hours. Do we understand what? What are the assets? We have our own subject matter experts to say, Oh, this is a centrifugal pump. It's horizontally mounted. It's got a strictly coupled this is what we can express. They expect from this size based on horsepower and flow and pressure.
Bad. That's, that's cool. Okay, continue. Yeah,
so and, and then we then we also, so once we understand the failure modes, and then we need to identify sensors that can detect the defects. So vibration, lubrication, electrical signature, thermography, ultrasound, performance, pressures and flows, what is the work that the equipment is actually doing? Because we can monitor those and get some context on how the pump is being operated, especially if there's multiple operating conditions that the equipment is going to be experiencing. How does it change operating states and so forth? So we bring all that together try to understand what sensors are valuable. People to understand the performance and defects in the equipment that are going to cause failure.
So you're agnostic to the sensor themselves. You can pretty much interact with those sensors that are out in the field, your DCS, your PLCs, and then your other devices that are you know, might be placed on these assets, right? You're able to do that.
That is correct. And so from a from a business perspective, cuts forth is essentially a software and a services company. And so we work with sensors that are available on the market. We there's a number of wireless sensors. We're working to integrate more and more of those vendors into our platform. And then there's a several data acquisition systems that are permanently wired we can typically connect into one way or another. So now you have all this data. Yeah, a lot of the data is complex, a vibration signature. You can think of an orchestra. If you've ever been to this symphony, and you hear all kinds of sounds. How do you break those up and map them to the parts that are going to fail?
Yeah, if you were me, you just sort of give up because it's extensive.
But if you've been through vibration training, or training, or oral analysis training, you understand what the parameters that you want to calculate off of that sample of data that map to the kinds of failures that you might actually see in the equipment. And so there's some analytics right there on the front end that break apart those dense data sets into trendable features that you can track and trend over time. But they're also indicative of a failure, type of bearing in a race fault, loss of viscosity in lubrication. Maybe there's some humidity in the oil, the chemicals changing in the lubrication and so forth. Those are all indicative of a defect that's developing within the equipment, and typically the the analytics can bring it down to a particular part in the equipment that is suffering from that particular defect. So if we if we understand the lubrication is losing viscosity, the bearing is starting to make some tones, we we now have maybe even a cause for why that bearing is fatiguing. If the lubrication is starting to show failures or degradation, and then the bearings starting to show up. We know that we have a lubrication issue that's causing a bearing failure. We might be able to correct the lubrication problem before the bearing wears and extend the life of our equipment, whereas with just vibration, you might not understand the cause of the bearing, you just know that it's wearing and it's getting worse, and and you may replace the bearing, but you might not have addressed the results. So,
so with that analogy, if I have I have a an asset, and I'm pulling vibration, I'm pulling sound, ultrasonic, maybe some heat, do you normalize that data on that asset in your system, saying, okay, here is the complete picture of that motor, whatever it might be, right? And then be able to, sort of green, yellow Reddit, you know, from a from a that perspective, is that what we're talking about, that's
what we're talking about, is being able to put some some indicators out of all of the equipment that are in scope for the online condition monitoring. Which ones have no defects detected? They're all green. Which ones have defects that we can see developing, but the level, the alert levels are still kind of low. I see the bearings starting to make noise, but it's at a small enough level that I probably wouldn't write a work request by itself. Now maybe if the lubrication and the temperature and the ultrasound are all telling me something, then that might give me enough evidence to actually write a work request to do some mitigating action, but yes, so we indicate the equipment in the equipment hierarchy in the software is yellow. We're detecting defects, and then we would probably go to an orange or a red, depending as as the severity increases over time, which really means that your time to plan and schedule you're mitigating action is starting to decrease.
Does it provide some sort of indication of or predictive indication of when they might think about failure? So in the case of this yellow asset, over a period of time, hey, it's still okay. I. Uh, but we see it's, it's failing at this rate. Do you do you have that capabilities? That
capability is is coming, and what's really interesting is that they're the best kind of the the term I call prognostics. How much remaining useful life, remaining functional capability do I have out of this, out of this equipment, before it fails to perform its function? We would call that prognostics. And the there's really two pieces of that puzzle, and what I've been describing earlier is really the physics of failure. So physics based models that all of us, subject matter experts can understand, we can explain we've been trained on them. We know what the alert levels are for the various sizes of machines and components that we're trying to monitor. So those physics based models, through the technologies and the training that the subject matter experts have been through, really form the basis of understanding. Do we have a defect, and is that defect getting more and more severe over time? Now the tricky part is, can we predict the future? If we think of the P to F curve, and I'll draw mine the way I look at it, where the equipment is normal and healthy at the top of the curve and it starts to degrade down till the functional failure, and I'm and I'm maybe a third of the way down that curve. How do I predict that trajectory, which is non linear? And so if I have multiple signals, multiple sensors that are each sort of saying, Yeah, I can see a little bit of a change. That's not good, but it's small. We can normalize, as you say, bring that data together through some I'll call it advanced statistics, all part of that artificial intelligence portfolio that could start to give me a curve structure, especially if the if the knowledge is there on how that particular type of equipment tends to degrade with similar failure modes in play over time, and then we have an opportunity to traject that P to F curve for that piece of equipment, for that particular failure mode into the future, and that tells us, can We make it to the next outage. There are several companies trying to do that. Some of them claim that they're having great success. Some of them aren't using physical space models. They're all doing data driven so you really have to have years of failure data. So there's a number of different plays. And actually that's really exciting part of the work that we're doing, it cuts forth, is building in that direction, starting with the physics based models, those are explainable. Those are understandable. And working with our artificial intelligence teams to try to project that PDF curve for
that. Yeah, that's sort of the that's the Shangri law of asset management. If I can, if I have a high confidence level of being able to predict when that particular asset will fail, then I can plan it in a better way. I can hopefully sweat it a little bit. I feel comfortable with sweating that asset, pushing it out a little bit. It has real bottom line financial benefits if I knew how to do that. Yeah,
it really does, and I call that supply chain optimization, so I don't have to express parts and people into my plant to fix something. Now I can plan and schedule and get things on everybody's calendar, including my suppliers, and everybody goes home feeling comfortable.
Yeah, I agree with you 100% sorry, that's my dog in the background. My studio has my dog. So it is what it is,
yeah? Well, it's real world, right?
Yeah, absolutely. So anyway, with all that said, with all that wonderful reality that exists, where do you see it going, and what are the roadblocks?
Yeah, so really, the first roadblock that most of our clients and prospects actually have is, how do I get started? Yeah, this sounds great. Yes, we're having failures that are catching us off off guard. Yes, we have some route based subject matter experts that inspect our equipment from time to time. We're catching some we're not catching them all. How can I build a business case, a business justification to be able to justify putting sensors in where we're continuously monitoring at least once a day, in the case of wireless sensors, these parameters that can detect those defects and one of the initial benefits to most organizations. Is just workforce optimization. So if you think about the subject matter experts that spend all day or four days a week, in a typical fashion of walking around the plant with their handheld analyzer for just one technology, typically making measurements on equipment, inspecting perfectly good equipment, finding a few pieces of of defects that they identify, but then they only spend 20% of their time, that one day a week, actually doing analytics, and they're in essentially a Data Silo, so they're not able to bring that data together. So you have workforce optimization, if you can take some of those machines off Route and put them online now, that analyst, that subject matter expert, can spend time not collecting the data, but spending more time looking at the data and learning from the data. So that's a workforce optimization that comes into play. But ultimately you're looking at, can I increase the uptime of the equipment before I actually have to pull it offline and service it? Can I lower my maintenance costs if I catch and plan and schedule and mitigate problems before they get worse? They typically cost less to and equipment that does not have defects, that is running smooth typically consumes less energy and less natural resources. OSHA would tell you that unreliable equipment is unsafe equipment. And yes, I have been in plants where machines grow parts kind of scary. Oh, yeah, but you don't want that to happen that was become real safety issues. So there's a number of objective and subjective business benefits at the at the higher level. And then if you look at organizations like the society maintenance reliability professionals, or reliability web and other organizations, they'll all tell you there's even other metrics that you can measure that may not bubble up into the financial system, but certainly help you understand how your workforce is adding value to the operation of your plant as you start to move some of the metrics and KPIs from the business of condition monitoring and predictive
maintenance. Final question, what are the roadblocks? What I mean, it makes sense, and I think that if you're a company, especially today, that you're not actively and aggressively seeking optimization of your your business through greater insights into your assets, you're going to be left behind. I just you're going to be competitively disadvantaged. What? What? What's the roadblock?
Well, yeah, so there's a kind of a number of roadblocks. Well, first and foremost, not all companies have, though the resources in their employment that they actually need to make this transition from Route based, or nothing at all, to an online monitoring system. So you need not only the subject matter experts for the technologies that you're going to deploy, but you also need information technologists, because this software has to run on a computer on premise or in the cloud, and then you've got the security and the it ot convergence issues. So you need subject matter experts. You need information technologists. You need an integration effort, and that may come from your IT team, I want to take my data from my inside cm software and make a message out of it when it sees a problem that I can transfer into my maintenance management system to essentially start a work request, so that the planners and schedulers and subject matter experts can figure out what to do with this developing defect, and when they're going to do that, you also need leadership. The leadership has to buy in to the benefit the organization. And certainly, we're all caught up in this artificial intelligence hype you might call it, but there's a, you know, a lot of good things that we're getting out of artificial intelligence today, so we have to understand that we're going to be able to leverage those technologies going forward, and we meet that foundation of good, solid data based on physics and the way our plant runs and the way our People in our process work together. So we need leadership to help us bring those those efforts together. And then, of course, operations, they're the ones that are running the plant and making productions. You have to serve the operations team in order to allow them to increase the capacity of the plant by keeping their equipment healthy. Be and available.
Excellent. Well done. Well summary, summarized. Preston. How do they get a hold of you? If somebody said, I'm enjoying what Preston is saying, I want to know more. What's the best way of being able to
get a hold of you? Email at my current employer, Preston, dot Johnson, at cuts for C, U, T, S, F, O, R, T, h.com, you can also find me on LinkedIn, and my slash is Preston Todd Johnson. All run together.
There you go. You're absolutely wonderful. Thank you. We're going to have all the contact information for President out on industrial talk. You can contact him. He knows what he's talking about, as you can tell by the conversation, he's got mad skills. You were great President.
Well, thank you very much, Scott. It's been very much a pleasure. I appreciate the intriguing questions that you brought forth today, and I really enjoyed our conversation. Oh,
well, thank you very much. All right, listeners, we're gonna wrap it up on the other side. We're gonna have, again, all the contact information for Preston out on industrial talk. Stay tuned. We will be right back. You're
listening to the industrial talk Podcast Network.
eciate your support. And it's: