Nick Haase with MaintainX
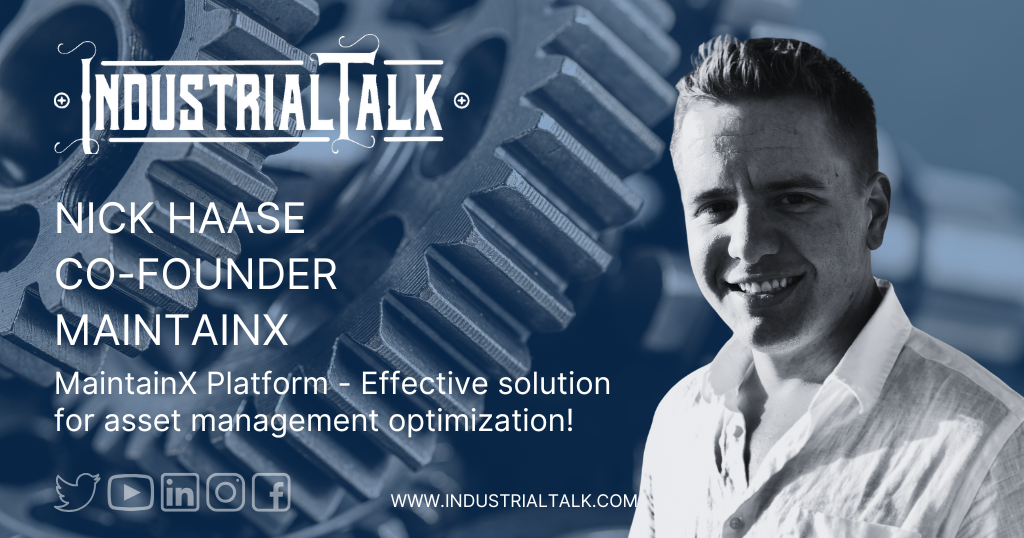
Scott MacKenzie hosts Nick Haase, co-founder of MaintainX, to discuss their mobile-first, frontline-friendly maintenance management software. MaintainX addresses the inefficiencies of traditional desktop-based CMMS systems by offering a mobile platform that streamlines workflows, reduces downtime, and integrates AI for predictive maintenance. Haas highlights the importance of capturing and digitizing data for AI tools to function effectively. He emphasizes the need for a solid data foundation and gradual AI integration. Maintain X aims to enhance efficiency, safety, and the onboarding of new workforce generations, leveraging IoT and AI to provide real-time insights and automate maintenance tasks.
Action Items
- [ ] Connect with Nick Haase on LinkedIn or Twitter to discuss MaintainX further.
- [ ] Visit the MaintainX website at getmaintainx.com to learn more about the platform.
Outline
Introduction and Welcome
- Scott MacKenzie introduces the podcast, emphasizing its focus on industry innovations and trends.
- Scott welcomes listeners and highlights the importance of industrial professionals in changing lives and the world.
- Scott expresses gratitude to listeners for their support and introduces the guest, Nick Haase, co-founder of MaintainX.
- Scott mentions Nick's previous appearances on the show and his active participation in industry events.
Promotion of Podcasting and Industrial Talk
- Scott discusses the benefits of having a podcast for industry professionals, emphasizing its role in opening doors and creating opportunities.
- Scott shares his personal experience with podcasting and how it helped his maintenance company succeed.
- Scott encourages listeners to consider starting a podcast and offers to help them get started with Industrial Talk.
- Scott highlights the importance of attention over marketing and how a podcast can leverage content to bring about opportunities.
Introduction of Nick Haas and MaintainX
- Nick Haas joins the conversation, reflecting on his previous appearance on the show and the changes in the industry since then.
- Scott and Nick discuss the evolution of MaintainX, a mobile-first frontline maintenance management software.
- Nick explains the gap in the market for mobile-friendly CMMS systems and how MaintainX addresses this need.
- Nick describes the initial challenges and the importance of capturing data digitally for AI integration.
MaintainX Workflow and Benefits
- Nick outlines the basic workflow of MaintainX, starting with technicians receiving alerts and accessing contextual information on their devices.
- Nick emphasizes the efficiency gains from having work instructions and parts lists readily available on the technician's tablet.
- Nick explains how MaintainX helps save time by reducing the need for technicians to go back and forth to supply rooms.
- Nick highlights the potential for predictive maintenance and AI integration to further enhance the platform's capabilities.
AI Integration and Predictive Maintenance
- Nick discusses the importance of having a solid data foundation for AI tools to be effective.
- MaintainX offers an AI procedure generator to help build workflows and save time.
- Nick explains how MaintainX can use AI to generate work orders based on sensor data and predictive alerts.
- Nick emphasizes the importance of user-friendly interfaces and the goal of making technology a co-pilot for users.
Challenges and Future of AI in Maintenance
- Nick acknowledges the challenges of change management and the skepticism towards new technologies.
- Nick stresses the importance of building a data foundation to support AI initiatives.
- Nick shares MaintainX's approach to helping clients start with basic workflows and gradually integrate AI.
- Nick highlights the potential for AI to drive significant improvements in efficiency and competitiveness.
Conclusion and Contact Information
- Scott and Nick discuss the importance of finding quality partners to help with AI implementation.
- Nick emphasizes the need for realistic expectations and a gradual approach to AI integration.
- Nick provides contact information for listeners interested in learning more about MaintainX.
- Scott wraps up the conversation, encouraging listeners to connect with Nick and explore the benefits of MaintainX.
If interested in being on the Industrial Talk show, simply contact us and let's have a quick conversation.
Finally, get your exclusive free access to the Industrial Academy and a series on “Why You Need To Podcast” for Greater Success in 2025. All links designed for keeping you current in this rapidly changing Industrial Market. Learn! Grow! Enjoy!
NICK HAASE'S CONTACT INFORMATION:
Personal LinkedIn: https://www.linkedin.com/in/nickhaase/
Company LinkedIn: https://www.linkedin.com/company/getmaintainx/
Company Website: https://www.getmaintainx.com/
PODCAST VIDEO:
THE STRATEGIC REASON “WHY YOU NEED TO PODCAST”:
OTHER GREAT INDUSTRIAL RESOURCES:
NEOM: https://www.neom.com/en-us
Hexagon: https://hexagon.com/
Arduino: https://www.arduino.cc/
Fictiv: https://www.fictiv.com/
Hitachi Vantara: https://www.hitachivantara.com/en-us/home.html
Industrial Marketing Solutions: https://industrialtalk.com/industrial-marketing/
Industrial Academy: https://industrialtalk.com/industrial-academy/
Industrial Dojo: https://industrialtalk.com/industrial_dojo/
We the 15: https://www.wethe15.org/
YOUR INDUSTRIAL DIGITAL TOOLBOX:
LifterLMS: Get One Month Free for $1 – https://lifterlms.com/
Active Campaign: Active Campaign Link
Social Jukebox: https://www.socialjukebox.com/
Industrial Academy (One Month Free Access And One Free License For Future Industrial Leader):
Business Beatitude the Book
Do you desire a more joy-filled, deeply-enduring sense of accomplishment and success? Live your business the way you want to live with the BUSINESS BEATITUDES…The Bridge connecting sacrifice to success. YOU NEED THE BUSINESS BEATITUDES!
TAP INTO YOUR INDUSTRIAL SOUL, RESERVE YOUR COPY NOW! BE BOLD. BE BRAVE. DARE GREATLY AND CHANGE THE WORLD. GET THE BUSINESS BEATITUDES!
Reserve My Copy and My 25% Discount
Transcript
SUMMARY KEYWORDS
Industrial Talk, asset management, MaintainX, mobile platform, workflow efficiency, predictive maintenance, AI integration, data collection, maintenance technicians, work orders, IoT connectivity, digital transformation, labor shortage, operational insights, technology adoption
Scott. Welcome to the Industrial Talk podcast with Scott. MacKenzie. Scott is a passionate industry professional dedicated to transferring cutting edge industry focused innovations and trends while highlighting the men and women who keep the world moving. So put on your hard hat, grab your work boots and let's all right once again. Welcome industrial professionals. Thank you very much for joining the number one industrial related podcast in the universe that celebrates you pointing at you in the video. You're bold, you're brave, you dare greatly. You're changing lives, and therefore you're changing the world. You are the heroes in this story. We thank you very much from the bottom of our heart. We just want you to succeed, and we just thank you for your support. We have a great conversation. The company is MaintainX. You might have heard him. He's been on the show before. Nick Haase is the individual co-founder, and we're going to be talking about their platform, MaintainX and workflows and greater insights into your assets. Let's get a correct and as I fade it down, yeah, it's a great conversation. He always delivers. Nick always never disappoints. We go to SMRP. There he is. We go to other events. There he is. His team is all there. They really have a passion to be able to sort of deliver a platform, a solution that really meets your, you know, asset management and maintenance expectations. They're just, they're quite nimble, if I could say that nimble. All right, so this, this again pops into my head. We want you again. I think it's a great opportunity to be in industry right now. There's a lot going on. There's a lot of buzz and and as as for anything, I want you to succeed. I want you to grow. I want you to expand. I want you to be successful in what you do, companies, individuals, Industrial Talk is here for you. If you are considering a podcast, you need to it is a powerful door opening solution for opportunities. It just is. I started it when I was having my maintenance company, and it did, it opened doors, had conversations and and it brought about a lot of success. And I and I want you to succeed. And therefore, if you haven't got a podcast, you need to contact me, you need to talk about what it would take to be consistent and to do a podcast. Because the reality is, this is just me. I it might just be, I don't know, some some people will disagree, but me, I think attention is far more important than all the the marketing stuff, because the marketing stuff is geared toward more attention. So you have a marketing platform which is podcasting. It gains attention. It is a content creating machine, and you must leverage that in such a way that it brings about opportunities. It opens doors. It just does. Now, if you have a podcast and you're saying to yourself, Scott, I'm just not getting the traction. It's, it's a task master. It is. You know, you got to be consistent at it, but I'm not getting the traction, the attention. Then the reality is, is that you have Industrial Talk. Put it out on Industrial Talk. Just come contact me and just say, Scott, I have a podcast. I would love to be able to put it out on Industrial Talk. That is, it's just that simple, because the realities of Industrial Talk is here specifically to help you succeed, bring about information and insights that make you do a better job at work, expand your company, keep current with all of the innovations that are happening out there. That's what Industrial Talk is all about. We want everybody to benefit from the conversation and and if you're saying, Scott, that's just too much, but you still need to amplify your voice. Contact me. Get on Industrial Talk. Talk about your technology, talk about your solution, talk about whatever it might be, because this ecosystem is all about getting that information out so that people can benefit from it. There ta da soapbox. Off. All right. Nick Haase, Nick, welcome back to Industrial Talk listeners. He's been on the show before. So how did, how was the last time we talked this? I
t was, I think it was back in:yeah, you guys, I think it was, wasn't it at SMRP, yeah, just on site, yeah, that was pretty cool. You've seen a lot of changes.
We have. Things are changing pretty quickly every day. In some ways, it feels like we were there yesterday. Others, it's lifetimes, yeah,
yeah, that's wild. Yeah, we're going to be talking about his platform, or MaintainX the CMMS system, mobile, if I remember, it's mobile, right? So, mobile
first, yes, sir,
yeah. See, see, it's cool. It's just, and you just keep adding to it, right?
Yeah, making it better, adding more functionality to help more more use cases and and see what we learning, learning from our customers too. We got more folks to learn from their lot smarter than we are, and they can help us kind of understand, you know, how to how to drive towards, you know, smarter innovations to help them. What are going to do? Seeing,
I go right into it, and I'm sorry listener, I just, I just start chirping right into the whole thing. And that's not very professional of me. I don't care. But let's who's missed your other conversation out on Industrial Talk, you can just type in Nick Austin, you're just good to go talk to us about who you are. Just give us a little 411 on who Nick is. Yeah, get into the MaintainX platform. Sounds
e launched a platform back in:rving. You're saying, back in:Yeah, it was, you know, when we launched the company, there were 300 plus CMS, type category companies in the market. So not an obvious place to start another, right is the market. Exactly what we realized is that most of those, if not really, almost all of them, were really dedicated for, you know, designed for desktop, which is not where these guys are doing the work. We're trying to help folks do the work, you know, in a system where they're doing the work in the field and and the what was happening is folks were still, even though they had, maybe, maybe, if they were advanced, had a system of record on their desktop, even though most still didn't even have that, they were printing work orders out. It's still very paper driven, very manual analog processes. If they were to look, you know, open a time capsule and look back 50 years, they wouldn't work the same way they were doing it 50 years ago. And so that was what we noticed. And we were like that. That's, that's not good because, you know, on one hand, I think we can generally appreciate that it's a little bit easier to share and exchange information and learn when we're capturing data and learning that digitally. But the other part of that kind of component, the other component that makes it really scary, is that we're rapidly moving towards this world of AI, and AI is heavily dependent on training data, and so if you've got all your let's say you are really disciplined, your team is documenting everything, and you've got it all on paper that's going to be really difficult to ingest and learn leverage AI tools to be able to help you do more with less. And that's really going to be, I think, the table stakes differentiator between companies that thrive over the next 510, years versus the ones that find themselves struggling to compete is the ability to integrate, integrate AI into their workflows across across the board. So
to level set what I hear and what you saw in the market, or what was lacking in the marketplace, because I been there, done that, you have a desktop CMMS, yeah, individual would go out. The field, identify assets, whatever it might be, try to create a work order. But they have to come walking back in, create a work order, get it all into the system itself and and then from there, then perform the work and so on. It's very inefficient type of workflow management. And many of the times, many of the times I would imagine in that scenario, you'd get some pencil whipping going on. It's hard to come saying, hey, here, here's a motor. It has this challenge, whatever it might be. And then I got to run back and and create a work order, and I don't want to spend the time. So you saw that niche take us through the typical workflow of a MaintainX solution, nothing fancy, nothing deep, nothing just, just. How does it work out in the field? Sure
take either real, real, basic, real, nothing sophisticated here, the technicians get, gets an alert notification on his phone, first tablet, and when maybe an operator has created a work request for a work order about part of the production line, that is, that is down, causing some downtime that maintenance technician may be across this, this opera, you know, this, this site. These sites are huge. Some of them are, you know, four or five, six football fields, at least wide. So there's, these aren't, aren't small, small facilities. He finds out that, oh, there's a motor that's wrong, you know, that's broken. There's some components that he's going to need to bring with him over there. So before he goes and runs over to work on that, on that repair or even troubleshoot it, he's got the contextual information that he needs right there on his tablet, right on his on his device, that he can run over to the parts, closet, the slide shelves, grab the pieces he needs, put it on his cart, and then head over there. And instead of having to go back and forth to the parks room, do the diagnostics, figure out what's going on, East he shows up. He's got the work instructions that he needs for that specific failure code already pre populated inside of MaintainX, so that he knows, hey, to fix this, you've gotta lock it out, tag it out, safeties first, and you gotta, and then you gotta come through and execute the following work instructions, you know, based on the OEM recommended, you know, protocol or or whatever that that organization has decided is appropriate for the for that, uh, piece of equipment, execute that that work document the parts that he's used close that work order out and and just that simple workflow there. We didn't stop a downtime necessarily. Maybe something happened. Maybe it was operator error. But nonetheless, you've gotten to the point where he didn't have he's saving what is likely going to be an hour plus time going back and forth to supply rooms, going and diagnosing things. So that hour, right? There is an hour of time that that company gets back to print more money, right, getting that production line back up and running. So that's sort of the basic light for use case. So I'm
an operator. I see that there's a an asset that is struggling for whatever reason, and then I, I the operator can go into the system itself right then and there, yeah, and be able to notify the maintenance professional to be able to go out and hey, this is it. Here's all the and then the system itself has all of the the documentation and all the information that is necessary for doing what is necessary on that, repairing that asset itself. You got, yeah,
s are doing it today, even at:through a scenario. Let's say I've spoken to many and it's you know it as well as I do. I'm collecting data off of that asset now that data is indicating that there's a possibility of failure. There's something, there's an anomaly that's taking place. Is it possible for that solution, that IIoT device, to be able to to notify the maintenance personnel the same, same but even even streamlining even more, to be able to get that maintenance individual out there with the correct information? Yeah,
absolutely. And so some of the things we talk to our customers about is what we call like a crawl, walk, run, journey. And some folks that crawl stage is basically we've got no paperwork, or all paper. We've got no paper like we're trying to just get, you know, none of all of our machines are dumb, and we're just trying to start, you know, treading water and catch our breath. They're doing that basic workflow I described up front. Now you're describing here with the IFT, that's when we can get to that, you know, walking and running, types of clients who are maybe a little further along in their digital, you know, transformation, maturity and their journey and and that's what we have the ability to connect directly with their sensors, their IoT, you know, whether it's SCADA systems PLCs grab that, you know, plug that right into an MQTT broker. And which, for those who don't know what that means, it basically, is a great, universal connector that we can talk to your machines and all that sensor data. Plug that right into MaintainX, and we build out automations and workflows that say, Hey, if the machine state is x and the following other parameters, conditions are y, z and so forth, then generate a work order automation that flags someone who's maybe electric certified, or, you know, whatever qualifications are required create a work order that you know maybe that machine is signaling that there's an e7 error code. And we can even generate the very specific troubleshooting directions and work execution steps that are necessary for that technician to show up, prepared with the equipment, tools that he needs to be successful, the parts, spare parts that he may need to replace, and the direct work instruction, so that as soon as that, that signal comes up that something needs to be done, he or she can go do that and and what that can be, you know, one of two scenarios. One is that the machine is already down. We've got to stop, we've got to we've got to, we got to fix it and get that back and running. Or it could be a predictive alert, something that says, hey, we're hearing, you know, the vibration is starting a little get a little bit funky, the machine still running. But if we get ahead of this, we might be able to prevent a costly downtime, a costly break, an injury or a safety risk, and get ahead of that. So there's kind of two ways that that data can help support those folks. So does
the algorithm associated with that scenario reside within MaintainX? So the parameters, let's say I have a vibration device on this asset, and you define normal operations. Then, then you define anomalies. Does that algorithm solution reside and MaintainX or do you? Do you? Do you depend on the logic residing in the device itself?
Yes to all the above. So we kind of do it in a couple of ways. One was, we can take that data and make, you know, our own automations out of it. We can also take in. A lot of folks work with vibration monitoring tools and solutions that have their own, you know, sophisticated some, lot of them have manual, you know, people who manually oversee those that data and make manual, you know, human based assertions that after they get AI based algorithmic flags, and then they'll they'll validate it. So wherever they're at we can kind of meet them in their journey and and help them kind of start to build those, those workflows that they need and and the nice thing is that all that for, you know, all that workflow building and those automations that you set up in our system, there's no code, so you don't have to be, you know, a computer scientist, or some overly, you know, you don't have to a lot of qualifications. You can just jump in there. And if you said, hey, if it's, if it's off, go send these types of people to it, so that we've tried to make it user friendly for folks that they can get in there and actually just get the work that they need done, rather than, you know, create more barriers to this, to entry there,
it seems to me, and correct me if I'm wrong, that that your your solution, MaintainX is to drive out as much inefficiencies, which I always look at time as. A component of inefficiency to drive as much time out of the identification of the asset, the challenge in that asset, and the corrective actions for that asset as well. So I'm trying to compress the time and minimize the the human impact that, you know, maybe the old way, here's a piece of paper, got to go over here, got it, and, you know, all the hands that have to be involved in that particular process. Is that, is that sort of a correct analogy?
Yeah, I think so. I mean, our goal here isn't to create more busy work for folks. Only. Technology should serve people, and everyone deserves technology that's easy to use, that makes their lives better, whether you're at home or on the job. And our goal is to help make sure that while you're on the job and you have, you know, a lot of other things to focus on and worry about, technologies not you know is there as almost a co pilot, a supporting cast member, not so much, something that is antagonistic with what you're trying to get done. So that sets the idea is that it's there to help you be a friend and be helpful. And if we screw that up, then we've kind of in person.
That's the goal, yeah. And I think it's all doable too. I think that outside of, well, change management, where you know, you know, that's, that's where you know, I I'm, I hear what you're saying, Nick, and I think that's great, and I understand the objective. However, you know, dot, dot, dot. Underline, underline, whatever it might be, but it, but I think it's doable, more so today than ever before, to be able to make that work, more efficient, safer, insightful, tactical. I mean, it's just, it's all available, and it's all with data.
Yeah, that's it. The Change Management still a real issue, and it's not unique up it's it's something that if you want to change, you know, anything in an organization, you've got layers of folks that you got to work through and teams to get folks you know, aligned on it. Our job should be to make that change management as simple as possible. Folks make sure that there's a full motion, and if we're giving folks a tool that makes their lives harder, they're going to naturally resist anywhere, right but, but if it's something that's helping them get, you know, then they're going to get that pull motion where they're like, hey, you know, we heard that this site, this plant over here has it. Why don't we have that tool now? And so, you know, there's but to be fair to the folks that that kind of have natural resistance to this, they've have a lot of scar tissue from very unfriendly software that they've been the years and and they've had all these deployments where, you know, it sounded great on paper and all the presentations, but then they deployed it and they didn't get any value out of it, or they didn't get the adoption. So there's a natural, you know, skepticism that, I think it's fair that this industry has towards technologies like this, but so, but nonetheless, you know that I think we, we still go out there and we do our best to try to make it let it sell itself, let it get let let it get into the hands of the folks and and let them kind of do the the polling for us and and That tends to be the best way forward and,
well, it can be quite noisy, especially in the world asset management. It's noisy and and for me personally, my head swims. Yeah, you know, I can. I can only imagine, from an operations perspective, that I think you touched on some really interesting facts that exist out there. And I think you're absolutely spot on when you say, Hey, I've already been down this road one time or two times or three times, and it all sort of ends in the same way, and that is, you know, I'm not happy now. Happiness, no joy in Mudville. Now let's, let's shift gears a little bit. Now we've talked a little bit about that ability to be able to to collect data, get the data, get the information. Now that's and then be able to do it in an efficient way. That, to me, is an AI type of scenario, tell us how MaintainX is sort of using hate to everybody's talking AI, right? It's like, How's MaintainX dealing with that?
rly to the way they ran. Like:That's a problem with large language models. I mean, you're talking something smaller, more manageable. There's still a lot of data don't give me, yeah, totally
not a big deal if you're writing song lyrics, kind of a problem if you're working on, you know, industrial equipment and safeties at risk and that sort of deal. So we put in some special guard rails to make sure our co pilot is going to give folks documented, you know, tool steps that that can make sure that they're doing things safely and accurately. So that's sort of how we're helping folks with AI today. Again, my biggest caution to folks is to be really thoughtful about what AI tools they're being you know, what the value that they're being promised is of a lot of these tools, because so much, so much of it is not going to work out of the box. And if you tried it, and what's going to happen is flips are going to come in. They're going to pay for these tools. They're not going to get what they expected because they didn't have a data foundation for it to learn on. And so these tools aren't going to work, and then they're going to build some resistance and skepticism towards AI, much like they did technology. You know, when those tools, that first wave wasn't working. And if we land there, your organization's going to be in a really, your leadership's going to be conditioned to say, You know what, we've been going just fine without AI for the past 80 years. We'll, we'll keep trudging along without it. And I think that's the biggest mistake any organization can make today. So I'm, you know, encouraging folks to really try to understand how the how these tools work, how to, you know, say, hey, maybe it's not. We're not going to get instant AI value today. You know, that's, you know, that massive ROI explosion, but it's really important to start to build the foundation and the framework that will allow you to be successful with AI over the next few years. Now,
I agree with that 100 Senate. And I, I, I caution individuals that are listening to this, and you're absolutely correct. I don't want the headache. I'm a manufacturer. I don't want the headache and, and this is creating another headache. But then there's the other organizations that say, yeah, it's, it's the future, and it's going to have to be, we're going to just have to take our lumps and bumps and and make it happen, because we know that there will be efficiencies that are gained, greater insights, greater knowledge, better operational uptime, whatever it might be. But the reality is, is that my, my humble opinion, you have to head down that road. You just have to, no matter what the bumps and bruises might look like, totally
agree. And I think that's, you know, we're going to look at the world maybe 510 years from now and and we're going to see a massive shift to companies in the Fortune 500 Yeah, and then beyond it, and there's going to be companies that you thought were blue chips never going to go down and and they're going to find that they can't compete with this new age companies that are taking advantage of some of this technology. So it's, it's a real threat if and companies have to take it seriously, but they have to be thoughtful about, you know how to approach it, and in an efficient way, for sure, can't,
which brings me to a point where, let's say I make that decision, I don't have the bandwidth. I'm manufacturing. I'm doing my manufacturing. I'm trying to keep this asset up and running, whatever it might be, and I don't have the bandwidth. This is where finding quality Sherpas to be able to help you along with that journey where you've done it before you you have a a methodology to be able to manage these assets, but then be able to deploy, or start to deploy, some sort of AI framework that that can be, you know, realized in the you know, future, whatever it might be, that, to me, is important because there's, there's a lot of people hanging shingles out there that saying, Hey, I'm an AI expert. I can do that. I can. And again, I, you know, a cautionary tell of Been there, done that type of thing. And you just need the right people to be able to help you along. Yeah,
we got the bells and whistle,:it makes sense. One last question. Where do you see things going? What's, what's uh, put your future hat on. What's uh, outside of AI being the, the latest and greatest, shiny little thing that's out there. Where do you, where do you see it going? What, what's, what's on the horizon for maintain? X, absolutely,
I think there's a, there's a lot of value, like, for a lot of really exciting. Things that start to come off of AI and not to beat that, you know, buzzword to death. But I think there's some real, real, potentially, like, super, really impactful innovation that's going to come out of that, from driving predictive maintenance insights, from connecting your machines so that your machines are giving you, you know, real time data. I think we're just starting to scratch the surface of what IoT can do, and because we've had this data for a long time, but we've always, you know, we've really, we've rarely had the opportunity to connect all of that in context with sort of the rest of the operation, what's going on in the production line, what type of materials are going through it, you know, what sort of work is being done on the on the maintenance, operational side, and being able to marry all of that, I think, is going to generate insights that are a lot more exciting and powerful than people expect. Our goal is to help enable you know, we're facing a labor shortage, and even as we continue to create more near shoring and bring more young people into the industry, that doesn't change the fact that I think we've got a pipeline challenge where more people are eight people are aging out of the workforce faster than they're coming into it. And so our goal right now is, is we're really excited about being able to enable this next generation to come in and be effective and be safe, and be able to sort of pass the torch effectively, to make sure that, you know, they can, they can keep these operations not only running at, you know, as they were, but but even challenge them to help make them better and more efficient. So we have some exciting, you know, product advancements that are helping enable that longer term vision, so that we can hopefully make, you know, unplanned downtime. I think in the past, for folks
say that's a whole nother conversation. Is the whole resource of the silver tsunami. And, yeah, how do you backfill that? Was skilled individuals. I mean, that's that's always going to be a challenge. You know, in fact, it was about 25 years ago. We were having the same doggone conversation, but we just didn't have the technology. We just didn't have it. We just knew that, oh my, these guys are leaving and and we don't have anybody backfilling, or we're just not having enough. Let's put it so we
raced, we raced the globalization, and we Bucha all offshore. And now you know how we handled it back then, this time, we're doing it in the inverse, where we're bringing more onshore and near shore. So we've got to make sure we can, we can help these kids and these young folks come in and get
successful and safe. Man, we're not, we're not talking about pieces of equipment that it could cause a little bit of a problem. You just need to be safe. Be safe. That's it. How do people get a hold of you? Nick, if they're saying, I want to know more about MaintainX, I want to know about how to get a hold of you. Nick, have a conversation. What's the best way reach
out to me anytime on LinkedIn or Twitter? X, Nick, Nick Haase, right here. And if you've got any questions about MaintainX, you go to MaintainX com, check that out. And, yeah, always happy to chat.
Nice. Alright, Nick, you are wonderful. You never disappoint. What's going on? It's, it's got a lot of frothing stuff going on. It's, it's fantastic. I It's an exciting time, I think. And your point about just tip of the iceberg, type of reality, and collecting data and analyzing data, and that, to me, is exciting, if I wish I was young. All right, listeners, we're going to wrap it up on the other side. We're going to have all the contact information for Nick out on Industrial Talk, his LinkedIn account, his his stat card. You'll be impressed with his stat card. All right. Stay tuned. We will be right back. You're listening to the Industrial Talk Podcast Network
has a wrap. That's Nick house. MaintainX is the company absolutely incredible work that they are doing in the world of asset management, maintenance, reliability and everything in between that's associated with that, collecting data, being able to analyze that data. You know it, you understand it, it's happening. You need to connect with Nick. You need to connect with Team MaintainX. You go out to Industrial Talk. There it is. There's a link to the stat card of Nick. So it's easy, easy peasy. Just do it all right. We're building the platform. I say it all the time. Industrial Talk is here for you. You got a podcast, put it on Industrial Talk. You want to do a podcast. You come and contact me. You want to start a podcast? Yeah, come and talk to me. I'm an open book. I am absolutely available for you and to have this conversation, because we want you to succeed. Industrial Talk is all about your success. It is a fabulous time to be in industry. All right. Be. Old, be brave. Dare greatly hang out with Nick change the world. We're going to have another great conversation shortly. So stay tuned. You.