Chris Colson with Allied Reliability
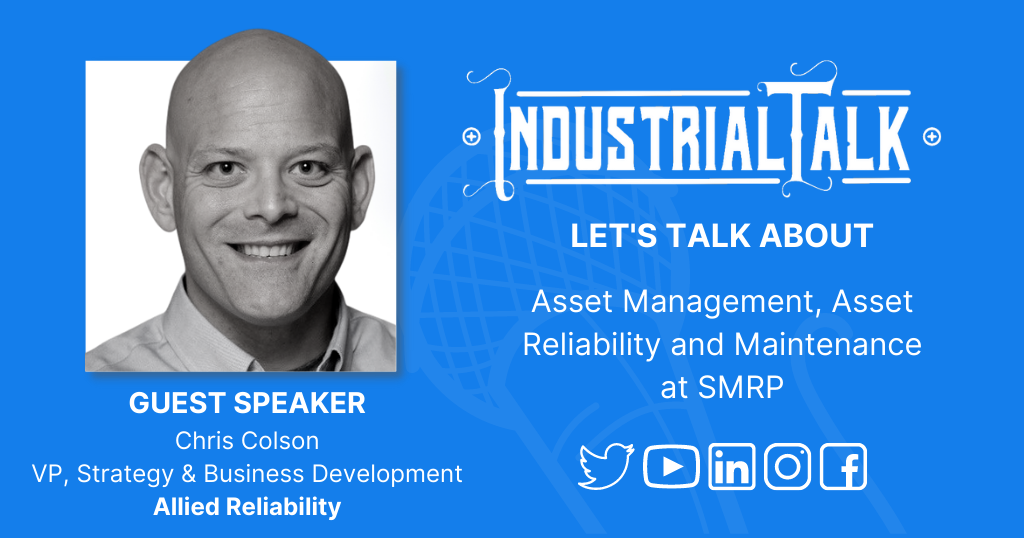
On this week's Industrial Talk we're LIVE at the 29th SMRP Conference talking to Chris Colson, VP, Strategy and Business Development with Allied Reliability about “Changing the Culture around Asset Management and Reliability”. Get the answers to your “Reliability” questions along with Chris's unique insight on the “How” on this Industrial Talk interview!
Finally, get your exclusive free access to the Industrial Academy and a series on “Why You Need To Podcast” for Greater Success in 2022. All links designed for keeping you current in this rapidly changing Industrial Market. Learn! Grow! Enjoy!
CHRIS COLSON'S CONTACT INFORMATION:
Personal LinkedIn: https://www.linkedin.com/in/chrisacolson/
Company LinkedIn: https://www.linkedin.com/company/alliedrel/
Company Website: https://www.alliedreliability.com/
PODCAST VIDEO:
THE STRATEGIC REASON “WHY YOU NEED TO PODCAST”:
OTHER GREAT INDUSTRIAL RESOURCES:
NEOM: https://www.neom.com/en-us
AI Dash: https://www.aidash.com/
Armis: https://www.armis.com/
Trend Micro: https://www.trendmicro.com/en_us/business.html
CAP Logistics: https://www.caplogistics.com/
Industrial Marketing Solutions: https://industrialtalk.com/industrial-marketing/
Industrial Academy: https://industrialtalk.com/industrial-academy/
Industrial Dojo: https://industrialtalk.com/industrial_dojo/
We the 15: https://www.wethe15.org/
YOUR INDUSTRIAL DIGITAL TOOLBOX:
LifterLMS: Get One Month Free for $1 – https://lifterlms.com/
Active Campaign: Active Campaign Link
Social Jukebox: https://www.socialjukebox.com/
Industrial Academy (One Month Free Access And One Free License For Future Industrial Leader):
Business Beatitude the Book
Do you desire a more joy-filled, deeply-enduring sense of accomplishment and success? Live your business the way you want to live with the BUSINESS BEATITUDES…The Bridge connecting sacrifice to success. YOU NEED THE BUSINESS BEATITUDES!
TAP INTO YOUR INDUSTRIAL SOUL, RESERVE YOUR COPY NOW! BE BOLD. BE BRAVE. DARE GREATLY AND CHANGE THE WORLD. GET THE BUSINESS BEATITUDES!
Reserve My Copy and My 25% Discount
PODCAST TRANSCRIPT:
SUMMARY KEYWORDS
reliability, organization, people, allied, maintenance, professionals, industrial, initiative, 29th annual, governance, piece, fluke, field, drive, conversation, safety, chris, technology, execute, work
Hello, and welcome to industrial talk. This is a special edition we were broadcasting live from the 29th annual SMRP conference. And this is a live recording from that particular event. And I want to put on your calendar this year 2020 to the 30th annual conference, and that is going to be held on October 17, to the 20th. And it is going to be in Raleigh, North Carolina. So put that on your calendar. The event in St. Louis was absolutely spectacular. And if you are a professional, focused on asset management, asset reliability, this is an organization for you. That is the SMRP 30th annual conference, and that is October 17. Through the 20th in Raleigh, North Carolina, all of the contact information will be out on industrial talk. So stay tuned. Let's get on with the conversation.
Welcome to the industrial talk podcast with Scott Mackenzie. Scott is a passionate industry professional dedicated to transferring cutting edge industry focused innovations and trends while highlighting the men and women who keep the world moving. So put on your hardhat grab your work boots, and let's go
all right you into history professionals. Welcome to industrial talk. We are broadcasting live from the 29th annual SMRP conference here in St. Louis, Missouri wonderful venue, incredible professionals just in reliability in maintenance wandering around. And just being great, great individuals. And we're also industrial Talk is brought to you by Fluke Reliability and accurate to Now what does that mean? So I go out to Fluke reliability.com. And then they there's a little blurb here that says provide maintenance and reliability professionals the data to do the job asset by asset where ever they are trying to argue about that when that's important because they do important work. And reliability professionals are great individuals and also Fluke or Accruent. If I go out to their website, it's solutions, real estate facilities and asset management, gaining insights to transform how your organization manages its physical assets. Another statement that you cannot argue about. All right in the hot seat for this particular event for this conversation, Chris Colson. He's with Allied Reliability. And we got a great conversation, Chris, how you doing my friend?
I'm doing great, Scott, thanks for having me.
This is good. Good to be here. Are you having a good conference,
I'm having a great conference. This is actually my 13th year coming. No kidding. I've been with Alan for 16 years. And we've been here and I've been a part of a number of different committees that I've served on over the years with SMRP. So I really really enjoy the show and love talking.
I really just the bottom line I just enjoy the individuals here who are passionate about what they are doing and trying to keep that asset up and running and doing and being asset doctors right and looking at and that's it man you're looking at a patient the patient could be a pump but you're trying to determine what the challenge is keeping it healthy whatever up. It's it's an it's a very if you're considering a profession consider reliability maintenance, whatever be either or I helped me define the difference. Maintenance are the ones that deploy the solution. Reliability identifies maybe the child has said hey, maintenance go out there, you will need this. We've got a bearing failure is that is that sort of the line of demarcation?
I think that's a great way of explaining it's gone. Yeah, guys and have their hands on the on the equipment. They they know the equipment, they want to fix what's wrong, but they need somebody to prescribe. Sometimes they don't have the insight or the or maybe the background to be able to say, specifically, here's what we need to do to to actually get better performance on a piece of equipment or fix it in a state that it can give us at least what it was designed for. Or maybe even better. And that's what the reliability engineer, I think brings to the game.
She's if I had to do it all over again, I would definitely consider this profession because it's just it's it's quite collegial. Most definitely. Now, we had this conversation and the conversation rolled around. Yes, there's great. The technology is out there. The sensors are out there. Things are available from a technology and innovation perspective. But it that's all fine and dandy, but if you don't have the right culture, people or whatever it might be. It's, it's well, it's not it's not optimal. That's for doggone Sure. Can we sort of start to explain a little bit about that. And why that is so important for organizations to sort of nail down.
Yeah, let me give you some of my thoughts and I get the opportunity and pleasure. Having worked with Allied and over my career. I started out as just a reliability engineer in the field. My background and I think it's a little bit like yours I understand. Used to be electrician
and baby a transmission journeyman lineman splicer. I did it all. And there it is. I ran crews. So he
I went out when I started my career, I knew I wanted to be an electrical engineer. So while I was going to college, I was also working as an electrician and then got to be a licensed electrician got to work with an electrical mechanical contractor in the state of Indiana, Warren largest privately held once. And and I got to get involved in design work of high voltage equipment. So I get kind of what you did in the field. And I got to see that with some of our team and then got to work with them from a design perspective. But as I transitioned in the career with Allied and on the reliability side, over over the first few years, I was out implementing projects and helping organizations get the right equipment strategy and not just understand the equipment strategy from a failure mode based. But what does it mean from an execution standpoint, and one of the pieces that I've been able to as I've elevated and moved on in the career and got to work with organizations and their leadership team was really talking about it, you know, we could throw lots of different technologies at it. But do we have we first of all identified how we're going to change the behaviors of either the operations team, the the maintenance team, and the overall culture to really drive a change that lasts? Too often, I think we get into a hurry of just fixing it and getting back up and running.
Yeah, that is a unfortunate reality that exists out in the field. And you're absolutely correct. I'll give you an analogy of exactly that. And I don't, I don't point fingers at anything, but it's just the realities. When we had a hurricane come through, powers out. Our only focus consumer get the power back up. So the professionals in the field are just trying to throw it up, they get it up, do they ever come back and say, Hey, I just sort of got this up to get the power going to get the ACS go, and so they never come back. And so that same thing can be applied to any organization where, Hey, you gotta get this thing back up. We got to do it. We don't have time get it? And so then, you know, they bubblegum it together, possibly. And then they forget about it, because there's another another thing. Yeah. And that's not the culture you want. No,
not at all. And so over the last four years with, with Allied, I've been able to work with leadership teams, and really work with them from a standpoint of putting in a governance process around any of their improvement projects that they're going to implement. And then governance entails what what are what are the expectations from everybody that's involved in this initiative. And when you look at that, from an organizational standpoint, there's people like health and safety, environmental and safety, you get, you get the finance department involved, because they have a piece, and HR HR is the folks that are recruiting the people in the skill sets that we need to be able to implement. So we will put what we would call a cadence of accountability around the execution of this initiative, and then across the entire organization and every function within the organization, and clearly identify what everybody's roles are, how quick how often we're gonna go back and report on the status update. And it's not just like, did we get this done that done? What are we ultimately driving for sure, in and executing on the strategic pieces that enable us to really get the full benefit out of the reliability initiative.
So you're saying, from a governance perspective, it's it incorporates, this body incorporates all aspects of that organization, that's from executives, finance, it, you name it all the way across and get everybody to buy in on the vision to support to be champions of whatever this initiative might be. That sort of it is.
And I've heard a number of different colleagues of mine, and some that I work with through the committees that we serve on here at SMRP that work with some of the other reliability solutions, providers, like allied, and sometimes we will toss words out like that governance piece. I'm very specific. And I like to promote that. You got to be concise. If you're going to ask an executive in his seat, that, you know, what is his role? You can't give him the whole spiel about maintenance and reliability, you've got to narrow down what's within his realm of control, and where do you want him to be involved and giving those pieces of information that he's going to act upon every single day or every single
week saying I like this? Because the reality is, is that I've seen a lot of, I mean, raise your hands if you've had a reliability initiatives fail, right? And it always gets down to what it always gets down to people, it rarely gets down to add a technology, blah, blah, blah, it's always getting down to that real passion and support by the executive team, whatever it might be. And I like how that you start there. Right? That's it, you know, somebody who cheer, we need a reliability program, we, we need to do better job at our maintenance and that means we got to do X, Y, Z. That's all fine and dandy, but you need that you need to start there. And I would imagine, correct me if I'm wrong, Chris. If you don't get that by and if you don't get that support, don't even go don't even go forward. Yeah,
I've seen a lot of wasted effort time but more than In anything it continues. If you don't get that effort, not only are you wasting people's time, but you're continuing to drive the culture in the opposite direction. Really? What? Right?
How many organizations? Have you ever been to where they said, we've tried reliability?
Nearly every one of them? That's right, I'll walk into right. That's right. And and then and then you've got it, what's different? What's going to be different this time? Yeah. And it's, well, because we're gonna get a chance to impact you.
And you know, the sad part about it is the simple fact that it makes sense. It's good business
it is. And you get back to it, though, you have to be able to tie all of those things back to helping them from from an executive perspective, how's this gonna better the company? How's it How am I going to get shareholders in, in in, you know, excited about this?
You have to? Do you ever pull in that that safety component? Because it is a safety conversation? as well?
Absolutely. Typically, when we go into to pull together a business case, one element of that business case is looking at the overall safety of the organization, how many safety events have they had? How are those things directly correlated with work that's being identified within their work system? And if you can see that there, they you know, I often when evaluating safety incidents, it's hard, hard to find where they've captured what they've done to correct that from a from a standard working, working position within every each, each day of their right. So do I see that that safety incident led to not only a root cause analysis, but did it change the way that they're executing the work in the field, and it's tough to find that, and typically, because they've not pulled it all together. And
so how it's important, we all establish that this is, this is, I believe, very strategic for businesses to truly nail down that culture, have that governance structure, that strong supportive governance structure. What I also find is that some people just get overwhelmed. Where do I start? Why how, you know, it can't be Big Bang? What what what do you recommend people to consider? Like, like, here's the elephant, where do we start?
Yeah, so my, what I've seen work pretty well, Scott, is one, we still start with the people. We start with understanding, do I need to do I need to? What's my current process overall, to drive the reliability? But more importantly, how do the people fit in? And do I have the right skill sets, and that's where you have to work very closely with HR and put together individual development plans for every person in the organization that's going to help support that reliability and initiative, we like to start there, because ultimately, you need the people to be able to execute and you need everybody aligned. So we start there, we put the governance piece in place, and then you start focusing in on the technologies, right, yeah, because it's then when I, when I have all of those pieces in place, I've got the right people with the right skill sets to execute and change the behaviors and execute the correct work, then bring it on, load me up with information from technologies.
There's been a lot of buzz conversation around training, resource development, and also the challenges associated with finding people. And there's been a, you know, a real concern expressed, do you find a clear, concise strategy around training allows people to sort of grab a hold of the vision of what you're trying to do and something? I don't know, just something more career driven as a less, you know, whatever defined? And
yeah, I do. And if you'll allow me to share and experience to be
a part of this year, it's about you. Anyway, Chris,
I was working with an organization. And we were talking about just this topic about training and building out IDPs for their entire organization. And when I say their entire organization, we were going across multiple business units. And they've got around 65 to 68 plants worldwide. We developed a three year program for every one of their maintenance technicians, whether it's electrical, mechanical, their supervisors on the operation side, as well as their maintenance site. We are at the beginning of of well, we've all been dealing with with the COVID situation. And so when we first started talking about this, we were going to be on site, we're going to be delivering that training curriculum and pulling people in, we were kind of tossed a curveball just like everybody else, how are you going to? What are we going to do? We can't stop we want to do something, right. And so we broke those sessions up, we delivered all of them virtually. For the first year, we delivered three different courses and we touched 520 people within their organization. And we brought them in in two hour sessions, two hour sessions over the course of about a month to be able to get through some of the first classes and that first class really is what's the overall strategy, what's the vision, what what, what benefit and what's in it for me to be a part of a reliance ability initiative. And we touched on that from every position, what benefit? Are they going to see? How does it make their life and their work better? And then also, how does it drive pride to the overall organization. So we're like, Man, I'm happy to work here. And I see the the companies investing in my future. That was, you know, we started to see that change over the course of that first, first course that we deliver, we got feedback from from VPS, as well as the guys that are in the field executing the work, and to saying, I think this is going to work. I love the bite size pieces. I love, love you guys conveying the overall strategy, and how I play into that strategy and where I can actually advance my career. I know what it's going to take to get to that next level. Right within the organization. So yeah, and
you're you've touched on, I mean, I love that by and I love the fact that they can determine and say, Yes, I see my role in this initiative. I see it. And so I can play that role. And I can play it to my best ability. And I don't know, man, I think you guys are doing great work out there. I think companies just have got to continue to do this. Yeah. No matter how much pain no matter how much I mean, training Come on. How do people get a hold of you, Chris?
You reach out to allied reliability.com Take a look at our website or send me an email at coastal sea at Allied reliability.com or professional.
You've done this before. It sounds like oh my gosh, it's incredible. All right, opportunity. Thank you very much for joining industrial talk. And also remember, we're broadcasting from the 29th annual summer SMRP conference in St. Louis, where the best of in reliability and maintenance reside. It's a fantastic time. And also, I want to just give kudos to accurate and Fluke go out to accurate.com as well as Fluke reliability and find out more great people. Great company. Great solutions. Thank you once again for joining industrial talk. If you're not we're going to wrap it up on the other side. So stay tuned.
You're listening to the industrial talk Podcast Network.
All right. Once again, thank you very much for joining industrial talk and a hearty thank you to Chris Coulson allied reliability as the company. I'm telling you, you need to find trusted individuals, Chris, trusted, if you are in the market for reliability maintenance, improving your maintenance, asset management, you need to talk to individuals like criticals and allied reliability. Also, if you are in that profession, SMRP is a must. Now the 29th annual conference was a fantastic event. This was 30th it is October 17 through the 20th and it is in Raleigh, North Carolina. It is a must tend to bet if you are a reliability professional, great, great venue, all right. To change the world you need to hang out with people like Chris. So hanging out with all of his contact information will be out on industrial time. And also also you need to continue to educate, collaborate. Definitely innovate. Be bold, be brave, daring greatly. We're going to have another great conversation shortly. So stay tuned.
Transcript
Welcome to the industrial talk podcast with Scott Mackenzie. Scott is a passionate industry professional dedicated to transferring cutting edge industry focused innovations and trends while highlighting the men and women who keep the world moving. So put on your hardhat grab your work boots, and let's go
all right you into history professionals. Welcome to industrial talk. We are broadcasting live from the 29th annual SMRP conference here in St. Louis, Missouri wonderful venue, incredible professionals just in reliability in maintenance wandering around. And just being great, great individuals. And we're also industrial Talk is brought to you by Fluke Reliability and accurate to Now what does that mean? So I go out to Fluke reliability.com. And then they there's a little blurb here that says provide maintenance and reliability professionals the data to do the job asset by asset where ever they are trying to argue about that when that's important because they do important work. And reliability professionals are great individuals and also Fluke or Accruent. If I go out to their website, it's solutions, real estate facilities and asset management, gaining insights to transform how your organization manages its physical assets. Another statement that you cannot argue about. All right in the hot seat for this particular event for this conversation, Chris Colson. He's with Allied Reliability. And we got a great conversation, Chris, how you doing my friend?
I'm doing great, Scott, thanks for having me.
This is good. Good to be here. Are you having a good conference,
I'm having a great conference. This is actually my 13th year coming. No kidding. I've been with Alan for 16 years. And we've been here and I've been a part of a number of different committees that I've served on over the years with SMRP. So I really really enjoy the show and love talking.
I really just the bottom line I just enjoy the individuals here who are passionate about what they are doing and trying to keep that asset up and running and doing and being asset doctors right and looking at and that's it man you're looking at a patient the patient could be a pump but you're trying to determine what the challenge is keeping it healthy whatever up. It's it's an it's a very if you're considering a profession consider reliability maintenance, whatever be either or I helped me define the difference. Maintenance are the ones that deploy the solution. Reliability identifies maybe the child has said hey, maintenance go out there, you will need this. We've got a bearing failure is that is that sort of the line of demarcation?
I think that's a great way of explaining it's gone. Yeah, guys and have their hands on the on the equipment. They they know the equipment, they want to fix what's wrong, but they need somebody to prescribe. Sometimes they don't have the insight or the or maybe the background to be able to say, specifically, here's what we need to do to to actually get better performance on a piece of equipment or fix it in a state that it can give us at least what it was designed for. Or maybe even better. And that's what the reliability engineer, I think brings to the game.
She's if I had to do it all over again, I would definitely consider this profession because it's just it's it's quite collegial. Most definitely. Now, we had this conversation and the conversation rolled around. Yes, there's great. The technology is out there. The sensors are out there. Things are available from a technology and innovation perspective. But it that's all fine and dandy, but if you don't have the right culture, people or whatever it might be. It's, it's well, it's not it's not optimal. That's for doggone Sure. Can we sort of start to explain a little bit about that. And why that is so important for organizations to sort of nail down.
Yeah, let me give you some of my thoughts and I get the opportunity and pleasure. Having worked with Allied and over my career. I started out as just a reliability engineer in the field. My background and I think it's a little bit like yours I understand. Used to be electrician
and baby a transmission journeyman lineman splicer. I did it all. And there it is. I ran crews. So he
I went out when I started my career, I knew I wanted to be an electrical engineer. So while I was going to college, I was also working as an electrician and then got to be a licensed electrician got to work with an electrical mechanical contractor in the state of Indiana, Warren largest privately held once. And and I got to get involved in design work of high voltage equipment. So I get kind of what you did in the field. And I got to see that with some of our team and then got to work with them from a design perspective. But as I transitioned in the career with Allied and on the reliability side, over over the first few years, I was out implementing projects and helping organizations get the right equipment strategy and not just understand the equipment strategy from a failure mode based. But what does it mean from an execution standpoint, and one of the pieces that I've been able to as I've elevated and moved on in the career and got to work with organizations and their leadership team was really talking about it, you know, we could throw lots of different technologies at it. But do we have we first of all identified how we're going to change the behaviors of either the operations team, the the maintenance team, and the overall culture to really drive a change that lasts? Too often, I think we get into a hurry of just fixing it and getting back up and running.
Yeah, that is a unfortunate reality that exists out in the field. And you're absolutely correct. I'll give you an analogy of exactly that. And I don't, I don't point fingers at anything, but it's just the realities. When we had a hurricane come through, powers out. Our only focus consumer get the power back up. So the professionals in the field are just trying to throw it up, they get it up, do they ever come back and say, Hey, I just sort of got this up to get the power going to get the ACS go, and so they never come back. And so that same thing can be applied to any organization where, Hey, you gotta get this thing back up. We got to do it. We don't have time get it? And so then, you know, they bubblegum it together, possibly. And then they forget about it, because there's another another thing. Yeah. And that's not the culture you want. No,
not at all. And so over the last four years with, with Allied, I've been able to work with leadership teams, and really work with them from a standpoint of putting in a governance process around any of their improvement projects that they're going to implement. And then governance entails what what are what are the expectations from everybody that's involved in this initiative. And when you look at that, from an organizational standpoint, there's people like health and safety, environmental and safety, you get, you get the finance department involved, because they have a piece, and HR HR is the folks that are recruiting the people in the skill sets that we need to be able to implement. So we will put what we would call a cadence of accountability around the execution of this initiative, and then across the entire organization and every function within the organization, and clearly identify what everybody's roles are, how quick how often we're gonna go back and report on the status update. And it's not just like, did we get this done that done? What are we ultimately driving for sure, in and executing on the strategic pieces that enable us to really get the full benefit out of the reliability initiative.
So you're saying, from a governance perspective, it's it incorporates, this body incorporates all aspects of that organization, that's from executives, finance, it, you name it all the way across and get everybody to buy in on the vision to support to be champions of whatever this initiative might be. That sort of it is.
And I've heard a number of different colleagues of mine, and some that I work with through the committees that we serve on here at SMRP that work with some of the other reliability solutions, providers, like allied, and sometimes we will toss words out like that governance piece. I'm very specific. And I like to promote that. You got to be concise. If you're going to ask an executive in his seat, that, you know, what is his role? You can't give him the whole spiel about maintenance and reliability, you've got to narrow down what's within his realm of control, and where do you want him to be involved and giving those pieces of information that he's going to act upon every single day or every single
week saying I like this? Because the reality is, is that I've seen a lot of, I mean, raise your hands if you've had a reliability initiatives fail, right? And it always gets down to what it always gets down to people, it rarely gets down to add a technology, blah, blah, blah, it's always getting down to that real passion and support by the executive team, whatever it might be. And I like how that you start there. Right? That's it, you know, somebody who cheer, we need a reliability program, we, we need to do better job at our maintenance and that means we got to do X, Y, Z. That's all fine and dandy, but you need that you need to start there. And I would imagine, correct me if I'm wrong, Chris. If you don't get that by and if you don't get that support, don't even go don't even go forward. Yeah,
I've seen a lot of wasted effort time but more than In anything it continues. If you don't get that effort, not only are you wasting people's time, but you're continuing to drive the culture in the opposite direction. Really? What? Right?
How many organizations? Have you ever been to where they said, we've tried reliability?
Nearly every one of them? That's right, I'll walk into right. That's right. And and then and then you've got it, what's different? What's going to be different this time? Yeah. And it's, well, because we're gonna get a chance to impact you.
And you know, the sad part about it is the simple fact that it makes sense. It's good business
it is. And you get back to it, though, you have to be able to tie all of those things back to helping them from from an executive perspective, how's this gonna better the company? How's it How am I going to get shareholders in, in in, you know, excited about this?
You have to? Do you ever pull in that that safety component? Because it is a safety conversation? as well?
Absolutely. Typically, when we go into to pull together a business case, one element of that business case is looking at the overall safety of the organization, how many safety events have they had? How are those things directly correlated with work that's being identified within their work system? And if you can see that there, they you know, I often when evaluating safety incidents, it's hard, hard to find where they've captured what they've done to correct that from a from a standard working, working position within every each, each day of their right. So do I see that that safety incident led to not only a root cause analysis, but did it change the way that they're executing the work in the field, and it's tough to find that, and typically, because they've not pulled it all together. And
so how it's important, we all establish that this is, this is, I believe, very strategic for businesses to truly nail down that culture, have that governance structure, that strong supportive governance structure. What I also find is that some people just get overwhelmed. Where do I start? Why how, you know, it can't be Big Bang? What what what do you recommend people to consider? Like, like, here's the elephant, where do we start?
Yeah, so my, what I've seen work pretty well, Scott, is one, we still start with the people. We start with understanding, do I need to do I need to? What's my current process overall, to drive the reliability? But more importantly, how do the people fit in? And do I have the right skill sets, and that's where you have to work very closely with HR and put together individual development plans for every person in the organization that's going to help support that reliability and initiative, we like to start there, because ultimately, you need the people to be able to execute and you need everybody aligned. So we start there, we put the governance piece in place, and then you start focusing in on the technologies, right, yeah, because it's then when I, when I have all of those pieces in place, I've got the right people with the right skill sets to execute and change the behaviors and execute the correct work, then bring it on, load me up with information from technologies.
There's been a lot of buzz conversation around training, resource development, and also the challenges associated with finding people. And there's been a, you know, a real concern expressed, do you find a clear, concise strategy around training allows people to sort of grab a hold of the vision of what you're trying to do and something? I don't know, just something more career driven as a less, you know, whatever defined? And
yeah, I do. And if you'll allow me to share and experience to be
a part of this year, it's about you. Anyway, Chris,
I was working with an organization. And we were talking about just this topic about training and building out IDPs for their entire organization. And when I say their entire organization, we were going across multiple business units. And they've got around 65 to 68 plants worldwide. We developed a three year program for every one of their maintenance technicians, whether it's electrical, mechanical, their supervisors on the operation side, as well as their maintenance site. We are at the beginning of of well, we've all been dealing with with the COVID situation. And so when we first started talking about this, we were going to be on site, we're going to be delivering that training curriculum and pulling people in, we were kind of tossed a curveball just like everybody else, how are you going to? What are we going to do? We can't stop we want to do something, right. And so we broke those sessions up, we delivered all of them virtually. For the first year, we delivered three different courses and we touched 520 people within their organization. And we brought them in in two hour sessions, two hour sessions over the course of about a month to be able to get through some of the first classes and that first class really is what's the overall strategy, what's the vision, what what, what benefit and what's in it for me to be a part of a reliance ability initiative. And we touched on that from every position, what benefit? Are they going to see? How does it make their life and their work better? And then also, how does it drive pride to the overall organization. So we're like, Man, I'm happy to work here. And I see the the companies investing in my future. That was, you know, we started to see that change over the course of that first, first course that we deliver, we got feedback from from VPS, as well as the guys that are in the field executing the work, and to saying, I think this is going to work. I love the bite size pieces. I love, love you guys conveying the overall strategy, and how I play into that strategy and where I can actually advance my career. I know what it's going to take to get to that next level. Right within the organization. So yeah, and
you're you've touched on, I mean, I love that by and I love the fact that they can determine and say, Yes, I see my role in this initiative. I see it. And so I can play that role. And I can play it to my best ability. And I don't know, man, I think you guys are doing great work out there. I think companies just have got to continue to do this. Yeah. No matter how much pain no matter how much I mean, training Come on. How do people get a hold of you, Chris?
You reach out to allied reliability.com Take a look at our website or send me an email at coastal sea at Allied reliability.com or professional.
You've done this before. It sounds like oh my gosh, it's incredible. All right, opportunity. Thank you very much for joining industrial talk. And also remember, we're broadcasting from the 29th annual summer SMRP conference in St. Louis, where the best of in reliability and maintenance reside. It's a fantastic time. And also, I want to just give kudos to accurate and Fluke go out to accurate.com as well as Fluke reliability and find out more great people. Great company. Great solutions. Thank you once again for joining industrial talk. If you're not we're going to wrap it up on the other side. So stay tuned.
You're listening to the industrial talk Podcast Network.
All right. Once again, thank you very much for joining industrial talk and a hearty thank you to Chris Coulson allied reliability as the company. I'm telling you, you need to find trusted individuals, Chris, trusted, if you are in the market for reliability maintenance, improving your maintenance, asset management, you need to talk to individuals like criticals and allied reliability. Also, if you are in that profession, SMRP is a must. Now the 29th annual conference was a fantastic event. This was 30th it is October 17 through the 20th and it is in Raleigh, North Carolina. It is a must tend to bet if you are a reliability professional, great, great venue, all right. To change the world you need to hang out with people like Chris. So hanging out with all of his contact information will be out on industrial time. And also also you need to continue to educate, collaborate. Definitely innovate. Be bold, be brave, daring greatly. We're going to have another great conversation shortly. So stay tuned.