John Turner with Gafcon Digital
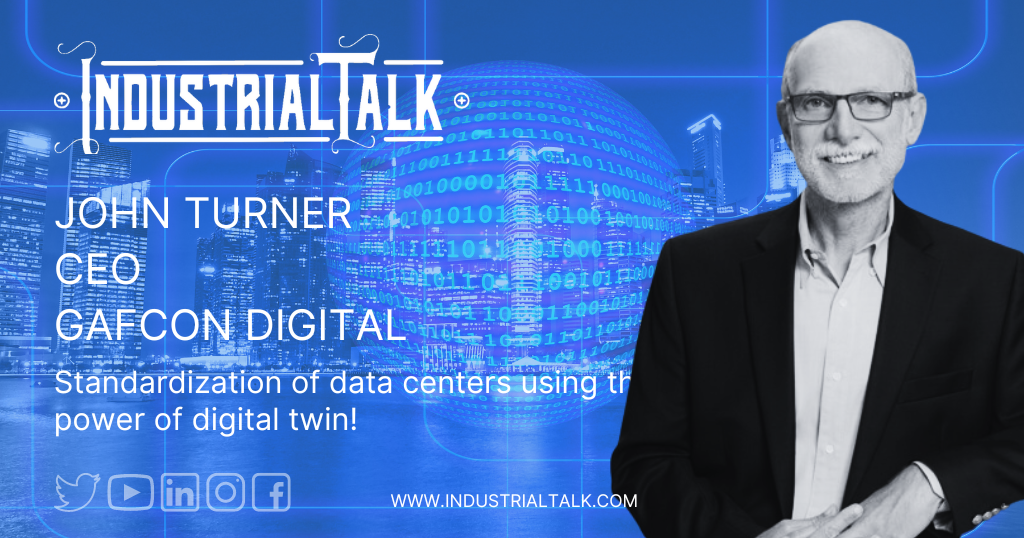
Scott MacKenzie hosts John Turner, CEO of Gafcon Digital, to discuss the application of digital twins in data centers and the construction industry. Turner emphasizes the inefficiencies in current construction processes due to silos and the need for a digital building lifecycle. He highlights the importance of digitizing construction through BIM and integrating data from various sources like reality capture. Turner explains the benefits of a digital twin, including predictability in safety, cost, and schedule, and mentions that buildings consume 41% of the energy in the US. He advocates for a transformational approach to organizational change management to achieve these efficiencies.
Action Items
- [ ] Send paper on digital twins and building energy usage.
- [ ] Reach out to John Turner at jturner@gafcondigital.com to discuss further.
Outline
Introduction and Overview of Industrial Talk Podcast
- Scott MacKenzie introduces the Industrial Talk Podcast, emphasizing its focus on industry innovations and trends.
- Scott highlights the importance of the podcast in educating and collaborating within the industrial community.
- The episode features John Turner, CEO of Gafcon Digital, who is a leading voice in the world of digital twins.
- Scott encourages listeners to visit the Industrial Talk YouTube channel for additional slides and information.
Introduction of John Turner and Gafcon Digital
- Scott MacKenzie welcomes John Turner to the podcast and asks for a brief introduction about himself and his company.
- John explains that Gafcon Digital focuses on developing a digital building lifecycle to improve efficiency in design, construction, and operations.
- John emphasizes the inefficiencies in the current design-construction-operational process due to silos and legal enforcement.
- Gafcon Digital targets serial builder-owner operators, particularly hyperscalers, retail, and life science sectors.
Standardization and Efficiency in Construction
- Scott and John discuss the concept of standardizing construction processes, using McDonald's as an analogy for optimized design and building processes.
- John compares the construction industry's lack of standardization to the automotive industry's use of lean techniques.
- Scott and John explore the potential for standardizing data centers and other large-scale construction projects.
- John introduces the idea of digitizing the construction process to create a foundational data model using BIM (Building Information Modeling).
Digital Twin and Reality Capture
- John explains the importance of digitizing the construction process to create a foundational data model using BIM.
- He discusses the role of BIM in integrating 2D, 3D, cost, schedule, embodied carbon, and document properties.
- John introduces the concept of reality capture, including 360 cameras, photogrammetry, laser scanning, and LIDAR, to bring real-time data into the design process.
- John differentiates between a visual twin and a digital twin, explaining the real-time monitoring and control capabilities of a digital twin.
Challenges and Organizational Change Management
- Scott and John discuss the challenges of shifting the construction industry to a more efficient, digital-twin-based approach.
- John emphasizes that the transformation has more to do with organizational change management than technology.
- He explains the need for serial builders to change their processes to scale efficiently, especially for data centers.
- John outlines the three-step evolution of the construction process: planning, design, construction, and operation, with a focus on a manufacturing perspective.
Benefits of a Digital-Twin Approach
- John highlights the benefits of a digital-twin approach, including predictability in safety, cost, schedule, and quality.
- He mentions that a BIM-centric approach can lead to cost savings of 10-15% in construction.
- John explains that 80-85% of the cost of a building post-construction is in its life cycle operations.
- He provides examples of how a digital-twin approach can improve efficiency, such as upgrading air conditioning systems in a university building.
Data Standards and Collaboration
- John discusses the importance of data standards and communication among different teams involved in the construction process.
- He explains the 3C approach: communication, collaboration, and correlation of data to improve overall performance.
- John emphasizes the difficulty of implementing these changes in practice but highlights the benefits of predictability and efficiency.
- Scott and John discuss the receptiveness of different industries to digitization and the importance of a holistic approach.
Energy Efficiency and Future Directions
- John mentions that buildings consume 41% of the energy in the US, highlighting the potential for energy savings through digital twins.
- He discusses the role of AI data centers in reducing energy consumption by being located near renewable energy sources.
- Scott and John explore the potential for digital twins to predict and monitor energy use in buildings.
- John offers to send Scott a paper on the subject and emphasizes the importance of addressing energy use in the digital-twin conversation.
Conclusion and Contact Information
- Scott MacKenzie wraps up the conversation, emphasizing the importance of the topics discussed and the benefits of a digital-twin approach.
- John provides his contact information for anyone interested in learning more about Gafcon Digital and their services.
- Scott encourages listeners to reach out to John and to continue the education journey through the Industrial Talk Podcast.
- The episode concludes with Scott thanking John for his insights and contributions to the discussion.
Finally, get your exclusive free access to the Industrial Academy and a series on “Why You Need To Podcast” for Greater Success in 2023. All links designed for keeping you current in this rapidly changing Industrial Market. Learn! Grow! Enjoy!
JOHN TURNER'S CONTACT INFORMATION:
Personal LinkedIn: https://www.linkedin.com/in/john-turner-2b616/
Company LinkedIn: https://www.linkedin.com/company/gafcondigital/
Company Website: https://www.gafcondigital.com/
PODCAST VIDEO:
THE STRATEGIC REASON “WHY YOU NEED TO PODCAST”:
OTHER GREAT INDUSTRIAL RESOURCES:
NEOM: https://www.neom.com/en-us
Hexagon: https://hexagon.com/
Arduino: https://www.arduino.cc/
Fictiv: https://www.fictiv.com/
Hitachi Vantara: https://www.hitachivantara.com/en-us/home.html
Industrial Marketing Solutions: https://industrialtalk.com/industrial-marketing/
Industrial Academy: https://industrialtalk.com/industrial-academy/
Industrial Dojo: https://industrialtalk.com/industrial_dojo/
We the 15: https://www.wethe15.org/
YOUR INDUSTRIAL DIGITAL TOOLBOX:
LifterLMS: Get One Month Free for $1 – https://lifterlms.com/
Active Campaign: Active Campaign Link
Social Jukebox: https://www.socialjukebox.com/
Industrial Academy (One Month Free Access And One Free License For Future Industrial Leader):
Business Beatitude the Book
Do you desire a more joy-filled, deeply-enduring sense of accomplishment and success? Live your business the way you want to live with the BUSINESS BEATITUDES…The Bridge connecting sacrifice to success. YOU NEED THE BUSINESS BEATITUDES!
TAP INTO YOUR INDUSTRIAL SOUL, RESERVE YOUR COPY NOW! BE BOLD. BE BRAVE. DARE GREATLY AND CHANGE THE WORLD. GET THE BUSINESS BEATITUDES!
Reserve My Copy and My 25% Discount
Transcript
SUMMARY KEYWORDS
digital twin, data centers, BIM, building lifecycle, organizational change, efficiency, reality capture, visual twin, digital twin, predictability, energy use, AI data centers, construction process, data integration, life cycle
Scott, welcome to the industrial talk podcast with Scott. Mackenzie. Scott is a passionate industry professional dedicated to transferring cutting edge industry focused innovations and trends while highlighting the men and women who keep the world moving. So put on your hard hat, grab your work boots and let's go. Hello industrial
professional. Thank you very much for joining industrial talk, the number one industrial related podcast in the universe that celebrates you. I'm pointing right at you in the camera because you're bold, brave, you dare greatly. You're changing lives. You are changing lives, and therefore changing the world for a better it's, it's just, it's simple math. It makes complete sense. This is the start of our innovation series. We're featuring John Turner. He's the CEO of Gav con digital, and he is the leading voice, one of the leading voices in the world of digital twin, and is and and just keep, just take note there's slides. So if you want to look at it on the video, just go out to industrial talk the YouTube channel. Find out the slides. It's, it's all there. Make it happen. It's, it's chock full of great information. Let's get cracking. Yeah, I've interviewed him before, and he didn't disappoint then he knows a lot. He knows a heck of a lot. And it's, it's, it's exciting to see specifically how they're deploying digital twin into data centers and trying to standardize the construction of many of these data centers, because they're out there. They're everywhere. You might not even know that they exist, but they are out there, and it is exciting to see what they're doing and how they're building these data centers, which are very important, very, very important going forward. Yeah, you know that? Well, who am I preaching to? All right, just a sort of a note of business. If you have a podcast, you're saying, hey, I need more traction on that podcast. Come talk to me. Get it out on industrial talk, we have a great community of followers that would be very happy to find out more information, because we're, you know, we're really into that education component. We're really into that collaboration, and as well as innovation, and specifically in the world of industry, it's just changing so dramatically. So again, I offer that out to you. If you have a podcast, you want greater traction, you want greater attention, stick it out on industrial talk. If you're thinking to yourself, how can podcast help me in bringing in other opportunities fill in that funnel you need to be talking to me too as well. I'll I'll help you get that started. I'll help you prop it up and and help you really define that strategy around why podcasting is important to your digital efforts. The bottom line, all right, if you one last thing, if you have a desire to be on the podcast, saying, I have a technology that I want to put out on industrial talk, just go out to industrial talk. Reach out to me and say, Scott, I've got this technology. It's sort of that AppSumo approach. We highlight it, we elevate it, we talk about the benefits of it. Because when you get right down to it, we're trying to solve problems, whatever the problem is, to find that problem, solve that problem, help everybody succeed. That's what industrial talk is about. It is a collection of individuals that you can collaborate with their open book. It's all out there. You want to talk to somebody on digital twin John Turner. Want to have conversation with you. He's he's an open book. And there are many, many professionals out there on industrial talk. Let's get cracking with the the conversation the webcast. I call it a webcast. It's a webinar. Ish, tomato, tomato, Potato, potato. It's the same thing. I just like webcast, the term webcast. John Turner, he's in the hot seat, and again, you want to see the handouts. You want to see what's being you know, talked about in a visual form. Go out to industrial talks YouTube channel and watch it there. So let's get cracking. Here's John. John, welcome to industrial talk. How are you doing today?
I'm doing fine. Thanks very much the invitation. Scott,
oh yeah, we were listeners. We were working through the technology, and we prevailed. We beat technology, and now it's working for our benefit. All right, John, before we get into the topic of BIM, give us a little background on on you and your company and what, what makes you so fantastic?
Well, the fantastic might be a stretch, but she'll make this. Different so it's got my company cap on digital, focuses on helping owners develop what we call a digital building lifecycle. There is so much inefficiency within our current design, construction, operational side, because of the silos that are really the way the industry has evolved, but also the way the legal system enforces that. And what we want to do is to to try and break apart those silos and provide a lot more efficiency, particularly for our main client base, which we defined as serial builder, owner operators. And that gives us a big focus on the hyperscalers, the people building a lot of data centers at the moment, but also on retail and on life science, where they're building essentially the same things over and over again. And if we can try and avoid the construction focus, where everything is built as a single entity, and get more with a manufacturing perspective, then we can benefit from building the same thing over and over again, but more efficiently.
See, I didn't, I didn't realize you, you're absolutely right. If I'm buying a McDonald's, I know McDonald's has a certain layout and and it's, there's, there's a logic to it, and they they've optimized their design and their building process. Is that, is that an accurate way of looking at that? That's
absolutely correct? Yeah. Now the The analogy I sometimes give is that Ford wouldn't let the people who are assembling f1 50s assemble every vehicle in a different way. They have a playbook. They they have the the parts arriving on the production line in a set manner. They're applying lean techniques. We don't do that within our standardized world of construction.
That is so interesting. I now that you bring that to my attention, I I can see that, and it's especially in the world where we're building these data centers, you'd think that there could be some sort of way of standardizing these, these construction efforts. Let's put it that way, so that just brings us into the the whole topic of, how do we how do we begin making that more efficient? How do we begin standardizing this process? So I'm going to share a little presentation that you put together take us through why BIM and all that good stuff. Okay, so
first of all, if we're going to standardize things, we have to digitize. And our world of construction is probably one of the least digitized industries, but I think McKinsey said, second only to agriculture, and even they have self driving tractors. So first of all, we have to have that foundational data model and BIM, which is building information model, but also building information modeling and Building Information Management gives us that ability to set up that foundational data model, which can then be leveraged between 2d, 3d, cost schedule, embodied carbon, properties and documents, but we Have to intercept the way. BIM is currently being used by architects, which is predominantly to produce the 2d drawings for permitting and GCS, who are predominantly using BIM to avoid clash issues in the field. From an owner's perspective, we want to use BIM as that foundational data model to tie everything together, not just for the construction process, but for the complete life cycle of the building.
Is this approach what we are talking about? I can see it being applied to new construction. Can it also be applied to existing structures, absolutely.
So as soon as we start to think of the data we need in a digital environment, we can start to bring in reality capture. So in reality capture can be 360 cameras. It can be photogrammetry, it can be laser scanning or LIDAR. We can bring that in as a reference model into the design BIM or rather than focusing on a BIM centric world, we can focus on a data centric world and bring everything into a real time or gaming environment, and start to integrate a lot of different perspectives. We've got the visual twin, we've got the digital twin, we've got them, we've got reality capture, all of which can be integrated in a single environment, and then the the use cases can be shared amongst all of the the actors or participants within the Digital. Lifecycle without having to build solutions for the individual silos
you touched on something that I need clarification. You have visual twin and digital twin. Tell us. What does that mean?
Yeah, so a visual twin is something if you go to slide 10 a little bit and scroll
on through and go to slide 10. Yeah, tell me when to stop. So,
couple more. There we go. So here is a visualization of a factory, and this is showing the factory floor. It's also showing the forklifts, which in this case are autonomous forklifts, driving through the factory. If we just provide a visualization of this, it's a visual twin, but we take it one stage further, so we make sure that everything that is happening in the the factory is then updated in real time, so or near real time, so that we can, for example, see exactly where the forklifts are, anywhere on that shop floor. We can also monitor the power requirements and what's happening with the power demands the particulate count within the factory. So if the particulate count goes above a certain level, we can restrict access to humans in that area, fans. So it becomes a way of controlling and monitoring the complete environment. So the difference is the visual twin is just the visual representation, but there is no updating of what's happening within that environment. A digital twin is then taking it to the next phase, which is integrating everything that's happening in that environment so that it can be controlled like it's a computer game.
So how do you begin taking all of this great technologies as I scroll again? No big deal going back to the slide. How do you begin impacting back up? How do you begin taking an industry that is set in its ways? We build buildings this way. This is what we do. How do you begin shifting that efforts into a more efficient approach and digital twin the construction
Scott? That's the foundational question. This has got very little to do with technology. It's all to do with organizational change management, yeah. And the first question is, not everyone is going to be open to doing that, and that's one of the reasons why we focus on serial builders, because they have the greatest benefit from changing their process. They realize that in the terms of the hyperscalers, the data centers, they cannot scale through the existing process. There's just not enough people to do it. So they have to change the way that they are building their data centers. Are, rather than constructing them, we start to think about, well, why not assemble them? Why not apply in manufacturing perspectives, and start to get into this very different perspective? So slide four, if we jump onto Slide four, sure, sure, you're starting to describe so we're jumping around, and we'll probably make it's not
a problem. So it's all about the conversation go ahead.
So the the evolution of the process is really in three steps. So first of all, existing process within our construction world is plan, design, construction, operate, very, very simple, and we normally find that the the owners and their contractors are organized within these four main silos. So what we want to do is to get more into this manufacturing perspective. So we have to change the way planning is done. It's really planning and developing the process so that it can be applied many times. We're then going to go into design with a lot of simulation, because the key benefit of a digital twin is to predict how you're going to do something, how a building is going to perform in energy or in people use, and then monitor how it actually is performing, and then make changes the next time you go through the cycle, if you're building a one off football stadium, it's probably not going to be advantageous. But if you're building 50 football stadiums, probably is advantageous. If you're building 100 data centers, it's certainly advantageous you're building five. 100 retail units, certainly advantageous. So then we're going to start to come out of design. And rather than the architect just handing over a set of drawings to a general contractor, we're going to make sure that design is focused on how you're going to manufacture, fabricate, deliver and assemble these units on site so they can be put together very quickly. And rather than going into a conventional test and commissioning process, you can then to start to use model based commissioning, so you can actually start to automate a lot of the process. And then when you get into operate, maintain, you're getting into this closed loop process, getting all the data on how the people are using the building, how the building is performing. And you can go through a lot of what if scenarios to then start to improve things. And that then leads into the final phase, where we start to consider design for manufacturing and assembly. So rather than just design we design in units. We design a kit of parts. So even in a standard office building, every building has restrooms. So why design each of those restrooms individually? Why not design them once and use them many times. And then you've got to change the way you go through the planning and development. You move around your Lego blocks. Make them fit the site, make them fit the use case. And then these Lego blocks can be assembled from the design kit of parts. They can be fabricated. They can be brought to site in a particular order, and then the whole process becomes more like a manufacturing assembly line.
We've been talking about the the data centers and and can you take a data center and build it to a certain level. Let's say three story, whatever it I have enough business to support a three story data center, but, but in three years, I'm going to have to add to it. Can you add to the design? If it's, if it's a Lego type of approach where I can then scale it to accommodate the market at that time?
That's a very insightful question. So I basically say there are three assumptions that we should make about buildings. First of all, something is going to be done in that building. It's going to be an office building or manufacturing or distribution. The second assumption is that that process that's done inside of that building is going to change before the building life expires. So we've got to design buildings so they're more flexible in terms of what can be done inside them. But then thirdly, buildings are becoming much more intelligent. In fact, if you go on to the next slide, Slide five, start to talk about how there are three main focuses from an owner's perspective. So starting at around about two o'clock. We've got the it focus. So there's a lot of systems which are involved within the the owner's life puzzle, ERP, CRM, the HR systems. There's data integration. We know about, data lakes, data warehouses, analytics, lot of technology being applied, but the first phase in the use of that technology was really to start to integrate the IT systems with the people and processes. That's the systems integration, front office, back office, type of things where you can go to the internet now you can see what stock is available. You can order that. But the the third phase of the evolution, which is what we're just entering now, is now to to start to integrate the the building with the processes which are going on inside of that building. And hence we have to integrate with the IT systems, so that we can completely eliminate these information silos and point solutions, we can get more predictability. We can start to better define how our organization is functioning, and that allows us to go through and make better decisions, better predictability with the budgets from an owner perspective. So it boils down to two things, we can increase the predictability of the business operation, and we can mitigate risks to that business operation by integrating these three focuses, of IT people and process and buildings.
And that gives that ability to be able to well. It gives, it gives the asset a much more usable life, right there. I mean, this is what always gets to me, is these, these data centers. People don't even know their data centers, or just look like buildings, and which is really fascinating to me, but, but they build them in such a way that that meets today's markets. And you know that data centers are are expanding dramatically and and there's going to be more reasons for them. And I just thought that now back to where we were at. This is a cultural mindset. How do you how do you begin changing that approach to building to include this sort of Venn diagram, digital twin systems? Yeah,
it's a transformational approach, and every transformation begins with a first step. So generally, we're focusing on the fact that we're going to need a lot of data in the operational environment. And the work we've done with insurance companies show that up to 60% of the data required to operate the building is lost within the design and construction process,
you're going to have to sort of clarify what is 60% of 60% of the
data, so knowing what an asset is. So we define assets as things, as systems and spaces. So when we go into building operation, a lot of the information has been collected or is needed. From an asset centric perspective, we want to know that we've got so many pumps or so many air handling units. We want to know manufacturing information, warranty information. We want to know how those systems are organized, so in a hospital environment, which of those mechanical systems providing clean air to the operating theaters. And so a lot of that information is available within the construction phase, but project controls in construction has a big focus on cost, not a focus on the asset. Oh
so 60% of that information doesn't exist after construction.
No. And because we're using from an owner perspective, because we're using GC systems collect that data, that information might not be transferred in the correct form into the owner systems.
GC, what
does that mean? General contractor and the guy,
holy cow, and that that is comes from insurance, and they're saying that 60% what? Okay, so 60% is gone. Take us continue with that thought process. So
what we focus on is making sure that that data can be collected in an organized perspective. So maybe if you bring up slide six, this will give an idea of of where we're coming from. So we want a data centric approach. So in the bottom left hand corner, we have the Building Information Model. This is setting up the basic data structure, because the the data intensity within the the BIM, it's a very granular data model. Every single BIM element can be associated with properties. They can be associated with a cost, it can be associated with documents. Can be associated with embodied carbon and also with the schedule. And so we're using the BIM as that central data model to start to bring together all of this information in a very holistic manner. And then as that project evolves from design through construction, we're looking at the the handover from the AE, the architect and engineering team, to the general contractor and their trade contractors, in a form that allows us to track the associated data to each of those assets right the way through into operations, and that allows us to set up the digital twin, which is very beneficial to the owner.
Are we looking at something that's you've got your standard process of how I'm going to build a building? Got it when I start to incorporate a data centric approach. Are you asking more from the general contract, or is this something that just happens? Or am I impacting somebody's time? Or do I just gather this information through the BIM and it's just happens
as long as. You have this process designed at the start. There is no additional cost, in fact, using a BIM centric approach, and maybe if you jump onto Slide eight, we we have what we call a a, 3c, approach. So first of all, we have to teach the team involved to communicate, because architects and general contractors and owners don't speak the same language. An architect might call a pump something a general contractor might call it something else, and the procurement might call it something different. Again, we're providing that basic data structure to allow them to communicate. Just because they all speak the same language doesn't mean they want to collaborate. So now we need to look at the processes, and these include the contracting processes to get everyone working together in a more holistic manner, and that allows us then to produce data which we can use to correlate all of these activities and improve these activities. So it's a very simple approach in principle, very much more difficult to make happen in practice. Practice,
yeah, I can only imagine, and but, but it might be difficult, but what's the benefits? What I mean, there's got to be a reason why I would want to do this. Tell us. Tell us. You know the upside,
the the key is predictability. It's knowing when your new facility is going to be available at what cost? So big focus on predictability, predictability of safety, because if we can, best way we can improve safety is to remove people from the site or to decrease the schedule so that people are not on site where most of the accidents happen. So we're looking at predictability in safety, predictability and cost, schedule and quality. So the this process is taken from an efficient and inefficient standard process, we've seen cost savings of 10 or 15% overall significant construction. Now that doesn't apply to every single project, because it's still a lot of efficiency in individual approaches, but a lot of clients will put together a contingency budget, which is 10 to 15% Our aim is to completely eliminate the need for that contingency through predictability.
It also through the life cycle of that asset, that building asset, if you establish the proper solutions up front, then it does continue to reap benefits throughout the life cycle. Is that correct? Absolutely.
And for an owner's perspective, 80 to 85% of the cost of the building post construction, they're in the life cycle aspects of it.
What does that mean? Okay,
,:Yeah, see, that's just, it seems like a no brainer. I mean, and, and what I hear, I can take existing assets, I can deploy a solution, what we're talking about, and begin reaping the benefits, or a greenfield type of arrangement from a construction perspective, and be able to establish a solid baseline so that the life cycle is far the life cycle of that asset is more efficient. It seems like a no brainer. Why? What are the roadblocks?
The roadblocks are largely organizational, because most owners still focus on a planning team, a design team, a construction team and an operations team. So most of our focus with our more enlightened donors is to understand what's going on in each of those silos and to start getting them working together. So go back to our three C's. We have to install data standards to teach them how to communicate, we have to then enable them to collaborate with that data, and then they can correlate the overall performance. So that's that's the slide. It comes down to those three steps, very, very simple to explain, extremely difficult to make happen in practice.
But are you finding that there's a greater receptiveness to the what you're talking about? It's happening, whether you like it or not, it's happening. And I yeah, I just think that if you want to be a competitive business, you need to consider all ways of being able to be more efficient. This just seems like a no brainer. It's
definitely happening. And there are a certain of the more the technology based companies which understand the value of digitization, the value of technology. They're very much open to the fact that, well, we're selling these solutions that work in the data centers, we should be eating our own dog food now. A lot of the retail companies are more focused on supply chain and distribution, rather than just the stacking shelves with products. They are highly technical, and they understand the value of technology. But if we can then start to link, for example, the refrigeration systems, with the products which are being sold at whole merchandising, we can start to make them more efficient by understanding how people are tracking through the stores what they're buying when they're buying it, when that product should be made available, whether it should be put on special offer, it's it's all down to the looking at this as a complete life cycle, not just in the silos of design, construction, operations.
Wow. It just seems bright. We're going to have to wrap it up here. But how do people get a hold of you? John, let's say that they want to find out more about what gafcon can do and have the conversation with you or your team. What's the best way to make that happen?
Probably just email me. Jay turner@gathcondigital.com
Yeah, because that's, that's the way to go. Anything we left out as a result of our conversation, or did we cover your topic thoroughly?
Yeah, I think we've, we, we've covered the highlights. This is a topic that I could talk for three or four hours about, because there's so much we haven't got into one of the key aspects of energy use within buildings, because Buildings consume 41% of the energy in the US. So key, you just dropped
a truth bomb. There. You're saying 41% of the the energy that is consumed in the United States come from buildings, absolutely, yeah,
and it's the fact that a lot of energy goes into making steel and concrete and glass. Lot of energy is used in keeping the buildings cool or heating them. So this 41% it's staggering
that is, that's another conversation that's huge. I'll
send you a paper that we wrote as part of the digital twin Consortium, which will introduce that subject, that in itself, is a subject which can be addressed through digital twins, through prediction of how a building is going to perform and then monitoring how it will
perform. See, I heard a staggering stat on, because of generative AI, because of that, that solution, the demand for power grows three times, three times the exist. Capacity because of generative AI. Yeah,
centers use a huge amount of energy. Yes,
and anywhere that you could take, slice away or begin to whittle down that 41% as it only helps, it helps the utilities dramatically, absolutely,
and that's why a lot of the AI data centers are now being cited rather than locally, because they're not so impacted with latency by having to be in the locality. They now build very large AI data centers close to hydroelectric or solar or nuclear power. Wow.
Didn't know that well, all I know, I was in Reston, and they had a lot of data centers. There,
lot of data centers. Yeah, in fact, they were running out of power locally.
Yeah, see, and I didn't know it, and they just looked like buildings. They looked like, you know, big buildings, and five people run it. Yeah, that's amazing. Well, this was a great conversation, John. I really appreciate it.
Well, thanks for the invitation, Scott.
I've enjoyed Yeah, awesome stuff. Okay, we're going to have all the contact information for John out on industrial talk. Absolutely, we're going to have send us that document. We'll have that um industrial talk as well, as well as Do you have any issues with us posting this presentation? No,
none at all.
Yeah, there you go. Man. All right. Thank you. John. Really appreciate it. Thanks. Scott,
bye. You're listening to the industrial talk Podcast Network.
John Turner, DEFCON digital is the company, and again, here at industrial talk, we're all about that education, collaboration and, of course, innovation. But the biggest part, and the best part about it, is that these individuals that you can reach out on industrial talk, have a conversation and continue that education journey. If you're in the world of industry, this is a must. It is changing so rapidly, so fast, that you have to maintain that education and being able to talk to individuals that are leading that way, John Turner is definitely a digital twin, is going to impact your life. Figure it out. Be a part of your your, you know, discussion and part of your education, right there. Reach out to John. You will not be disappointed, all right. Come to industrial talk. You have a podcast. You want to be on the podcast. You have technology. Put it out on industrial talk. Be bold, be brave. Derek greatly hang out with John. Change the world. We're going to have another great conversation shortly. So stay tuned.