Pat Newberry with Aptim
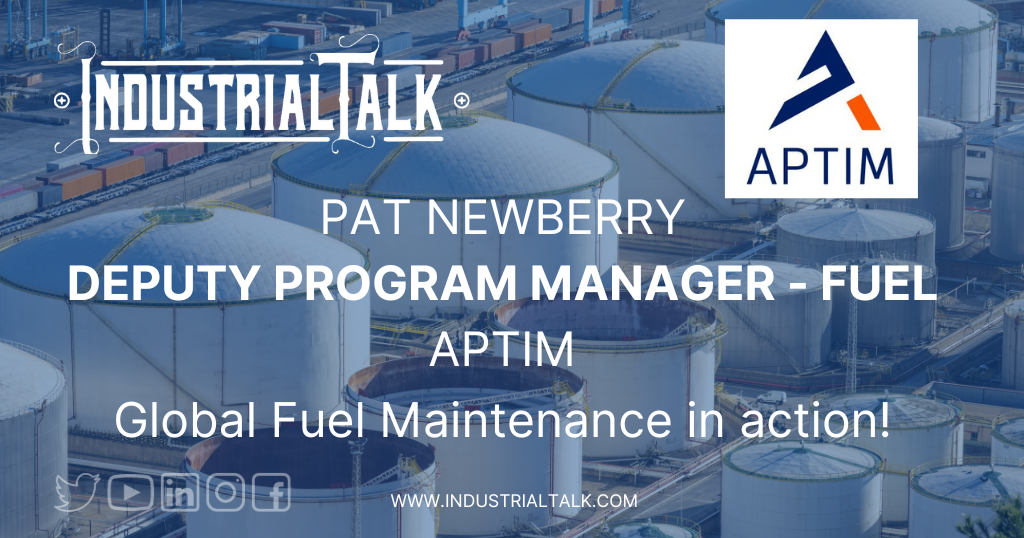
On this episode of Industrial Talk, we're onsite at Accruent Insights and chatting with Pat Newberry, Deputy Program Manager with Aptim about Global fuel maintenance in action. Here are the key takeaways:
- Securing operational technology with zero trust. 0:00
- Palo Alto Networks offers zero trust security for operational technology, simplifying management and providing comprehensive visibility and protection.
- Maintenance connect and company history. 1:16
- Pat Newberry discusses using Maintenance Connect at Gaylord conference.
- Pat has been with Aptim for 26 years, starting as a mechanical engineer and working in various roles, including with the Department of Energy.
- Pat is based in Denver and has been with multiple companies, including Shah, Shaw, CB and I, and McDermott, with experience in environmental engineering and infrastructure.
- Maintenance management for 70 military installations worldwide. 4:59
- Program manager for recurring maintenance of 70 military installations in the Pacific, including Japan, Korea, Guam, and the US.
- Pat manages 70 facilities worldwide, including those in Japan, and they are all on maintenance connection, with 97,000 assets to manage.
- Pat explained that the facilities are similar in region, with the same type of valving and structure, but the maintenance is the same regardless of location, and Maintenance Connection makes it easy to do repetitive tasks and ensure consistency across all facilities.
- Maintenance management for military assets. 9:35
- Pat has been working with maintenance connection for 2 years, with a slow transition to mobile capacity due to lack of cell service in Diego.
- Pushback from service members and funding agents has been a challenge, with the government organization setting boundaries and responsibilities for contractors and operating staff.
- Pat explains their company's asset management approach, including quarterly inspections and detailed inventory of valves and other equipment.
- Using Maintenance Connection for asset management. 13:26
- Pat describes how they were able to customize Maintenance Connection to fit their specific needs, despite initial hesitation due to its complexity.
- Pat highlights the importance of finding a solution that is flexible and intuitive, allowing them to manipulate it to suit their unique requirements.
- Pat highlights the benefits of a common platform for managing assets, including faster issue resolution and reduced travel for engineers.
- Pat discusses the potential of integrating 3D scanning technology with the platform to provide more detailed information on assets.
- Maintenance and asset management for fuel systems worldwide. 17:44
- Pat shared insights on maintenance and asset management for fuel systems worldwide.
Also, get your exclusive free access to the Industrial Academy and a series on “Why You Need To Podcast” for Greater Success in 2023. All links designed for keeping you current in this rapidly changing Industrial Market. Learn! Grow! Enjoy!
PAT NEWBERRY'S CONTACT INFORMATION:
Company LinkedIn: https://www.linkedin.com/company/aptimglobal/
Company Website: https://www.aptim.com/
PODCAST VIDEO:
THE STRATEGIC REASON “WHY YOU NEED TO PODCAST”:
OTHER GREAT INDUSTRIAL RESOURCES:
Industrial Marketing Solutions: https://industrialtalk.com/industrial-marketing/
Industrial Academy: https://industrialtalk.com/industrial-academy/
Palo Alto Networks: https://www.paloaltonetworks.com/ot-security-tco
Industrial Dojo: https://industrialtalk.com/industrial_dojo/
We the 15: https://www.wethe15.org/
YOUR INDUSTRIAL DIGITAL TOOLBOX:
LifterLMS: Get One Month Free for $1 – https://lifterlms.com/
Active Campaign: Active Campaign Link
Social Jukebox: https://www.socialjukebox.com/
Industrial Academy (One Month Free Access And One Free License For Future Industrial Leader):
Business Beatitude the Book
Do you desire a more joy-filled, deeply-enduring sense of accomplishment and success? Live your business the way you want to live with the BUSINESS BEATITUDES…The Bridge connecting sacrifice to success. YOU NEED THE BUSINESS BEATITUDES!
TAP INTO YOUR INDUSTRIAL SOUL, RESERVE YOUR COPY NOW! BE BOLD. BE BRAVE. DARE GREATLY AND CHANGE THE WORLD. GET THE BUSINESS BEATITUDES!
Reserve My Copy and My 25% Discount
Transcript
SUMMARY KEYWORDS
maintenance, assets, valve, work, industrial, platform, people, pat, company, inspection, put, connection, tanks, denver, manage, system, talk, operations, facilities, cb
Industrial Talk is brought to you by Palo Alto Networks. Palo Alto Networks offers zero trust for your operational technology without the PTSD. If you're in the digital transformation game, keeping Operational Technology secure and running smoothly, is a tall order. It's enough to make any coolest Operations Director wake up in night sweats Palo Alto Networks zero trust OT security delivers comprehensive visibility and security for all OT assets, networks and remote operations. It provides best in class security, while simplifying OT security management. It sees and protects everything in the network. And it automates threat detection while implementing zero trust across all operations. So sleep better at night knowing you have the most comprehensive platform to detect, manage, and secure your OT assets. Learn more about the Palo Alto Networks Zero Trust solution, go out to Palo Alto Networks.com That's Palo Alto Networks.com Find out more, you will not be disappointed.
Welcome to the Industrial Talk podcast with Scott Mackenzie. Scott is a passionate industry professional dedicated to transferring cutting edge industry focused innovations and trends while highlighting the men and women who keep the world moving. So put on your hard hat, grab your work boots, and let's go Alright,
once again, thank you very much for joining Industrial Talk. And thank you for your continued support of a platform that is celebrating industry professionals all around the world because you're bold, you're brave, you dare greatly. You are collaborating, you are solving problems. You're making lives better and the world a better place. So that's why we celebrate you on this podcast. We are also on site. This is the accrual insights at at what is this? So it's a Gaylord at the Gaylord, and it is it's a big place. It's a big place. But what is great about this particular conference is the fact that I'm looking out and I'm seeing people having great conversations, solving problems, having these conversations to make their business better. So absolutely wonderful. In the hot seat. We have a gentleman by the name of Pat, that Newbery Aptimize the company. And we're going to be talking about maintenance connect and how they use that product. So let's get cracking. How are you doing?
I'm doing okay.
Having a good conference.
It has been a great conference.
How long have you been with that?
I've been with Aptim for 26 years. Yeah. Second job out of college. Yeah. Oh my god. Yeah. It's I'm an oddball. I know that.
I want to take something did mark and grab your ear and look at that long term employee. Yeah, exactly.
Exact.
So where are sapling located?
We're located all over but our headquarters are in Baton Rouge, Louisiana, and I'm out of Denver, Colorado. I actually have not I've avoided that I avoided the corporate office.
Because we live in right outside of New Orleans in a town called Mandeville. Okay. Yeah. So, my wife was from around that area. So
yeah, we used to be Shah. Oh, yeah. So if you know Shah, that's what we used to be. I had ministry was Shaw environmental, and infrastructure is what we used to be. Yeah, well, we two companies ago so I originally was Stone and Webster. Yes. Went to Shaw.
Because whoever Yes, so
the pedigree was done in Webster right at a drop out of school. Yes. And then we transferred and get got bought by Shaw and then became a Shar E and I CB and I then bought us. Yep. And then CB and I went under and they sold our part off and back to I did it did. Yep. And then macoco briga bridge and iron is no more. I didn't know that. They were around forever. They Yeah, they've been around for it's crazy. Bad management. McDermott bought them. McDermott. Yep. And then they disappeared CB and I haven't know exactly what happened. But it was after they kind of partial us off and put us into a venture capital firm. And that's where we are. So
now we're rolling. So before we get into the conversation about what you do, give us a little background on who you are.
Well, I'm originally training as a mechanical engineer, grew up in Arkansas, went to grad school to go skiing and got an environmental engineering degree. Started with the Department of Energy after that, I did that for a couple years right out of school and ended up in Denver and been doing all sorts of stuff with all the companies that I've been with in the same seat.
Ah, Yeah, that's that's pretty good. Okay, so for the listeners also out there, probably have not
heard of APA. Yeah, probably, if not, we're kind of about what that company is. Yeah. So Aptim largely government consulting. What I do specifically is we work with federal fuels. So fuel systems on we build them, we construct them, we repair them. My job is to do all the maintenance for select locations. But after most of those coastal restoration, they do emergency response, disaster recovery. They were huge in Katrina. So hurricanes come through, we provide trailers, manage things for FEMA. We do laboratory management, environmental cleanup, nuclear decommissioning of ships, all sorts of things. It is a conglomeration of some really interesting, folks. Yeah.
How many people?
I think we're in the:h, you're doing all that with:I think. And lots of good relationships.
That's pretty cool. It's
pretty amazing.
So we've got maintenance connection. We, you are, what's your title?
installations in Pacific:But the ones Yeah, yes. Yes. Pacific? Oh, my goodness. Yeah.
It's it's pretty interesting stuff. What we do, everybody's like, Oh, we do that. And we're the only group that really does kind of international stuff for our company, which makes us kind of hard to deal with sometimes.
Make it hard to because we're International.
So we have to travel and the flights and security is most of the rest of the company is
just us. Do you have a team in the Pacific? Yep.
We have people that are at the bases. My engineers at a Denver will fly over and be in the field for two or three weeks at a time and they'll work there. We have a gentleman that's permanently stationed in Diego Garcia in the Indian Ocean. I haven't heard that name in a long time. Yeah. So we have a guy there. And we do all the maintenance for them as well.
So do you do you travel?
i less than I used to? But yeah, yes. I've been to all the places in Japan. I used to go once every three months. It was a wild ride. It is.
That is a guy that's a grind. Yes. Look at you. You're here to say I survived. Yeah. So with the fact that you have 70 facilities, right? Are they all on maintenance connection?
They all are on maintenance connection. So we have about 97,000 assets that we manage so pipes, pumps, tanks? Yeah. Yeah. It's been quite a Archer was trained to get it switched from our old system, get everything in and the assets updated, where we can use it and get our people trained. But it's, it's well worth it. We've We've really enjoyed it.
So are the facilities, there's some commonality with the facility. So you're able to say, hey, here's a pump here, there's a pump there, you can see how this pump is performing, be able to sort of triangulate some sort of Maintenance Solution around that. Yeah, yeah.
And the most of the facilities are built relatively the same regionally. So Japanese facilities are a little different than other places, but it's essentially a big tank, all the tanks have the same type of valving. And structure, there may be three entrance or four different pipe entrances to those. So they're kind of configured the same way. But a big isolation valve for the tank is maintained the same in Japan as it is in Alabama. So the work is the same, it's just a full summer, some have floating roofs, some don't. But the maintenance is the same if it's a floating roof in Seattle, or wherever we do the same stuff to them. And so it's maintenance connection makes it really easy for us to take all that put it in a stack, and be able to do things repetitively and do it over and over and make sure everybody has the same stuff in front of them.
The How long have you been on maintenance Connect?
We've been working with maintenance connection for the last two years, kind of coming up on our two years, roughly, but first year was mostly transfer of all of our Yeah, how
long did it take for that? Um,
it took us four or five months to get that going. And now our office staff so the office staff uses the, the, I guess the MRO piece, the maintenance piece that's on on the Desktop, we're just now getting the mobile capacity because like you said, like I was saying it was in Diego. There's no cell service of any of any consistency there. So we've been really involved with the Kinetic Development to make sure that it's going to work for our guys, because if it doesn't,
did you have any pushback? I mean, these these assets have been around for many years. Yep. So there was a number of years that were just, this is what we do. This is how we do it. This is how we maintain our assets. No, you can't tell me how I did this. And so on and so forth,
we get some of that. But most of that push is actually coming from the funding agent through the government. So the Defense Logistics Agency is the funding source for all of this. And they're the ones that say, no, these guys are going to do it. And so they have to deal with the service member that is out there doing the operations. And they've done a actually believe or not a pretty decent job of splitting that line and going, okay, these things are the stuff we're going to have contractors come in and do. This is what you're going to do. Now granted, individuals are individuals, but for the most part, the government organization has said, No, this is how we're going to do this. So we have this responsibility. These groups have that responsibility. So it's really been interesting in a training sense from Eric perspective, because we're under contract. So we know what we're supposed to do. The operating guys on the base are like, no, no, I've always done this, just like you said, we're like, Okay, well, let's sit down and figure out how can we all get this done, because everybody wants to make sure that the plane flies and doesn't fall out of the sky. That's what I tell my young engineers all the time.
Take us through the the, the the asset base, the you've got the tanks, you've got the piping, you've got the ship got the valves, you've got everything that's associated with it, how far into that whole model? Or is that just what you?
Well we go through and like when we went to new contract, we have a new site that we haven't been at, we usually send a team of four to five, depending on how large it is to do a full inventory. And they go out for two or three weeks at a time with iPads. And they're counting valves. And they're measuring what the makes and the models are. And we have a relatively unique set of about 150 classifications, which is determined maintenance connection that we count, so we'll kind of fire protection system that supports the tanks that the fueling system, but we won't count every valve will just say that's the fire protection, because that's all we have, we just have to make sure it's painted, make sure it works. But when I look at the valving system, I'm talking about a two inch valve and then the next valve and so I'll count very detailed if it holds fuel. So we call it our wetted surface approach. And so that inventory is really kind of our base point. And if we don't get it right, all of our maintenance down the road doesn't work. And maintenance connection does all of that for us, we come out to do a quarterly event and do quarterly inspections, we just have maintenance connection, where the assets generate the work orders, and I give a big stack to my guys in the field through their iPads.
There had been an evaluation of a platform, there's there's their appointments,
this maintenance jobs back in:again,
nimble, nimble and moves quickly. Yeah,
you don't have Have the friction if you can, sort of that intuitive capability of like, okay, I get it I Yeah, you know, yeah.
And we could manipulate it was it was flexible enough that we could manipulate it away from just a standard Facilities Maintenance Program, which is what it was designed for. And we have talked to guys, that's one of the been the great things about the conference. I've talked to some of the people that are truly facilities maintenance guys. And they use it and it seems very simple. And it's like a, like an old tennis shoe, it fits well, I've had to take that shoe and break it in and twist it and paint it and make it look a little different than what it does normally. But it wasn't that hard. I just had to think about it a little harder at the beginning. And then once we got to go in it's everybody's very happy with it. My team loves it.
With that said, you've had this journey into sort of how to a solution, a platform for managing your assets. What were the benefits associated with, with that common platform over the benefits some
of the benefits that we've my engineering staff, because our engineers do all the heavy lifting for us. And so they can see the data on the asset quickly, we can be consistent in common whereas In Maximo they couldn't see it, because it's too heavy, they couldn't find the thing. And I have photos and documents for that asset, they can see what's wrong. So when the, you know, the airman calls my service order engineer and says, Hey, my valve is broken, he can go, where is it? Can you give me a number? If you've stamped it, some of our valves have stamps on it as the standard? Can you give me that number or give me your number that they call it, they can pull it up in the system, they see a picture, maybe multiple pictures, all the work orders that have ever been done on that every inspection, they can see it like instantaneously while the guys on the phone and go, Oh, okay, now I know what's wrong. Now I can give you a solution. And I can make this work. And I can give you a service order and we can get this thing fixed.
Where do you see it going?
Our next big push for us is to get our 3d scanning, we do a 3d scanning. And we want to get those things connected. So that not only can you see it by picture by picture, he can go to our 3d scan. And I can see it. Think of Oh, that's my bow. Now I can see it not only is it just my valve, but now it's at height, or it's in a box or I can't really get it in there because it's a 500 pound valve and I got to lift a crane into the containment to lift the valve out. And yeah, they can do all that without having to, they just know what it looks like and not have to go there. And all my travels goes down. So I don't have to send them, ship them and fly them everywhere all the time.
Exciting stuff are awesome.
That compensates you do some interesting, a lot of different stuff than what they did here.
How do people get a hold of that
can give me a email george.newberry@abdom.com or cell phone is our telephone 303? I am but I don't use it that much. But I am out there. Okay, email to this email is the best. You're
wonderful. Thank you very much. All right, listeners. We're going to have all the contact information for Pat aka George, out on Industrial Talk. So if you're not you'll be able to contact him with no problemo. All right. We're gonna wrap it up on the other side. Thank you very much for joining. We
will be right back. You're listening to the Industrial Talk Podcast Network.
That was a meaty conversation, Pat delivered, that I enjoyed the fact that it was maintenance and asset management, inaction real on the ground maintenance, and reliability and asset management right there dealing with fuel systems all around the world. Very cool. Re listen to that one. That's really good. All right, we're building a platform as I continue to say all the time. This platform is dedicated to amplifying your voice, your industrial voice. It is necessary. We need you to succeed. Reach out to me go out to Industrial Talk, click Let's collaborate. Let's talk let's have a conversation. Because it's important that we continue to educate, we can elaborate and of course, we continue to innovate, as you can tell by Pat, there's a lot of innovation going on out there. And you know what causes some great, I guess concern is the confusion. Let's let's just demystify. People will be brave. They're greatly hanging out with Pat changed the world. We're going to have another great conversation coming from