Tara Holwegner with Life Cycle Engineering
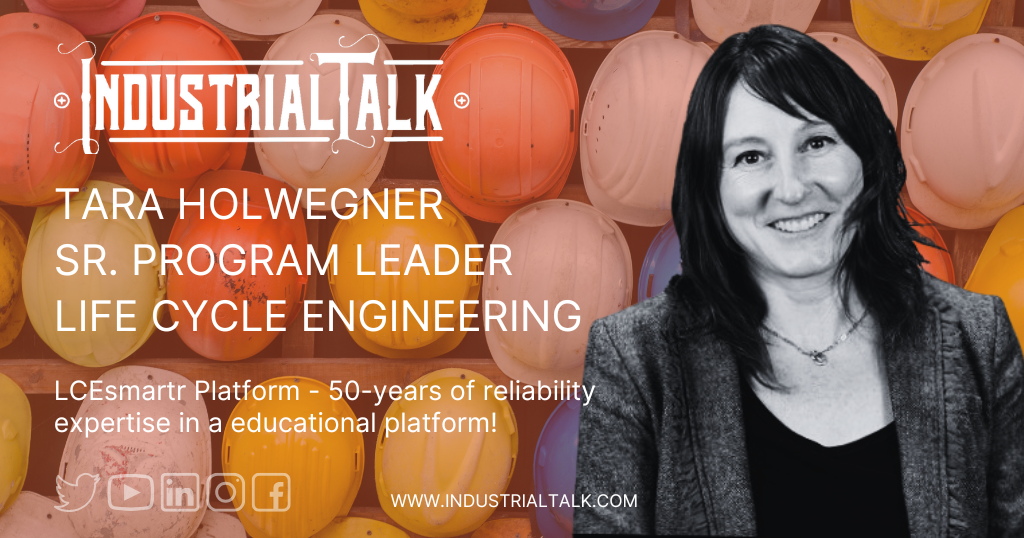
Scott MacKenzie announces a webinar on adapting to new China tariffs in manufacturing, featuring Eric Millinger and Jorge Filio. He then introduces Tara Holwegner to discuss the LCESmartr platform, which leverages 50 years of life cycle engineering knowledge into an educational platform. The platform includes an implementation guide, assessments, work stream packages, and e-learning courses. It has shown a 30% acceleration in reliability improvements and is available in multiple languages. Tara emphasizes the importance of employee engagement and continuous improvement, highlighting the platform's ability to support global operations and provide actionable insights for asset management and reliability.
Action Items
- [ ] Explore the LCESmartr platform by visiting lc.com or emailing info@lc.com to schedule an in-depth demo.
- [ ] Reach out to Tara on LinkedIn to further discuss how the LCESmartr platform can benefit your organization.
Outline
Webinar Announcement and Introduction
- Scott MacKenzie announces a webinar titled “Post Election Manufacturing Adapting to New China Tariffs in 2025” scheduled for Wednesday, November 20, 12 to 1 PM EST.
- The webinar will feature Eric Millinger and Jorge Filio discussing metal casting and fabrication.
- Scott emphasizes the importance of educating, collaborating, and innovating within the manufacturing market.
- The webinar will be available on demand for those who cannot attend live.
Introduction to Industrial Talk Podcast
- Scott thanks listeners for joining and praises industrial professionals for their daily problem-solving and innovation.
- Scott mentions a previous interview with Tara Holwegner at the SMRP event, which was canceled due to a hurricane.
- The upcoming interview will focus on Tara's platform, LCESmartr, which leverages 50 years of life cycle engineering experience.
Overview of LC Smarter Platform
- Scott introduces Tara Holwegner and sets the stage for discussing the LCESmartr platform.
- Tara expresses excitement about the platform and its potential to help listeners and viewers.
- Scott mentions that the interview will include slides and encourages listeners to watch the YouTube recording for a better experience.
- Tara reflects on the previous SMRP conference and looks forward to the upcoming event.
Challenges and Opportunities in Asset Management
- Tara discusses the challenges of workforce retirement and the need for effective onboarding and training of new workers.
- She highlights the importance of stable, reliable systems and documentation to mitigate operational risks.
- Tara mentions the significant capital investments in the industry and the need for strategic growth and expansion.
- She emphasizes the maturing discipline of asset management and the growing interest in digital manufacturing and Industry 4.0.
LC Smarter Platform and Its Benefits
- Tara explains that the LCESmartr platform is a playbook that encapsulates 50 years of life cycle engineering knowledge.
- The platform aims to address the challenges of workforce retirement and onboarding by providing a comprehensive toolkit for reliability and maintenance transformations.
- Tara mentions that the platform has been tested with early adopters and has shown significant benefits in accelerating reliability improvements by 30%.
- The platform includes best practices, tools, and resources to support organizations at various stages of maturity.
Implementation and Assessments
- Tara describes the implementation guide, which outlines the five stages of a transformation: visualize, plan, execute, sustain, and improve.
- The guide includes resources, tools, and guidance for establishing a business case, leading a transformation, and tracking progress.
- Tara highlights the importance of assessments in determining an organization's maturity level and tailoring improvement plans.
- The platform includes assessments for work management, reliability engineering, materials management, and capital delivery design.
Work Stream Packages and Practitioner Tools
- Tara introduces the work stream packages, which provide detailed best practices and tools for various disciplines.
- The platform includes practitioner tools such as critical spares analysis worksheets, asset criticality calculators, and FMEA/EMP tools.
- Tara emphasizes the importance of continuous improvement and the ability to add new resources and tools over time.
- The platform supports global operations with translations into multiple languages, including Japanese, German, French, and Italian.
E-Learning and Certification
- Tara discusses the e-learning courses available in the platform, which cover key topics in maintenance, reliability, and asset management.
- The courses are modularized, allowing organizations to level set their workforce and provide professional development opportunities.
- The platform also includes a reliability engineering certification program, which can be completed through the platform's coursework.
- Tara highlights the benefits of e-learning, including high engagement rates and the ability to onboard new employees efficiently.
Feedback and Support
- Tara explains the feedback loop and support mechanisms available to users of the LCESmartr platform.
- The platform includes a dedicated communications channel for customers to provide feedback and request support.
- Tara mentions the reporting dashboard for leaders to monitor user activity and assess progress.
- The platform supports multiple sites and groups, allowing organizations to measure and improve performance across different locations.
Benefits and Success Stories
- Tara shares success stories and the benefits of using the LCESmartr platform, including improved employee engagement and retention.
- The platform has shown significant savings in spare parts and reduced carrying costs.
- Tara emphasizes the importance of sustaining a culture of reliability and continuous improvement.
- The platform focuses on people, processes, and technology to create safe and efficient work environments.
Conclusion and Contact Information
- Tara encourages listeners to visit the LCE website or email for more information and to schedule a demo.
- Scott praises the LC Smarter platform and its potential to transform organizations in the field of asset management and reliability.
- Tara invites listeners to connect with her on LinkedIn and emphasizes the importance of collaboration and education in the industry.
- Scott wraps up the podcast, encouraging listeners to stay tuned for more conversations and to visit Industrial Talk for more resources and information.
If interested in being on the Industrial Talk show, simply contact us and let's have a quick conversation.
Finally, get your exclusive free access to the Industrial Academy and a series on “Why You Need To Podcast” for Greater Success in 2023. All links designed for keeping you current in this rapidly changing Industrial Market. Learn! Grow! Enjoy!
TARA HOLWEGNER'S CONTACT INFORMATION:
Personal LinkedIn: https://www.linkedin.com/in/taradenton/
Company LinkedIn: https://www.linkedin.com/company/life-cycle-engineering/posts/?feedView=all
Company Website: https://www.lce.com/
PODCAST VIDEO:
THE STRATEGIC REASON “WHY YOU NEED TO PODCAST”:
OTHER GREAT INDUSTRIAL RESOURCES:
NEOM: https://www.neom.com/en-us
Hexagon: https://hexagon.com/
Arduino: https://www.arduino.cc/
Fictiv: https://www.fictiv.com/
Hitachi Vantara: https://www.hitachivantara.com/en-us/home.html
Industrial Marketing Solutions: https://industrialtalk.com/industrial-marketing/
Industrial Academy: https://industrialtalk.com/industrial-academy/
Industrial Dojo: https://industrialtalk.com/industrial_dojo/
We the 15: https://www.wethe15.org/
YOUR INDUSTRIAL DIGITAL TOOLBOX:
LifterLMS: Get One Month Free for $1 – https://lifterlms.com/
Active Campaign: Active Campaign Link
Social Jukebox: https://www.socialjukebox.com/
Industrial Academy (One Month Free Access And One Free License For Future Industrial Leader):
Business Beatitude the Book
Do you desire a more joy-filled, deeply-enduring sense of accomplishment and success? Live your business the way you want to live with the BUSINESS BEATITUDES…The Bridge connecting sacrifice to success. YOU NEED THE BUSINESS BEATITUDES!
TAP INTO YOUR INDUSTRIAL SOUL, RESERVE YOUR COPY NOW! BE BOLD. BE BRAVE. DARE GREATLY AND CHANGE THE WORLD. GET THE BUSINESS BEATITUDES!
Reserve My Copy and My 25% Discount
Transcript
SUMMARY KEYWORDS
webinar announcement, manufacturing adaptation, China tariffs, metal casting, fabrication discussion, Industrial Talk, podcast episode, LCEsmartr, asset management, reliability engineering, work management, e-learning courses, employee engagement, business case, global operations
pting to new China tariffs in:Welcome to the Industrial Talk podcast with Scott. MacKenzie. Scott is a passionate industry professional dedicated to transferring cutting edge industry focused innovations and trends, while highlighting the men and women who keep the world moving. So put on your hard hat, grab your work boots, and let's go all right
once again. Thank you very much for joining you industrial professional, the number one industrial related podcast in the universe that celebrates you, as I point to you on the video, you are bold, brave. You dear, greatly. I say it all the time. You innovate. You solve problems each and every day. That's why you're the center of this story for Industrial Talk. That's why we celebrate you on this platform. She's been on the show before. I think we we interviewed her at SMRP, which is a great event, by the way, it got canceled by a hurricane, but that's okay. We're gonna be another one right around the corner. Her name is Tara all weekner, yeah, I probably miss mispronounce her last name, but I always go just by Tara. She we interviewed her at SMRP, and she never fails to deliver. We're gonna be talking about LC e smarter, their platform that takes 50 years of their experience at lce, that's life cycle engineering, and puts it all into an educational platform that you can't help but be better from it. All right, let's get cracking. Yep, she's amazing. She's got a lot of spunk and pepper. She's a lot of fun to talk to, and she's passionate about what she does. So that's, that's the interview coming up, and it's, it's, it's a bit lengthy, and we do show some slides. So if you want to go out and you want to see the slides, you want to see that presentation, go out to Industrial Talks, YouTube channel, easy Industrial Talk, and you go out there and you find it, and you get to take a journey with Tara on the LCEsmartr platform. It's a great platform. I was, I was dazzled by it. You know, one of the things that is always sort of amazing from this reliability, asset management perspective. It never stops. It's very collegial, it's very insightful, and it is all just focused on making businesses, manufacturers, industry, successful in how they manage their operations. It's in a in a nutshell, if I was in a nutshell. On a business side note, if you have a podcast, if you have technologies, sort of like what Tara is doing, if you have a podcast technology, and you want to get greater amplification, you want to get greater attention, Industrial Talk is like the Spotify, if I could say that, yeah, Spotify of industrial content, you need to put it out there. You need to just go out to Industrial Talk, connect with me, have a conversation, and let's make it easy, which is really important. Let's make it easy for these professionals out there that are making the world great, to get the content, get the information to to educate as they as needed to make them a success. That's the passion behind Industrial Talk, is to hopefully just help as much many people as possible and and if you want to just collaborate, because it's always about education, collaboration and innovation. From my perspective, you want to collaborate. Just go out to Industrial Talk. Find all of the great contributors to that you know site, and I guarantee you they want to have a conversation. So you need, you need. You need some serious Sherpas helping you along on this journey, all out on Industrial Talk. So. So don't come to me and say, I can't find anybody. They're there, right there. Industrial Talk.com, all right, let's get on with it. This is lce smarter. It's a platform that takes all of the knowledge that they've gained over 50 years, 50 years of asset management, maintenance, reliability, all of the stuff that's associated with it, put it into a system, and it's, it's user friendly, and it has, it's chock full of incredible information. So that's what we're going to be talking about. That's what we're going to be demonstrating. That's what Tara is going to be delivering. So let's get cracking with the conversation. Tara, how you doing? Welcome to Industrial Talk.
Thank you, Scott, thanks for having me. It's always
great to have you on Industrial Talk, listeners. She's been on Industrial Talk and she never, she never disappoints. I
never disappoint. I love that. Okay,
you pop with enthusiasm. Well,
I you know, I mean, you bring it out. You bring it out in us, Scott, but, but honestly, I do think we have, you know, I'm something really exciting to talk about today. So thank you for asking me to come on and talk about the LC smart platform, because I really do think that it has some resources, guidance and tools that are really going to help some of your listeners and viewers,
yeah, and if you you'll be able to listen to it on podcast, but it's not going to be the same. You might want to go out to YouTube and and find the recording it, because it's, we'll be sharing the screen, and we'll be looking at the solution time as we sort of take a test drive of it. Tars goes, she's going to make it happen and make it enjoyable and and dazzling.
I hope so. I hope so. But definitely, like you said, this, this session, this episode, is meant to be seen as well as heard. Yeah,
there you go. Take that. I'm going to steal it. Steal it.
Please do.
It's in my
so. You know, when you and I, you and I met at the SMRP conference last year, it was last year, right? Yeah, yeah. And, by the way, looking forward to this year, so I'll be listening right
around the corner. But what if it's going to be bigger, better, stronger, faster? What if it's gonna be, I
mean, it wasn't cheaper, so if it's the rest of them, then that, then that's good, but, but, no, you get great value out of that conference, but, but we talked about that was kind of the unveiling. It was a soft launch of the LC smart platform, and we got to talk a little bit about it. But it's been a year since then, and you know, so I thank you for inviting me here to tell folks more.
So it's just been out for a year. Yeah, it is. It's really,
it's really fresh. We had some very we had some early, trusted partners, customers that we said, hey, you know, we have, we have this new platform, and we want, we want you guys to help us see if it's everything that everything that we want it to be. So basically, we built the LC smart platform, and we call it our playbook, because it is literally everything that life cycle engineering has learned about implementing reliability and maintenance transformations over almost 50 years. So actually, in two years, like we were 48 years, in two years, we're going to be 50 years in the in this business. And we put it all. We put our entire body of knowledge, all of our resources, which I'm going to show you all online. And why, why do we do it? Yeah,
why? I mean,
well, yeah, it for a few reasons. First of all, it we have seen out there the challenges of a couple things with regarding our workforce. So knowledgeable workers, they're retiring, and they're taking the expertise with them. I think you call it, what did you call it? The Silver?
Silver Tsunami, yeah, I'm stealing that from somebody that he constantly because I stole it? Well, I've
never heard it before, so it's yours
now, silver.
It's amazing. But on the flip side of that, there's also the challenges of onboarding and training the new the new workforce in the most reliable, efficient, best practice way of doing their work, there's a lack, you know, of stable, reliable systems and documentation out there that opens up your operation to risk. You know, outside of the workforce, that's leaving. You know, there's assets that have been in operation for a long time that are a different phases of their. Life Cycle, maybe approaching end of life, and then huge boom in capital investments, you know, huge growth, which is the gray part of of what's happening, you know, in our in our industry today, lots of investments being made in expansions, lot of that's due to some, you know, favorable legislation. But also that the asset management, you know, as a discipline, is maturing, you know, in in our industry, and people are looking at more things, more strategically, and growth and expansion more more strategically, and investing in that. And then, you know, the industry four zero, digital manufacturing, digital transformation, and all, all this new technology and software that's out there, but people haven't been seeing the benefits or the results that they expected by implementing or introducing those new technologies and and with lifecycle engineering. I mean, that's been our whole genesis for being we we go into and we support manufacturing, um, industrial facilities, utilities, you name it, in developing those fundamentals, those asset management, maintenance and reliability best practices in the core key functions of work management, materials and reliability engineering. So storing reliability engineering and planning and scheduling and that that will enable you to transform faster, which is what we found with the playbook. It it literally accelerates a reliable improvement we've found by about 30%
also, also, okay. I hope you're going to cut this, because I'm going to have a big pause. It's
okay. It's not a problem. Hey, you're, you're rattling off a lot of stuff. I want to ask you a question about the faster. How did you come up with the fast? What does that mean if I, if I, I mean, it's, it's one thing to say faster, but I, I'm thinking in my head, I have a I have an organization, and that organization needs to be sort of change management around a more reliability type of culture, right? And I, I have the right leadership in place. They're all supportive of it. We're going to deploy it. And you're saying that this playbook, if I, if I head down that road, this playbook, also helps support that transition. What is yes, yes.
And by the way, you mentioned something that's half the battle, which is getting the leadership support that you need to have sustain change, right? Because this, this doesn't happen overnight. But I do want to talk about about the acceleration piece of the Yeah, because I
really 30% that's you nailed the number there. And I'm going, how do you check? How about
:was gonna let the math slip a little bit
well, but, but that 30? But that 30 was what we have found in terms of the time that we've saved in getting people to adopt the the new processes and getting them to become proficient. We've been able to speed that by the tools, the resources and the reporting that's in LC. That's an LCEsmartr and our consultants have had to spend less time because we've right less time on site, you know, and in more coaching role, because we have, we've put so much of the effort into. The system itself. So
you really, from a business perspective, you can approach another, let's, let's use manufacturing as an example. You can approach a manufacturer where they're at, both financially and where they're at in a reliability maturity point of view, too. So for example, if I'm a new manufacturer and i i All of a sudden say, Yes, I want to be able to transform my business, but I don't have the resources, the financial resources, I can still use this playbook in a way that benefits me and gives me the the information that I need, versus, let's say I'm a mature manufacturer I want to bolster up. I have the balance sheet to be able to sort of help financially and bring a team on board, and you can, you can meet me anywhere I'm at in that that
exactly you said it. You said it, exactly you said it better than I could. So the the smarter, the smarter platform is exactly that you you find where you are. And we actually have assessments that, if you're not sure you know where you fall in a maturity continuum, we have self assessment. So you can actually track those assessments over time to get those resources that are going to support you where you are. And even if you're proactive, what we call a proactive operations or an excellent operation, there's always still room to continuously improve and get even better, to be able to, you know, meet customer demand, or in this in the and the example of the capital expansions to start off with those best practices. So you're a Greenfield and you are starting off with everything already your reliable operations are designed in right? So that's even a better
let's say I'm an organization, and we're going to get into your solution, we're going to your solution, we're going to share, and we're going to be able to take a little test drive and kick the tires a little bit. But let's say I'm a organization, and I make the decision that I truly want to be that that organization that is focused on asset management, really good asset management, good reliability. And I would imagine I'm inefficient. Then all of a sudden, I become efficient, you're saying, and I see this. I see this graph in my head. I can't show it to you, but it's in my head. So I make big leaps of efficiency in the beginning, and then I then I'm fighting for the smaller, but you're saying that there's always room for more and greater efficiencies as time goes on
right. And also to to adopt, you know, the innovations that that your workforce. You know who's on the floor, who has good ideas you know, can bring to the table, but also all of the that's the time. That's the time to look at advanced predictive analytics, that's the time to look at performance monitoring, that's the time to take it to, you know, the next level in terms of automation and digitalization, but to have those foundations in place is the only way that you're going to be as successful.
Yeah, and that's a whole nother conversation. I it is, I think, I think a silver bullet is, like, all of a sudden, yes, I want to digitize my business. I want to be able to venture into industry 4.0, but I don't have the blocking and tackling, the basics in place correct to ensure that I succeed. And I think that is where people, well, stumble and stumble. Yeah,
it does. And that doesn't do well. That doesn't do well for business case, for investment. So, so that is, you know, we've talked about a couple of different we've talked about, I guess what, I guess what they call in product, use cases, right? We've for for the playbook. I
interviewed the guy that came up with the term use case, the founder, i did i i Give
me a touch like, oh, person, yeah, here's
how he came up with the term use case. He was, it was back in the early 60s, early 60s, like 60. And he just said, Well, we've got a we got this technology. We just need some sort of a use case, a user case. And then it just shrunk to use case there. That's it. He needed to have any any desire to didn't think that was going to blow up. He just said, we just need to use
your case. There it is. Now, now, I mean, it's just part
of the part of the lexicon.
But yeah, so we talked about a couple, right? We talked about, you know, the the perhaps fledgling, you know, or or early stages of No. Knowing that, you know you want to pursue some kind of change, some kind of reliability improvement, or you know are aspiring to that, you know, this could be the platform and toolkit for you that the organization, the large scale organization that sees the competitive advantage and the business, you know, burning platform we have to improve now, you know. And this is, you know, the toolkit for you. You know what, what you're talking about about, you know, hey, we want, we want all this cool technology. It's the answer, no, we have the fundamental blocking and tackling already defined for you. So just plug and play the smarter playbook, and then plug and play the technology on top. And now see where you you know you can get with actually pulling data out of your CMMS. All
right, let's, let's start kicking the tires here. Let's Okay, show us. Show us what you got. Okay, I
will, and I also want to, I also want to share that this system has been translated already. We're on our fourth language. We're going to our fifth language. So the next use case is global operations that want everyone to speak the same or have the same terminology, if you will, around reliability and asset management.
I agree with you 100% on that. So the five languages, I'm sure Spanish,
actually not yet.
Yeah. So make a recommendation. Yes,
I agree. I agree. So, hey, customers, if you're out there listening, we've, actually, we've, we've translated the the system according to what, what our customer needs base is, and believe it or not, Japanese and German, yes, sir, and French and Italian. So really
talk about a low hanging fruit. Spanish
is next up from for, you know, North and South America, yes, but you know, but French is going to help the Canadian manufacturers as well, and industrial operations as well. So, so this is the home screen of the LCEsmartr playbook. When our when an enterprise purchases it, we do brand it so it looks like your system. You know, it is your playbook. It is not lifecycle, engine engineering playbook. But I just want to kind of step through the different the different sections of the tool. First of all, we have an implementation guide. And the implementation guide is going to take you through what we call the five stages of a transformation. They range from visualize to to all the way to implementation and sustainability. So if you have this implementation guide, it gives you resources, tools and guidance, really a step by step instruction manual on how to lead and support a reliability transformation from establishing your Why do you really need to change getting leadership involved business case. We actually have a business case tool in the playbook all the way through working through your project plan with your focus teams, and then tracking your programs progress, as well as sustaining that change through regular reassessments and tracking your performance, we tell you, you know, how long, how long are we going to be investing, you know, time in this change and so all of those project management and change management tools, look here. We have a case for change presentation you can send to leadership and an online calculator. You can work with your with your finances, right
off right off the bat. Right off the bat, have a gotcha? Yeah, right off the bat, you're if I was a reliability engineer in my organization and I'm trying to gain traction where I'm trying to get support, I would, can I just get this and have this as a resource? Because, man, you're hitting on some really important topics. Well,
yes, and again, you know, like I said, it's what we've learned about implementing these best practices for over 50 years, and we've put it all in a cloud based online system. Them. Look, you have all of your change management plans here, your risk plan, your resistance management plan. How are you going to be training your employees? So that is the implementation guide. But I will say, Scott, that's not all we also have. I'm going to go into assessments. So how do you know where we were talking earlier about your maturity and meeting you where you're at? Yeah. Well, we have for our our core, as I described in the beginning, our our core areas, um, of foundation, our reliability engineering, materials management, work management, but we want this playbook and this platform to support the entire life cycle of your assets and your systems. So we just added, recently capital delivery design for reliability and shutdowns, turnarounds, all of our I'm going to show you in a minute, but all of our work streams, as we call them come complete with an assessment that is tied to what we consider our best practice, process flow. So work management has seven I'll show you more about that ranges from work identification to work execution and work close out. And you can see yourself in these descriptions, in these assessment descriptions, and and you'll get an overall score for how are you reactive? Are you early emerging? Are you already in proactive zone? And you can tailor your improvement plan to exactly you know where you are on that maturity. Major. What
if I get into that and I have this assessment, and I'm I'm deemed reactive? Are there recommendations? Because you don't want to be reactive. I don't want to be reactive, I want to be proactive. I want to be insightful, and all of that good stuff. Do you Do you provide recommendations on saying you're reactive? Yes, want to consider some other options here well,
and we show you too. We show you what, what, what proactive, what you know is best practice looks like, right? So the next area I'm going to show you is what we call our work stream packages. So if you want to go, we'll look at reliability engineering this time, because that was work management. And if you go into you can see, Okay, where am I now? What? What should I go to next? Because you're not going to move directly from reactive into proactive. It just you have to, but you have to move through the different areas of maturity to get to that level. Yes, what we can do is, through the LC smart platform, we can help you see what that looks like and develop a plan. But we also, whenever any enterprise purchases a subscription to the playbook, they also have subject matter expert support, and that's going to be, that's, that's going to be really critical as part of your implementation to get it right. And that can vary what sort of support you may decide, and you may be able to get the support, you know, for full scale transformation across all three work streams, or you may have to prove that one works. And we'll be able to help you. You know, we'll be able to help you get there.
I think the title of that particular workflow right there, that's mega level view. It is not just any level view. That's Mega.
It's your Mega level view. So these, these are all of the components. It's what we consider a best practice reliability engineering discipline. And then if you go into the different the different processes, including that work stream, we provide a single point lesson, yeah, we provide a workflow diagram which is customizable, and that's what our subject matter experts, you know, a lot of the times, help support our our customers with we also have what we call our step definitions, and we have coaching cards, which is another change management tool. This is like a GEMBA walk support tool, where you as a manager or as a supervisor can take a checklist, a digital checklist. And see, you know, how are these new processes working? Are there any changes, adjustments that we need to make? How is the data this? Is this, for example, is with asset data collection. So you know. How is that reflected in the in the oops,
I whoops, go back. Let me go back. Okay. How long did this, this effort? It's been in sort of production for a year. How long did it? I mean, this seems voluminous in its resource capabilities and. Brain. How long did it take for you guys to pull this together? This is amazing. Oh,
well, thank you. And I just want to let you know that's not all, um, if we go to, we'll go to, um, we'll go again to, we'll, we'll keep playing in the reliability. And, yeah, please area. So in addition to all of the standard work and engineering processes and tools, we also have some practitioner tools that are specific to that discipline. So in the reliability engineering work stream, you're going to see critical spares analysis worksheets. You're going to see asset criticality calculators. You're going to see your FMEA EMP tools, which our own consultants use. You'll have some advanced tools, like a viable calculator, if you want to play around with that. But the system also supports the growth and maturity of your program. So we also have additional resources, like job descriptions, and some of our customers have really gotten a lot of benefit from just being able to take the job descriptions that we provide in the system and put them out there to hire some really qualified candidates. And we're constantly adding to the playbook in terms of resources. So over here, in the Additional Resources tool, you might see a brand new resource pop up every quarter. We have a newsletter where we keep our where we keep all of our our enterprise customers, aware of what we're adding to the system. Another exciting area, and yes, it did take several years, and it's constantly evolving. It
has to, you had to make the decision to say, Okay, we've got a lot of information. Let's, let's get it into production, and then let's do the SAS model and update it as we continue to go forward. So it just, oh, I'm impressed. I really am. Good job.
Well, thank you. So it did take our, I mean, our consulting firm, you know, worked very, very judiciously, to come up with what we call our gold standards. I I'm sure you were lifecycle engineering has a lifecycle Institute which has been around now for almost 20 years. And so not only have we been in the consulting arena, which is the larger part of our business, but we've also been in the education for our industry. And so by developing what we call these gold standards and training people on the best practices, we realized that we had this entire body of knowledge that could be curated in such a way that it could be consumed as part of the implementation, and it wouldn't just be our secret anymore that we could share it at a larger scale, Yep, and also let more of our consultants impact more operations, but the next, one of our most exciting, I think, areas of the playbook, and one that our customers are very committed to, is the e learning so here you see three of our E learning courses. We have six, and we have two more on in development for capital and design for liability. So we had these are transformations of our three day in person instruction into online courses. So we're talking about six to eight hours of E learning. Now, the beauty of this is that the way that we have designed these courses is that they're highly modularized, so we don't expect the full organization to take all six to eight hours. Actually, some of our customers do the because it they believe that every you know maintenance and reliability best practices is how we run our business, and you need to understand, you know, how we how we work and how we live, but you can, you can take modules or lessons of these courses and level set the entire organization. So you have a knowledge baseline around enterprise wide, a knowledge baseline around maintenance, reliability and asset management, best practices. Another, another neat tidbit is we have moved our reliability engineering certification online, and we have four universities that that partner with us for this certification, and you can actually get the coursework done for the certification in this. Order playbook. There's still some work outside of that that you have to do, but, but you can, you can get a lot of the the learning done. This is huge for our our clients that have stayed with us over time, because they now they have a system where they can onboard new people or refresher training or professional development and skill building up skilling and re skilling all through the playbook.
How does it's great, no doubt about it. I'm dazzled by it, overwhelmed. How do you speaking of being overwhelmed drinking from a fire hose,
that's a lot.
How do you help organizations to sort of take small bites and take this massive store of information and then methodically go through it in such a way that benefits them the most. That's one question. And then the second question is, what if I go through this process and then I have a feedback is there a feedback loop that I can go back to lifecycle engineering and say, Hey, thought I just feed this back. So
absolutely, well, the the second one might be easier and quicker to to answer. So we do? We do have a team, like I said, when, when you purchase an enterprise version of the of the playbook, you're going to have some subject matter expert support and point of contact so that that individual can help you along the way. And if you find that you need more help, then, of course, that can always be arranged. We also have a dedicated communications channel for all of our customers. We We want every customer of life cycle engineering, but of course, of the playbook to be a success story, so we are constantly staying in touch with the reliability leaders and the point of contact and helping them understand, how can they make the most out of their LC, smarter playbook, and where else could they use, you know, some support or some guidance if it's currently not in the playbook. The way that we grow is to get feedback from our customers and clients on what do they need, what's what may be missing, or what can we help you with that we can expand, you know, the playbook on you talked about feedback. So we do have a reporting dashboard for the leaders of the playbook, so in this way, they can see, okay, what is my login activity? You know, who's using the playbook. How often are they logging in? You know, if, potentially, if there are some improvement efforts going on at a particular site, that's the other thing you can we can organize the smarter platform in such a way that you can have multiple sites, multiple groups. We have one customer that has over 600 users and over 30 sites, and we are measuring all of the activity that goes on the playbook, and they can easily filter and get the reports that they need on what's happening at different sites. So this is where you can monitor your training activity that happens in LCEsmartr. We also measure, you know, what kind of resources are people into interacting with? And then, with regards to the feedback loop and the work stream assessments, and being able to measure the assessments over time is huge in terms of being able to, you know, see, okay, I was doing great, but maybe I've slipped, you know, and where have I Where? Where are my areas of opportunity, you know, or what site may be doing some excellent things, and we want to be, you know, using that, that site or or the efforts that are ongoing there as an example.
But yes, and I sorry, I this is just sort of popped into my head. Can you translate this into some benefits? The real hard dollar benefits, as I continue to train, let's say I bring this particular tool into my organization. It is, it is the access, you know, enterprise wide, I'm tracking and monitoring all of the learning. Are you seeing? It also translate into why we are benefiting from this? Why Asset Management relief? Ability that is is important,
right? So I would just go ahead and stop sharing, if that's okay. We could just just talk. But Hi, so we, we have, we again, you know, especially for the organizations that go through a full transformation with us. We can get down to the nitty gritty of you know how since we have made these improvements, you know, what has been the impact to your OEE? What has been the impact just to your availability? Because we do have a lot of customers that come to us, they they need, they're they are not going to expand, or they've already made some plans to expand. And we say, well, wait a second. You're only you've got so much availability. You've got a whole you've got a whole other factory in there that you don't even know about. You don't need to, you don't need to build a new facility. You need to get the most out of what you got now and and you can make that so we do have, you know, those business cases that we go in, and we can make those specific monetary returns. What we have found, though, in terms of what the training specifically has done, and in LCEsmartr has done we get back from our evaluations. So the employee engagement, and that's a huge thing about keeping people in retention, is giving people the opportunity to grow and to develop, and the employee engagement rates in terms of I can apply what I've learned. The training was really valuable. Every all of our E Learning has action plans, and it's insane to me, the evaluation results that we've gotten from this e learning, 90% of people has said, I believe I can apply what I use. We're at like 92 depending on, you know, we have, we do have quite a few customers, you know, now who are utilizing the playbook, and we're just seeing off the charts things that I don't see in even in public, in person, classes, in terms of results, of how people feel that the learning is valuable and that they can use the resources and use what they learned. Wow, and then and then you will see, you know, with in terms of the efficiencies that you know, in terms of the efficiencies that you can see through the improved, you know, work effectiveness that comes with savings. You know, you can also when we go into the storeroom and we're getting rid of, you know, spare parts for assets that you may not even have in your organization anymore, you know you're lowering your carrying cost. You're, you're only keeping the critical spares that you need, and you've got a plan to save on, you know, to save on whatever lead time or shipping that you may have, you know. So there are, there are definitive savings, you know, there as well.
That's cool. I'm this is really impressive, empowering, right? It really is, well,
and that's sort of, it's within that's, that was life cycle. Is life cycle engineering. You know, see, this
is why the rub always happens with reliability. Sometimes it's, it's, how do we sustain it? How do we sustain that culture? Keep it moving forward. Keep on improving upon it. Keep extracting greater value out of that very important asset. It's, it's always dealing with people, and how do you sustain it? This seems like a tool that really promotes that, sustaining the that, that effort. It's important stuff. I like it. We
always say we focus on people process, and then, you know, technology, yeah, and and with that, you know, we can enable everyone to come to a safe environment, to work an efficient environment, to work where they can be proud of the work that they do and proud of what what they're producing. You know, for all of us, whether it be energy, whether it be food, you know, whether it be my favorite beverage or a needed medicine, you know, that's, that's what we're here to, to facilitate.
If I'm if, if somebody's listening and they're saying, hey, my gosh, that is just, that's the cat's meow. That's, that's the best thing since life spread. I'm running out of words to say anyway. Ah, if somebody says that, what is the best way to be able to start this conversation?
Oh, well, all they need to do is they can go to lc.com they can email info@lc.com they can come see us at SMRP. But we are, we are available to do an in depth demo. We're available to help you build business case for your leadership. We're just here to talk about what's going on and how, how we can help. Say, tar,
you were you were great. Oh,
thank you for the opportunity to show you. Know, Like that. Like I said, it's a we actually call it a revolution, and reliability excellence 15.
I think I like it. I will, I definitely will adopt that. Because this is outside of the podcast, which, if you're listening to the podcast, gotta see the video. This is a great tool for you to consider if you're in the world of asset management reliability, and you're one of those engineers that are looking for an a never ending source of insights and education. This this smarter platform, this playbook is weight. Love it. I love it. Well done. Well done to LC, and you Good job. Thank
you, Scott, and Thanks for Thanks for the time today. Love it. Listeners and watchers, yes, please just come to lc.com and you know, just shoot us. Shoot us a note. Find me on LinkedIn. We're here all right.
Listeners, we're gonna wrap it up on the other side. We're gonna have all the contact information for Tara out on Industrial Talk. So stay tuned. We will be right back.
You're listening to the Industrial Talk Podcast Network.
That's Tara. She's quite chirpy. She's She's very passionate. And you know, Team LC very passionate about your success in the world of asset management, reliability, and it is. It's a it's a game of education. What is the latest and greatest you have all this innovation that's happening out there in industry right now? How do you keep current? You need a team like LC e to be able to be a part of your partner and your group and your your team, to be able to keep current with all of the things that are happening out there on in industry. Yeah, big time. All right, again. One, you have a podcast, an industrial podcast, you put it out on Industrial Talk. Two, if you have technology that you truly want to amplify. You put it out on Industrial Talk. It's simple or easy peasy. You want to be on a podcast. You give me a call, go out to Industrial Talk, and you will find me there. All right. Be bold. Be brave. Get greatly. Hang out with Tara change the world. We're going to have another great conversation shortly. So stay tuned. You.