Mr. Colin Duncan with SEAM Group Talks About The Performance Triad
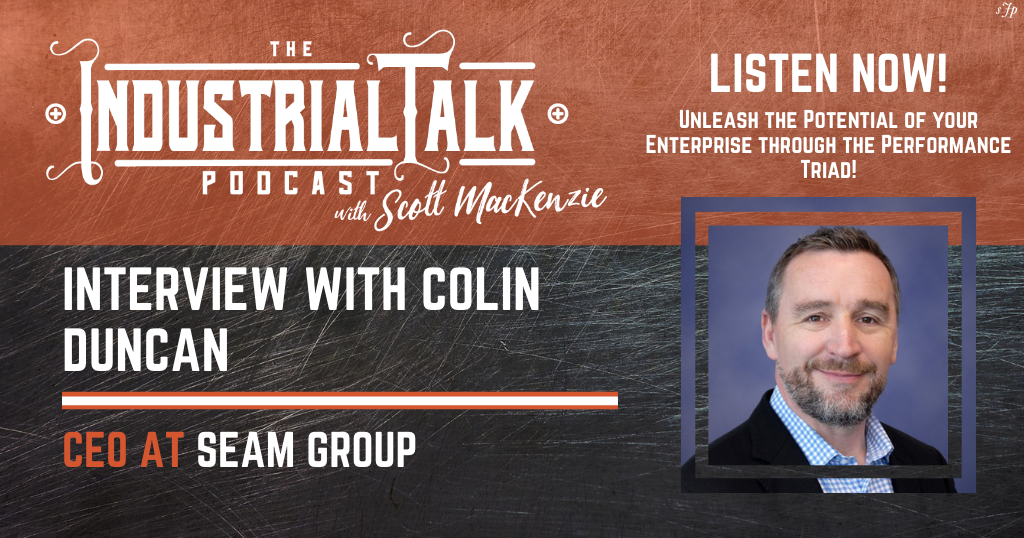
In this week's Industrial Talk Podcast we're talking to Colin Duncan, CEO at The SEAM Group about “Unleashing the Potential of Your Organization through the Performance Triad of Safety, Reliability and Maintenance”. Get the answers to your “Performance Triad” questions along with Colin's unique insight on the “How” on this Industrial Talk interview!
You can find out more about Colin and the wonderful team at the SEAM Group on Unleashing the Potential of Your Organization by the links below. Finally, get your exclusive free access to the Industrial Academy and a series on “Why You Need To Podcast” for Greater Success in 2020. All links designed for keeping you current in this rapidly changing Industrial Market. Learn! Grow! Enjoy!
COLIN DUNCAN'S CONTACT INFORMATION:
Personal LinkedIn: https://www.linkedin.com/in/davidred/
Company LinkedIn: https://www.linkedin.com/company/national-oilwell-varco/
Company Website: https://www.nov.com/
PODCAST VIDEO:
THE STRATEGIC REASON “WHY YOU NEED TO PODCAST”:
OTHER GREAT INDUSTRIAL RESOURCES:
CAP Logistics: https://www.caplogistics.com/
Hitachi Vantara: https://www.hitachivantara.com/en-us/home.html
Industrial Marketing Solutions: https://industrialtalk.com/industrial-marketing/
Industrial Academy: https://industrialtalk.com/industrial-academy/
Industrial Dojo: https://industrialtalk.com/industrial_dojo/
Safety With Purpose Podcast: https://safetywithpurpose.com/
YOUR INDUSTRIAL DIGITAL TOOLBOX:
LifterLMS: Get One Month Free for $1 – https://lifterlms.com/
Active Campaign: Active Campaign Link
BombBomb: BombBomb Link
Social Jukebox: https://www.socialjukebox.com/
Industrial Academy (One Month Free Access And One Free License For Future Industrial Leader):
Business Beatitude the Book
Do you desire a more joy-filled, deeply-enduring sense of accomplishment and success? Live your business the way you want to live with the BUSINESS BEATITUDES…The Bridge connecting sacrifice to success. YOU NEED THE BUSINESS BEATITUDES!
TAP INTO YOUR INDUSTRIAL SOUL, RESERVE YOUR COPY NOW! BE BOLD. BE BRAVE. DARE GREATLY AND CHANGE THE WORLD. GET THE BUSINESS BEATITUDES!
Reserve My Copy and My 25% Discount
PODCAST TRANSCRIPT: