Klaus Blache with University of Tennessee
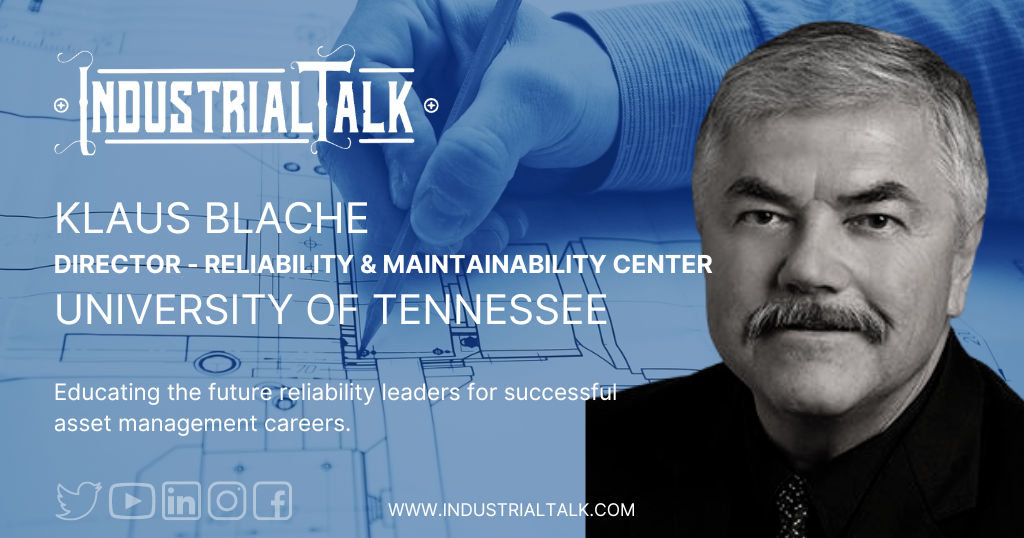
Industrial Talk is onsite at the 30th Annual SMRP conference and speaking with Klaus Blache, Director – Reliability and Maintainability Center at the University of Tennessee about “Educating the Asset Management Leaders of the Future”. Get the answers to your “Reliability Education” questions along with Klaus' incredible insight on the “How” on this Industrial Talk interview!
Finally, get your exclusive free access to the Industrial Academy and a series on “Why You Need To Podcast” for Greater Success in 2023. All links designed for keeping you current in this rapidly changing Industrial Market. Learn! Grow! Enjoy!
KLAUS BLACHE'S CONTACT INFORMATION:
Personal LinkedIn: https://www.linkedin.com/in/klausblache/
Company Website: https://rmc.utk.edu/
PODCAST VIDEO:
THE STRATEGIC REASON “WHY YOU NEED TO PODCAST”:
OTHER GREAT INDUSTRIAL RESOURCES:
NEOM: https://www.neom.com/en-us
AI Dash: https://www.aidash.com/
Hitachi Vantara: https://www.hitachivantara.com/en-us/home.html
Industrial Marketing Solutions: https://industrialtalk.com/industrial-marketing/
Industrial Academy: https://industrialtalk.com/industrial-academy/
Industrial Dojo: https://industrialtalk.com/industrial_dojo/
We the 15: https://www.wethe15.org/
YOUR INDUSTRIAL DIGITAL TOOLBOX:
LifterLMS: Get One Month Free for $1 – https://lifterlms.com/
Active Campaign: Active Campaign Link
Social Jukebox: https://www.socialjukebox.com/
Industrial Academy (One Month Free Access And One Free License For Future Industrial Leader):
Business Beatitude the Book
Do you desire a more joy-filled, deeply-enduring sense of accomplishment and success? Live your business the way you want to live with the BUSINESS BEATITUDES…The Bridge connecting sacrifice to success. YOU NEED THE BUSINESS BEATITUDES!
TAP INTO YOUR INDUSTRIAL SOUL, RESERVE YOUR COPY NOW! BE BOLD. BE BRAVE. DARE GREATLY AND CHANGE THE WORLD. GET THE BUSINESS BEATITUDES!
Reserve My Copy and My 25% Discount
Transcript
Welcome to the Industrial Talk podcast with Scott Mackenzie. Scott is a passionate industry professional dedicated to transferring cutting edge industry focused innovations and trends while highlighting the men and women who keep the world moving. So put on your hard hat, grab your work boots, and let's get around once
again, thank you very much for joining Industrial Talk a platform that is dedicated to industry professionals all around the world because you are bold, yes, brave. Yes. You dare greatly you solve problems you collaborate. You're making my life and the world a better place. How about that for a celebration? We are on site once again, at the 30th annual SMRP conference here in Raleigh, North Carolina. It is well attended. If you are in the manufacturing, if you are in the industry, if you are in maintenance, if you're in reliability, this is a thing. This is the conference for you. All right. He's a legend. He's been on the podcast a number of times, he does not disappoint. Klaus, his name, University of Tennessee.
They just won a football game to iron
scuttlebutt has. I'm excited about this conversation. Seems like our paths crossed quite a bit at various things when it's all cool. It's always great to see you.
Enjoy being in all places.
is a good time. It's exciting time. I mean, more than ever. I mean, I think you're right in the middle of it.
It's good to get out again, too. You know, it does.
Yeah, well, when was the last time we saw each other? It was I think it was manufacturing,
or COVID? Yeah.
That's right. I wanted to interview them. But you were too busy. You were you were being Klaus, most definitely. All right. I know that we need to level set real quick on who you are. I know who you are other listeners down. So let's just sort of give us a little background on the class. And then we're gonna talk a little bit about what's happening at the University of Tennessee and and from a reliability perspective and how education is important. Talk to us.
Sure, great. Well, currently, I'm at the University of Tennessee director, reliability, maintainability. Center, and Professor there, but although I do tie in the students, and we do various academic things, and majority of my time is really involved with helping industry, really implementation, everything from the technical stuff to changing cultures and law, but it would be professional development, training, but also everything from assessments and what are roadmaps to get better at etc, data mining all the things and the technologies around that. And then I didn't know the 14 years, I was gonna hurt to believe in itself. Oh, I
say that again.
I've been there 14 years, is it really hard to believe it is? But no, I've always had great. I've always been, I retired for 32 hours, my wife kept track. And then I left the job as a manufacturing engineering director at Cadillac of General Motors at the time. And you know, we build plans, random and so on. And then, in the middle of my career, I had North America responsibility for manufacturing liability and maintenance. And that's really I grew my love for this kind of stuff. And so I'm glad that you know, corporate jobs and industrial engineering. So now I have a global benchmarking, which I still do after 30 years. I was one of the 810 companies, people that was involved in putting SRP together and in the early days. And so that's, you know, that's why I have a lot of ties back into here. I was chairman for a couple years around year five, six, and then kind of lose track of when and and then I went to the University of Tennessee because even those a few other schools now getting into a war. It's the only university when I started in North America that had both undergraduate and graduate program, we tied it we tied into our and our, and so I targeted that specifically, I didn't just kind of kind of land there. And so they've had a program probably about three years after SMRP. So it's actually our 27th conference.
Wow, that's pretty cool. Yeah. So if I had a nickel of every time somebody cynical, I know what they look like. If I had a nickel for everybody, every time somebody says hey, we're having we're having resources challenged where we're having difficulty finding people and and I don't know chicken egg, I don't know. But you're in the thick of it. You're where you're where you're focused on education, you're focused on building that future with with young professionals desire Ready to get into this? You know, World of reliability? What have you seen? What are how is the University of Tennessee help facilitating that? Or minimizing the pain of what's going on out there? Well, I
think those are a couple of things is I mean, we obviously have our academic minor and for the students coming out, so they get some of the some of that academic experience. And then we look at it every three, four or five years during that timeframe, every every window like that, we put students in half the United States in summer internships, so they're also getting the practical experience in companies,
you're putting them in and on the floor, or wherever, yeah, they're doing
working in academia, we spend:How do you how do you, you know, how do you keep current? Because one thing that's obvious, and apparent out here is that there's a velocity that exists. And there's the the traditional, you know, reliability, you know, work. And then you got all this innovation in this technology out here. How does your organization sort of begin to marry the two and keep moving and keeping that sort of nimble mindset?
do a lot of benchmarking with:That's, that's interesting. So how do we how do we change that? Well,
part of it again, is the cultural thing. Which is, you know, it's not it's not That's
not easy. That's not a light switch. That's for doggone Sure, right. Yeah, you
don't change that over
over? No. But But, but, but there is, there's got to be a plan to do that. Yeah, we've got to be competitive with
yada, and then even with the technologies, the technologies are gonna come, what I see the integrity of the data is not there to support the technologies, some stuff, you can pull off with a condition monitoring, but there's still a lot of many manual input and interpretation. And so some companies have lots of data, but it's not that good. Other Other companies have really good data, but data missing. And so what good it is, is that if you have technologies that are plug and play, if you don't trust your data, to make the tough decisions, and so that's an issue right now, still to that. So so whenever I see projects or things, even a few that I'm involved with, I won't mention the names. But But the biggest issue is 80% of the effort is cleansing the data.
You know, you bring up a good point, and every time that I went into an implementation of some sort, the biggest and nastiest conversation was around data. Bad data over a period of time it it accumulates, I and again, I don't know the solution to scrubbing that data. But so with that said, so with all of this data stuff, it's still we're not in a position we we dream about all of this wonderful innovation and technology. But we still have a lot of work to do just to get it to a point where it's sort of drivable.
Absolutely was the two things that can help with the culture. One is, is I see people, rather than doing just Kaizen or continuous improvement events. Yeah, they learned how they need to learn how to coach better, because what you really want is everybody in the plant floor to be a problem. So it's somewhat like a potential improvement event. But you might have this kind of like a lean sensei type of demo concept. Where you going out there? And you're never given the answers in this kind of simplistic version of that you never given the answers. Rather than saying, I've got ideas going to work, I might say, you know, listening to you talk about what you're going to do, I'm not sure what you're going to implement is going to give you the results that you want. Have you thought about some other things, but I will never give you the answer. But rather than just giving you an answer, even though I think I know it, I'm gonna have to come out five or six times, they have the patience to do that. But when they gets done, you become a problem solver. And now, and that's coaching, so that's part of that. And so in a real lean sensing environment, you're always getting coached by somebody, and you're always coaching somebody. But now you might have developed two or three more problem solvers on the floor by taking the time to go out there four or five times rather than saying, here it is, go implement it. And then eventually, they'll coach somebody, and they'll coach somebody, after five rounds, you got to 300 Problem Solvers versus just going out and doing a Kaizen event with five or 10. Engineers. And now you have a whole planet full of problem solvers. So that's part of it is shot just
the other day doesn't happen overnight. Oh, no.
The other thing I see is just the lack of resources. And so most companies under they, let's say, you've gotten to the robust decision that we're not going to find the resources. And so what do we do internally? And so it gets back to how do we get the operators more involved, which is the really the last step of autonomous maintenance, the owner operator, the latest buzzword last five years, but operator driven reliability, but but it's really, it's all the same thing. Yeah, I agree. And so some people that are putting together really good programs, that are even teaching the operators basic electrical skills, and they love it, not everybody, but a lot of them love it, because now they can do some basic electrical at home, you know, safely and all that and they get certified in that, and some that have the aptitude go far enough, and the operators become skilled trades. And so, so people are training their own to get there, and everybody's piling that some are farther along, and so on.
That is, I like that. And so what I hear, and correct me if I'm wrong, if I have an organization, and some challenges with resources, not getting the right ones, whatever it might be, but I do have skilled individuals that are still a part of my organization. It sounds like I should be motivated in expanding their their capability capabilities, or
people that have the potential to have skills, but never gets given the opportunities, right.
And then be able to, and that would seem to me that that individual would have greater desire to be there. Be committed to the organization, there's as opposed to just leaving or whatever, because you're making that individual, such a valuable component to the organization and, and expanding there. How, with your organization with the University of Tennessee, how do you how do you do that for your students? How do you I mean, it's, it's not, it's one thing to say, hey, here's a pop, and this is what you do. And this is what it's all about, blah, blah, blah. It's another thing to try to inculcate the dynamics of the industry that they're going into, and that they're passionate about?
Yeah, the hardest thing I think, for students to learn always is 80% of the decisions you have to make don't have an answer you can calculate. Yeah, see? Yeah. And so we try to teach some of those skills between the internships in the center and so on. Because on the test in school, it's usually you calculate an answer. And it's ABCD, or a number is observed,
right, wrong. Yeah. I don't know how you do it. I don't know how you do. But it's a neat, it's needed I find, especially today, and maybe it's because of the, the pandemic, that there I just sense a better a greater focus into the benefits of asset management, proper maintenance, doing what we need to do utilizing the tools out there and doing it because I think the pandemic, you know, highlighted the fact that, oh, this is not good for me. And then I need to collaborate and have conversation to talk about it. Do you find that sort of trend happening?
Oh, yeah. I think a lot of the stuff happening even on a plan floor, is I think we have to get a lot better at meeting the people where they're at. Yeah, logically, like that time when how fast are we get into the new technology? I mean, I labeled that usually zone of uncertainty. I think we're in the middle of one right now. Oh, it's, again, again, how fast do I step into the new stuff? When 90% of my workforce is still trying to understand the basic technology. It's
so true. It's and I agree with you 100% It's like, I got it, but I'm just trying to lube this bearing. That's all I'm trying and trying to do it right. Yeah, because I gotta lube it. You know. I don't want Don't put too much in it. I don't want to I want to put the right in. That's where they're at. It's it's pretty basic. And you're absolutely correct. And it's important. So I just think you're right in the heart of it. And are you finding greater interest from a from people saying, hey, I want to be a part of this?
plant that have been in there:and see when I was a lineman, I started as a ground man, right. And I'm going to be a transmission lineman. And I was going through my apprenticeship program, it was on site, it was on the tower, it was on a pole, it was doing the stuff but I was always paired up with a crotchety old, seasoned son of a gun and seen it all and, and he was like, in colorful language, don't do that. Do this.
But when I was a young engineer, I volunteered to run second shift. Nobody wanted to rotate. And they said, well, I'll just take it all year, because my kids were the age I would see him more during the day. So as I'll run second shift, because I knew there was less meetings, so I got changed, and went out with maintenance, you know, every night that I could, and I'd say, here's what I learned at school, how do you really do it? You know, and I learned more there than I mean, not that I learned the technical stuff. But all the things that keep a client running, it was the people on the floor that showed me that
it's always the case. It's always the case. And when I was out in the field, the same thing, it was like, Yes, God, this is the this is the reason why we did it this way. Oh, yeah. It's not suppose yeah, they say it's this way. But this is the reason why we did that. You know, it just is
yeah, that's what you're losing now is yes. Oh, baby boomers and the technicians, the trades, the engineers that are on the floor. They all have their own little soso notebooks, blank books that says, notes on what makes the plant run how I just did it over all the years. Exactly. That's not in a in a CMMS system or anything. That's your own personal notes.
It's not you're absolutely spot on. I just I don't know, I just, every time I say it, I think it's exciting. At the same time, it's a little unnerving. Because I don't have answers. I don't have I still have a bunch of question marks out there. Right. So anyway, how do they get a hold here? Let's say you're talking to somebody and say, Hey, this is how you get a hold of me because they're interested in knowing more about what what's taking place in the university.
first initial last name, so it's a que kblache@utk.edu. I'm pretty good on email.
And pretty good anyway.
Like the thing so but we're having a good time.
All right, once again, we're broadcasting from SMRP. This is the 30th annual and Klaus here was a part of the SMRP in the beginning. 30 A fan.
out take your good liar. And I believe
it's in October of next year.:You're listening to the Industrial Talk Podcast Network.
Another great conversation with Klaus, University of Tennessee. Now I make this recommendation. Because it's important if you have any passion or any desire to get into the reliability, maintenance, asset management world, I highly recommend that you reach out to clubs, all the contact information will be out on Industrial Talk, University of Tennessee. It is a great, great opportunity to really learn a wonderful profession and that's without a doubt. University of Tennessee. Great. The guy the director, Klaus, great guy. He knows a lot right there. He knows a lot. All right. I always say that We're building a platform platform that is truly focused in on education, collaboration, as well as innovation. The world is changing, and it's changing rapidly. And, and the only way that I know me personally, is that you have to be committed to the education, you have to be committed to finding those professionals that you want to collaborate with, so that you can innovate and innovate in a way that creates a resilient business. That's what the Industrial Talk is all about. And that's why we feature all of these wonderful professionals that that are truly open to collaborating, so I highly recommend it. Just go out to Industrial Talk.com. Say, Scott, I want to I want to participate. I want to be a part of it. Just let me know. You'll be talking to me. All right. Be bold, be brave, dare greatly. I say it all the time, all the time. Hanging out with people like Klaus and you will change the world. We're going to have another wonderful conversation coming from SMRP By the way, you need to put that on your calendar SMRP shortly so stay tuned.