Samson Olanrewaju with Fictiv
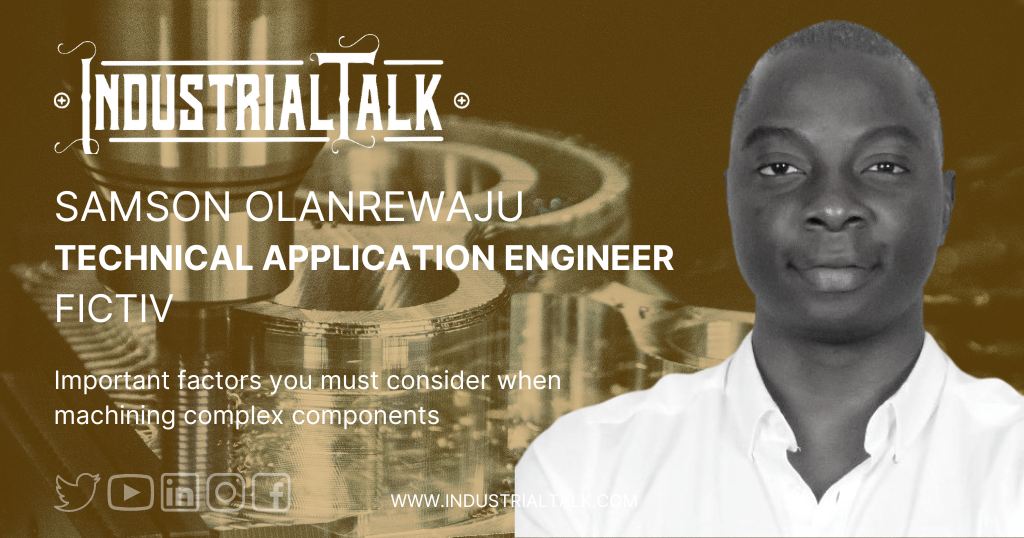
Industrial Talk is speaking with Samson Olanrewaju, Technical Application Engineer – Fictiv about “CNC Machining Complex Components”. Get the answers to your “CNC Manufacturing” questions along with Samson's unique insight on the “How” on this Industrial Talk interview!
Finally, get 10% off your first order at Fictiv.com by entering INDUSTRIALTALK! Learn! Grow! Enjoy!
SAMSON OLANREWAJU'S CONTACT INFORMATION:
Personal LinkedIn: https://www.linkedin.com/in/samson-olanrewaju-34002286/
Company LinkedIn: https://www.linkedin.com/company/fictiv/
Company Website: https://www.fictiv.com/
PODCAST VIDEO:
THE STRATEGIC REASON “WHY YOU NEED TO PODCAST”:
OTHER GREAT INDUSTRIAL RESOURCES:
NEOM: https://www.neom.com/en-us
AI Dash: https://www.aidash.com/
Hitachi Vantara: https://www.hitachivantara.com/en-us/home.html
Industrial Marketing Solutions: https://industrialtalk.com/industrial-marketing/
Industrial Academy: https://industrialtalk.com/industrial-academy/
Industrial Dojo: https://industrialtalk.com/industrial_dojo/
We the 15: https://www.wethe15.org/
YOUR INDUSTRIAL DIGITAL TOOLBOX:
LifterLMS: Get One Month Free for $1 – https://lifterlms.com/
Active Campaign: Active Campaign Link
Social Jukebox: https://www.socialjukebox.com/
Industrial Academy (One Month Free Access And One Free License For Future Industrial Leader):
Business Beatitude the Book
Do you desire a more joy-filled, deeply-enduring sense of accomplishment and success? Live your business the way you want to live with the BUSINESS BEATITUDES…The Bridge connecting sacrifice to success. YOU NEED THE BUSINESS BEATITUDES!
TAP INTO YOUR INDUSTRIAL SOUL, RESERVE YOUR COPY NOW! BE BOLD. BE BRAVE. DARE GREATLY AND CHANGE THE WORLD. GET THE BUSINESS BEATITUDES!
Reserve My Copy and My 25% Discount
Transcript
Welcome to the industrial talk podcast with Scott Mackenzie. Scott is a passionate industry professional dedicated to transferring cutting edge industry focused innovations and trends while highlighting the men and women who keep the world moving. So put on your hard hat, grab your work boots, and let's get
all right what's good. Thank you very much for joining industrial talk a platform dedicated to you industrial professionals all around the world. You are bold, you are brave, you dare greatly you collaborate, you solve problems, and you're making the world a better place. Thank you very much for what you do. And thank you for your continued support. Now Samson is in the hot seat. fictive is the company, and we're going to be talking about CNC machining complex components. Let's get a correction. Yeah, this is this one. This is a paper and pencil conversation. You will get right off the bat. Samson's passion to help you succeed. Right there. He's, he's amazing. And it's an enjoyable conversation, and fictive. I believe Fictiv is really disrupting the way we look and design parts because they're able to provide their platform at fictive.com. That's fictiv.com and go out there and just look around. But the best part about it is if you say hey, give me a 10% discount on my first order. Click on it. Enter industrial talk, boom. 10% discount right then and there. All right. We have no time to waste. Here is Samson. Enjoy the conversation, Samson. Welcome to industrial talk. Thank you very much for finding time in your busy schedule. Really appreciate you sharing your insights and wisdom with the best listeners chips, chips. Can I say that in the universe? Industrial talk. Thank you, man. How you doing?
Pretty good. And thank you so much for having me on your podcast today. I really
am so excited. I got to tie your form. I'm looking at your form that you filled out because listeners I don't create this stuff out. It's all about the individual being interviewed, and what they want to talk about. And I'm excited about this one. Before we get into that conversation there. Samson give us a little background for the listeners to know who you are.
Yes, my name is Samson. Alero I German last name I knew is difficult to pronounce. So you can just call me Samson.
We are but I'm gonna have your full name out on industrial talk.
Oh, thank you. Thank you appreciate it. I can have some good practice pronouncing it. But yes, so my background is in aerospace engineering. I studied aerospace engineering Ukraine. I worked as an aircraft design engineer for almost a decade. And I transitioned into my new role here at fictive as a technical applications engineer, so I manage the technical requirements gathering for the manufacturing of products, especially for the CNC manufacturing processes. And I support our customers to ensure that other products we do manufacture meets their quality requirement. And so that's the role I play right now affected.
But you don't just stay within the aerospace, you're able to sort of take the knowledge that you have the precision knowledge that you have and be able to apply it to pretty much anything that comes across your desk. Right?
Correct. That's the beauty about manufacturing. The fundamentals of manufacturing applies to virtually all industries, right. So currently, I fix a fictive as most people know, it's not an aerospace company, but we also serve the aerospace industry. So, I apply my knowledge not just to the aerospace industry, but as well to the automotive to transportation all across the world. For for engineering industries in general.
For the listeners, please just sort of generally speaking, help us understand fictive
fictive, we like to call it the air b&b manufacturing industries. Yeah, we have a network of manufacturing partners. And we're sort of the middleman we manage that manufacturing process for our customer, we take the burden off of their shoulders. So just to explain in layman's terms, the customers would come to us with their design, we accept those designs, review them ensure that we can meet those quality requirements. And that we send that to one of our manufacturing partners to lead us to manufacture that part. We offer different manufacturing processes CNC 3d prints and injection molding sheetmetal European cast and you name it, and we have over 250 manufacturing partners across the globe. This saves our customers so much time from the supply chain issues of trying to find a partner trying to meet the quality requirement fix it manages all of that. And the good thing about it is the customer does not even have to have any communication whatsoever. With our manufacturing partners. We manage all of that from the beginning of the manufacturing process to the end of it even to meeting the quality requirements.
Say I like that I think that that is a great service solution that you I just I can't poke holes in it. Are you seeing an increase in additive manufacturing for your process?
u have to get a tool in place:Brilliant, because that was when back before 3d printing that was always sort of like, you better get that design, you better get that injection molded. Spot on, don't go make any mistakes and things like that are risks were through the roof. Yeah, exactly. That's, that's brilliant.
That's genius, right, there.
It is. It's genius. All right, let's talk a little bit about CNC machining, complex components. One, what does that mean? What give me an idea of a complex component, and then sort of state that problem statement? What are we dealing with? Okay, talk to us.
Okay, I think overview for us. Let's understand what CNC is. Right. So CNC is a subtractive manufacturing process. And I like to explain things in layman's terms so everyone can understand. Right, amen. So technically, you're taking a tool, and then you're just machining out or removing material from that existing stock material until it creates the patching, right. It's an advanced method of manufacturing. But keep in mind with everything, there's always exceptions, there's always difficulties, there's always challenges and limitations. The CNC manufacturing process has limitations. Because of course, there are different types of money for our CNC machines. There's three axes, five axes and so on.
Just FYI, I went to IMTS. Up in Chicago. CNC is off the charts. Interesting. It's Go ahead.
It's amazing. It is amazing.
Just watch it, stare at it. It's like
just go on YouTube and just watch videos of like them just machine.
Yeah. It's like when you go to a campfire, and you're just sort of staring at this thing spinning around.
Like how is that happening? Yeah, that's impressive. Yeah, so, we would consider anything any manufacturing of competent vaccines, your complex part if it makes it challenging to manufacture it from the CNC manufacturing process, right. So just an example. Um, CNC has limitations. For example, there is a bounding box or bed size, they are tolerance limitations, of course, new CNC machines are being manufactured. Nowadays that can meet really tight tolerances. But then things like tolerances or features on that company that makes it difficult for the CNC to to machine easily or to create, mix that back complex. And then in that scenario, as the designer and the manufacturer, you have to start thinking about either alternative methods of manufacturing that particular part or alternative methods of designing that part. So you could go two ways, you could either go ahead and simplify your design, saw the manufacturer can make it through CNC, or you could all along just change the whole manufacturing process itself.
I have to interject here. What did we do? I mean, the sophistication of today's capabilities, the CNC capable, I just can't imagine there's something that is I can't do it. I mean, they're just constantly coming out with more. How did we sort of operate? In the past when we're tight tolerances, we just sort of, we just couldn't do it?
That's a great question. CNC has been around for four decades now. Yeah. And the thing about technology is this continuous improvement, right, we are tight tolerances that before CNC came out, it was impossible to, to 10 thousandths of an inch, for example, was impossible so so things like that, what a designer would do is you'd have to kind of like play around with what you have in hand, right? If you don't have a process to make it, you have to make a lot of tweaks to your design make sacrifice as much as you can in order to bring that design into reality. Right. And yet, here's the funny thing up front, just from the designing background, working as an engineer, right for for almost a decade now. It kind of like has a weird place on your mind. So to say. It's like you as a designer, you already have an idea of what's available out there, right to make your part. So from the beginning stage, from the conceptual stage, you're already designing with the intent that I know there isn't a tool out there that can make this so I'm not going to bother going in that direction. But now as those tools begin to come into place as those complex high technology comments plays now the designer is more aware that Oh, I can actually stretch the band. So to an extent, right, I could now go in that direction. So it changes, it changes the industry engine
and the reliability of manufactured parts increase because of the tight tolerances. There's just so much it's so much benefit from all of that. So what's so with that saying, We've got, I'm looking at it, give us some of the problems that we are dealing with today?
Yeah, that's a good good question. That there are so many things are so many reasons why apart could be considered complex, but because of time, we'll just talk about a few of them. Yeah, one of which is thin walls, and I'll just put it simple as that thing Well, so, thin walls is imagine you have a competency trying to manufacture right. And then some feature in that company has a thin wall, typically, we would consider something maybe less than 0.5 millimeters for metals or less than one millimeters for plastics thin. Those can be challenging, right? Especially for industries that involve that require a lot of thing was like in the aerospace industry, or in the robotics industry, where there a lot of shells and casings. The issue reason why that is a complex problem is that when the machining to get to that thin wall, right, the heat transfer to the thin wall and the vibration of the tool, make that wall wall, right. And by wall, I mean just that feature on that particular components, such that when it's sent, when you send the part out to say the assembly location of its function, it doesn't function as expected, because it doesn't meet the toners the face there is has some warpage. And the thing about what page is, it's difficult to control. Right? So that is really challenging. And there are multiple ways you can go about that. Well, the question then comes, should we change the design? Or should we change the process? And how can we get that done, there are some scenarios where you cannot afford to change the thickness of the walls on that on that particular company. So you have to think about either change the manufacturing process, for instance, you could change the manufacturing process from just CNC to casting and then CNC. Yeah, you can cast the whole part and that feature that has those thin walls, and then do a finish machining without having to come in contact with that wall, right. Um, the downside to that is while you can meet the requirements of the thin wall, if you require a particular type of line surface roughness, then you still have to machine the wall. Right. So that again proposes another challenge. It's a solution, if you're not concerned about the surface roughness of that pipe, because casting can get you some some level of self assuredness. Sorry, go ahead.
Yeah, you just real quick. The the need for thin wall is that just a strive for reducing weight.
Reducing It could range from reducing weight to assembly requirements, the design intent of that particular complex for the aerospace industry, absolutely. For reducing weights. For the transportation industry, for example, robotics, it would most likely be when you're braking to competence together, and it has to like have a kind of snug fit to another complex and it has to slide in through. So the reasons could vary depending on the industry. Yeah, yeah. And then I would say another another way to mitigate that would be to change the method of machining the pipe. So this, the way that CNC tool goes is it's subtracting material from the bounding box or stock material, you can use the radial depth of cuts approach or the exhale, depth of cut approach the audio CO or atoc. And what that is, is I wish I had a box open, but imagine you have a box, right? And at the fine end, or the latter end of the box, is where the thin wall is, right? What the radio depth of caught approach does in the CNC machining process is instead of taking the tool and just cutting out the stock material, you gradually step it up to the wall. So you could go by sit, take 50% of the material, come back, take 20% Come back, take 5% and then come back, take 1% What happens is it gives the world time to cool down a little bit and the vibration is not instant on that particular one right? gradual process of going back and forth before hitting the thing wall helps limit or helps mitigate the tendency of warpage on that wall, right. Another approach is the actual desktop card. So imagine if the thin wall is in the middle of the pot, right? Yeah. If it wasn't a team wall, the machines can say, You know what, I'm just gonna go ahead and machined out everything on the right side of the stock material and then go ahead and machine everything on the left side, right. But if it's a thing, well, what we recommend is the machines should go ahead and do an actual depth of course So you what he does is he sections out the left the right side, and sections on the left side. And then he goes, cut to a particular depth on the right side, stop, lifted up, go to the left side, currently the depth stop, and then keep on interchanging. Yeah, what happens is the base part has enough rigidity to hold the wall while he's coming down gradually, as opposed to finishing the whole wall on one side, and then switching over to the left side. That makes sense, yeah. Now allows the wall in the middle to manage the vibration coming in and also manage the thermal conductivity as it goes into the wall.
Like that. I like I like that a lot. And and so you've got all these interesting approaches, as I look on your thing, and now we have these, those are some of the solutions, what are some other solutions that you can sort of share with us on some of these, some of the problems that you are like, the complexity of geometry, all of that? How do you guys just, I mean, I mean, let's say I submit something I got effective, I can upload the drawn, I do all that stuff, you guys are to do this, the magic behind the scene, which is doggone cool, no doubt about it. And then you come back and you say, you know, great, little complex, but we could do it this way. And they take us through that. How do you how do you evaluate something like that? When I'm just I'm betting on this on that on whatever it
is? Yeah, that's See, that's why we I recommend people to us fix it, right? Because when it comes to complexity, and I understand this, because I came from the design world, and now into the manufacturing world. So I see both sides, and I see the challenges both sides are facing right. For complex geometries, right? It's, it's critical to involve the manufacturing engineer at the initial stage of your design, right, if you can, and that's one of the things spectative brings to the platform, it's like, you don't have to finalize your design to its highest level of complexity, before thinking about sending out the machine is because what happens then is you've spent hours and days trying to design this stuff. And then you send it to the machine. And the machine says, Hey, we don't have the capabilities to make this like you, you've gone over the top with this right? Having team of engineers effective, lets us help you in that design intent, that design phase where it's like, you're still building your design, we collect, you know, the manufacturing capability is limited with this particular type of tolerance with this particular type of feature. So you might want to change that. So we provide what we call DFM feedback that's designed for manufacturability feedback, we provide that both on a platform and with direct conversations, we get on a call with the customer, we explain to them what the some of the limitations that CNC has, and some of the manufacturing feedback so they can implement the design to make sure that the manufacturing process goes smoothly, right.
What I hear you saying, You're just saying, Okay, I've got to design and I'm all bad i and let's say it's this, this thing right here, and I'm, I'm just nailing it, and I just I can't stop working on it and tweaking it and tweaking it some more. Yeah, what I hear you saying is that I can I can get it there, you can get the concept we can have, and then be able to submit it. Have a conversation because of your network of skilled operations. Yeah, then then you can sit there and go, Okay, this is what you want to do. That is great and fantastic. And knowing full well, when you submit it to your network. It's gonna say, Oh, that's cool. Yeah, great. We can do that.
Exactly, exactly. And it saves them so much time it will line up, right. You see, yeah, Lita. And that's one of the critical things when it comes to manufacture. It's lead time, cost and quality. Right? Yeah, bring into the table. It's like, hey, let's get in a conversation. We have our team of engineers here to help you. We can trash this out in a very quick amount of time, and get this manufactured for you as quickly as possible. What is what's the pushback
on this stuff? Because I just like, for me, maybe I'm your target audience, or target design guy? Because the simple fact that I could save time, that is always like, Yeah, that's great. And the other fact is that I can leverage your expertise to get the right thing at the right time. So that when you submit it, it does it does what exactly what we're supposed to, what's the pushback?
What do you Yeah, that's a good question. And it varies from industry to industry, and not just varies from industry to industry. But it also varies from company to company as well. Of the three factors I just mentioned, lead time, cost and quality. The only thing that's consistent and that's required across all board across all companies across all industry is quality. That's all like that is all that's consistent across board. When it comes to lead time and cost depending on the company, depending on the stage of their production, depending on the project some of them values one over the All right, some might say, Hey, listen, we can pay you a million bucks, just get this for us by tomorrow. And some might say, Hey, listen, we're not in a tight rush for later. And we don't really care about your time. This is a project that's scheduled for six months from now. So right now, we're not really concerned about the leads. And what we're concerned about is the cost. Can you bring this down? So it varies depending on what stage they are in their project, and depending on the company, as well. So there could be that push back on it, depending on what they value at the moment.
But the reality is, is that, you know, I speak to a lot of people and it just want people that they can trust to have a conversation with trusted individuals, because I might not, I need to collaborate, I need to have that conversation to know that I'm doing it right. Because the last thing you want is not to do it right. And it gets frustrating. And it's like, you know, I don't want to get up out of bed because I got to deal with. But the reality is, yeah, it's true. Yeah. And it would be just, I just, I'm struggling, but at least even when somebody says I'm pushing back, because I the lead time is, you know, let's it's down the road away. So let's get it right here, whatever it is, you can still have that conversation.
Exactly. And that's what builds trust. And I believe that's what stand out from the industry is that we have rows with infected that we called Cas, that's a technical applications engineers. These are the guys in fixing that will jump on a call with you anytime. And actually, I am one of those TAs, we will jump on that face to face call on zoom on the phone, you can call us, email us to have that conversation and let you know, hey, listen, we're not just taking your car and sending it off to some random person. We are heavily involved in your project just as much as you are. And we're here to make sure that your project meets your required quality requirements.
But you're also you're taking, you're taking a risk risk position to you're gonna say, hey, we want it right. We're going to work through this. And we'll we'll also work in conjunction with you and make sure that it's right, because we want it to be correct. Exactly. Last thing you want is to say, Hey, Scott got a part that didn't meet any expectations. And that's not good for anybody. Right?
Right. Correct. And that's how we have systems in place, right? We have technical customer support, we have quality documents that we actually send out to the customer, right? Before they get the parts, right. So when the parts are made, we inspect this doc, we inspect this. We say to them, we send them the pictures, hey, look at it, make sure it meets your requirements, they approve it, and then we'll ship it out to them. So we the transparencies, there is what it is. And that is crucial in an industry like
Josh, how do people get a hold of you there Samson,
you could reach out to us directly on website WW the effective.com. There's a chalkboard right at the bottom left corner. Or you could just send us an email directly, Mike? Well, I would have to spell that out. Because in any cocktail
plus, plus, you're out on LinkedIn. And I'll have to add and have all the contact information for Samson. So don't worry. Yeah, don't worry. And
yeah, yeah, how to spell it out today. On the last name. I think I might have to change my last name. So it's easier for people to remember, but
it's okay, Samson, I got the Samson right. It's okay. It's okay. No problem. You are absolutely spectacular. Thank you. Thank you. Thank you very much. All right, losers, we're going to wrap it up on the other side. Thank you very much for joining. Thank you very much for your support. We're going to have all the contact information for Samson out there on industrial talk. You need to reach out to him and you need to reach out to pick up because they're pretty cool people. So thank you very much. We will be right back.
You're listening to the industrial talk Podcast Network.
As always, thank you very much for joining industrial talk and thank you for your continued support. How about that conversation? How about that conversation Samson is the guy that you need to put on your bucket list to connect with victim is the company go out to fictive.com that as FYI, the CT iv.com And I want you to get a 10% discount. You want a quote, you want a 10% discount, you need to go right there. Test drive down. You will not be disappointed. Talk about a lot of passion, a lot of passion that fictive to help solve your problems. All right, people be brave, daring, greatly hanging out with Samson and you're going to change the world. Thank you very much for joining and we're going to have another great conversation shortly. So stay tuned.